Contents
- What This Rebate Means
- How Much Rebate Is Available for Distilleries?
- Assessments and Audits
- Dangerous Goods Hazards for Distilleries
- Common Chemical Hazards for a Distillery
- Dangerous Goods Storage for Distilleries
- Dangerous Goods Handling Equipment for Distilleries
- Dangerous Goods Equipment for Distillers
What This Rebate Means
How Much Rebate Is Available for Distilleries?
Assessments and Audits
Dangerous Goods Hazards for Distilleries
Common Chemical Hazards for a Distillery
Dangerous Goods Storage for Distilleries
Dangerous Goods Handling Equipment for Distilleries
Dangerous Goods Equipment for Distillers
Good news for Victorian distilleries with the announcement of a rebate for equipment and infrastructure that improves chemical safety. The Business Victoria initiative offers a rebate of up to $50,000 for expenditure on eligible safety infrastructure for eligible distillers of alcoholic beverages.
REMEMBER: Distilleries have safety obligations, under the Victorian Occupational Health & Safety Act 2004 (OHS Act), to create and maintain a safe working environment. As the industry grows, it’s vital that distilleries are supported so they can ensure safe chemical management.
What This Rebate Means
The rebate is a welcome incentive for distilleries in Victoria to seek professional advice on the improvement of hazardous area and dangerous goods safety in their operations – and implement the best systems to support this.
While all workplaces with hazardous chemicals and dangerous goods have a responsibility to ensure a safe working environment, distilleries face unique risks that may not be fully understood of controlled. Through the processes of distilling and beverage production, it’s vital that all businesses – whether they’re large or boutique distilleries – have the knowledge and ability to control the chemical risks in their operations.
IMPORTANT: This rebate is part of the Business Victoria $20 million Distillery Door program which aims to develop skills, tourism opportunities and the growth of the industry through investment in infrastructure and safety investment.
A light has been shined on chemical safety in distilleries with the new rebate for Victorian distillers.
How Much Rebate Is Available for Distilleries?
Small distilleries under 10,000 LAL in 22/23 must co-contribute 20% of total expenditure, while large distilleries over 10,000 LAL in 22/23 must co-contribute 30% of total expenditure.
Therefore, the rebate is up to 70% or 80% of the total eligible expenditure (GST exclusive) or up to the maximum of $50,000 (GST exclusive) — whichever is the lesser amount.
Eligible expenditure incurred from 1st April 2023 until 30th September 2024 can be claimed.
REMEMBER: Applications for the Distillery Support – Safety – Hazardous Areas and Dangerous Goods Rebate close at 5pm on 30th September 2024 – or until funds are fully subscribed (whichever occurs first).
Like more info on the rebate? Click here
Assessments and Audits
To be eligible for the rebate, distilleries in Victoria must have either a:
- Hazardous area assessment
- Dangerous goods audit
- OHS essentials program relating to hazardous areas and dangerous goods
- Assessment by a WorkSafe dangerous goods inspector
These assessments, programs or audits are to determine eligible equipment and infrastructure for the rebate. The rebate can be used for the costs associated with a Hazardous Area Assessment or Dangerous Goods Audit.
A rebate is available for Victorian distilleries of alcoholic beverages to improve chemical safety onsite with eligible equipment and infrastructure to minimise risk during the distilling process.
Dangerous Goods Hazards for Distilleries
Due to the multiple classes of dangerous goods used by distilleries – and the prevalence of flammable liquids during the distilling process – workplaces are vulnerable to hazards associated with the chemicals that they are carrying.
Whether it’s through the production process, chemical handling or dangerous goods storage, there are many issues that can impact safety if the proper equipment and procedures aren’t utilised.
There have been multiple accidents at distillery sites due to the manufacture, storage and handling of ethanol as part of operations.
“Ethanol is the primary material used in distilled spirits manufacturing and is a flammable Dangerous Good. Hazardous Areas are established when working with flammable liquids to reduce the likelihood of ignition sources in an area that may have an explosive atmosphere due to the presence of ethanol vapour. These areas are important to define what equipment and processes are suitable for use in these environments to reduce the risk of incident.” - Distillery Door Program Guidelines
Common Chemical Hazards for a Distillery
Some common hazards faced by distilleries may include:
- Ethanol or other flammable liquids igniting
- Instability with temperature sensitive substances
- Chemical incompatibilities creating hazards
- Human harm from exposure through inhalation or contact with the skin or eyes
- Spillage due to improper handling or storage
However, these risks can be effectively controlled by ensuring a risk management strategy that includes the identification of hazardous substances, assessment of the risk, the implementation of controls and the inspection and auditing of these controls to sustain ongoing compliance.
REMEMBER: Dangerous Goods, including flammable liquids, must be handled in a safe manner to control the risk of accidents, which may harm people, plant or the workplace.
Dangerous Goods Storage for Distilleries
To reduce the risk of chemical incidents, there are many dangerous goods storage solutions available through Storemasta for distilleries, wine makers and beverage manufacturers.
Popular dangerous goods storage options include temperature-controlled stores for temperature sensitive chemicals (from $100,000 - $300,000) chemical storage cabinets for indoor storage (from $863 - $7389), a range of outdoor stores to suit every dangerous goods class (from $2607 - $33,920), gas and aerosol cages for any onsite Class 2 dangerous goods (from $522 - $13,232).
*all prices approximate, excluding GST and delivery
Temperature controlled stores for volatile flammable liquids can keep the substances safe, stable and viable.
Dangerous Goods Handling Equipment for Distilleries
In addition to storage solutions, there are a multitude of handling solutions that can reduce the likelihood and impact of a chemical incident. These include gas bottle trolleys, bunded drum dollies, bunded trolleys and dispensing equipment to control spillage.
Dangerous Goods Equipment for Distillers
Are you a Victorian distillery interested in the hazardous area and dangerous goods rebate? There’s some steps you can take if you’re interested in applying:
- Check the website to learn more about the rebate
- Read the guidelines
- See if your Victorian distillery of alcoholic beverages is eligible
- Organise your audit or assessment
- Discuss options for equipment and infrastructure
- Make a copy of all invoices and receipts for eligible expenditure (1st April 2023 to closing date)
- Gather your supporting documents
- Apply for the rebate online
Alternatively, if you require information about chemical storage and handling equipment to minimise risk for your operations, book an appointment with our Dangerous Goods Storage Consultants who can assist with improving site safety at a time that’s convenient for you.
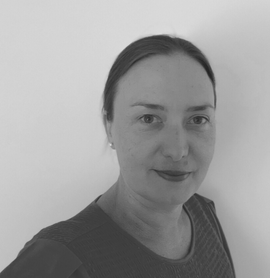
Living life by the 4 C’s of marketing – communication, coffee, compliance… and more coffee – Leisa Andersen is Storemasta’s Content Marketing Manager. When she’s not writing, you’ll find her enjoying all the good things in life, including shopping, travel and gluten free donuts.