What are The Five Whys?
What Kind of Questions Should I Ask to Determine Root Cause?
Understanding Root Case
What Line of Questioning Should I Follow?
Types of Incidents Involving Dangerous Goods
How to Apply Root Cause Analysis to Dangerous Goods
Determining Root Cause to Lower Incident Rate
Here at Storemasta, we talk a lot about risk management and how you can improve health and safety with your dangerous goods and hazardous chemicals. And one of the ways in which you can improve processes is by fully understanding why a problem has occurred in the first place. This is called ‘root cause analysis’ and it’s an important part of maintaining dangerous goods safety for any organisation. Whether it’s a minor incident, such as a leaking drum — or more significant, such as a chemical burn — workplaces should be looking at any issues to make sure that the applicable corrective measures are in place to minimise the likelihood and impact of an occurrence in the future.
The 5 Whys are a technique that’s been adopted by many organisations, to determine the root cause of a problem. As the name suggests, this root cause analysis tool asks the question ‘Why?’ to get to the core of the issue – and allow for a successful resolution.
In this post, we’ll be looking at the 5 Whys and explaining how you can apply this to any dangerous goods or chemical safety issues in your workplace. We hope by adding this approach to your inspection and investigative tasks, you’ll be able to remedy any hazardous situations before they turn into a dangerous incident.
What are The Five Whys?
Before we can apply this tool to dangerous goods, we first must understand what the 5 crucial questions are.
The 5 Whys are asking the question ‘Why?’ – with each answer spurring another ‘Why?’ to determine the reason behind each problem. The Why’s are not necessarily just to be repeated five times, as they can be taken further if necessary to determine the root cause of a problem.
Think of the Whys as a chain of questioning, that digs deeper into the root of the problem with every query.
The 5 Whys starts with asking why there is a problem, then goes step by step through the process, asking why each stage of the process is problematic.
At the end of the questioning, staff should have a clearer understanding of the real issue and be then equipped to move forward with a plan to rectify the problem.
DID YOU KNOW The Five Whys were developed by Taiichi Ohno at Toyota Motor Corporation who achieved phenomenal success through his production systems. Taiichi’s work inspired Lean Manufacturing through his Seven Wastes model that aims to identify waste including non-value-added activity, product defects and unnecessary motion.
What Kind of Questions Should I Ask to Determine Root Cause?
There are endless questions that can be asked when applying the 5 Whys to your chemical safety plan. While you need to remain flexible in your questioning, so that you hone in on the actual core of the problem, there are some simple questions to start you off.
- What is the key issue that needs to be solved?
- How has safety been compromised?
- How did this come to be?
- Is there evidence to support this idea?
- How could this have been avoided?
- What processes weren’t followed prior to this incident?
.
Interviewing staff to determine the root cause of a chemical safety incident should be done in a relaxed, neutral environment where staff feel free to speak honestly.
When interviewing staff, make sure they are in a comfortable and safe environment where they feel free to speak honestly.
Always record meetings or take detailed notes that can be analysed later.
Don’t rely on one person’s opinion, try to get a cross section of information from a variety of sources about the event.
And always remain open minded, as coming in with pre-determined ideas about the root cause of an incident may lead to a biased investigation. Be agile and adapt with the answers, focusing on looking deeper into the cause of the safety issue.
REMEMBER: As workplaces rely on problem solving to improve, health, safety, productivity, efficiency and profits, this root cause analysis technique is a simple solution for workplace investigations. The 5 Whys can provide a succinct and prompt way to determine why something has failed.
Understanding Root Case
The root cause of a problem is the fundamental reason that underlies its occurrence. Successfully identifying the root cause of a chemical safety issue is crucial for effective problem-solving. If determined, it can lead to the safety issue being resolved through a true understanding of the problem, context and all contributing factors.
At Storemasta, we are big believers in risk management and believe that any information gained from errors in the workplace should be thoroughly examined and discussed so staff can create new procedures and processes that prevent the incident from occurring in the future.
It’s important to share this information and to act upon it, otherwise, you could risk health, safety and compliance.
IMPORTANT: To learn more about establishing root cause after an incident with hazardous chemicals or dangerous goods, read our popular blog about causation models.
What Line of Questioning Should I Follow?
The first step is to identify the problem. This needs to occur before using the 5 Whys to determine root cause. Start with a broad query such as:
“What is wrong?”
“What is the health or safety problem you’ve identified?”
“What is the chemical safety issue you’re dealing with?”
This problem will then kick off the 5 queries (or more, if required), beginning with “Why”. You could initially ask:
“Why did that happen?”
“Why did it fail?”
“Why wasn’t it secured?”
“Why was there confusion?”
“Why did they fall?”
“Why did it breakdown?”
“Why was it treated that way?”
“Why was that ignored?”
“Why did that occur?”
“Why was that done in that way?”
Following this query, you can then start by simply asking “Why?” — or provide a more detailed query that specifically relates to the information previously provided by the interviewee. This process is then continued until the underlying cause of the problem is identified.
Types of Incidents Involving Dangerous Goods
Incidents involving dangerous goods can vary widely based on the nature of the goods, the environment, and the circumstances.
Here are some examples of incidents that may occur:
Spills and Leaks: the accidental release of hazardous chemicals during handling or transport; the escape of flammable or toxic gases.
Fires and Explosions: Fires in storage facilities holding dangerous goods; ignition of substances during a spill; battery fires or explosions.
Natural Disasters: Floods creating unstable chemical storage, which leads to pollution and human harm; bushfires threatening facilities and fuelling the fire or explosion risk.
Emergency planning requires consideration to events that may happen infrequently, such as natural disasters and security incidents.
Exposure Incidents: Harmful substances being ingested inhaled or absorbed through the skin or eyes; corrosive chemicals damaging property.
Environmental Pollution: Accidental chemical releases polluting waterways, soil or air quality.
Security Incidents: Theft of hazardous materials, which can be used for illegal purposes; deliberate damage of facilities carrying dangerous goods.
REMEMBER: Emergency planning is a responsibility under WHS law. Each type of emergency incident requires specific response strategies and safety measures to mitigate risks and protect people, property, and the environment.
How to Apply Root Cause Analysis to Dangerous Goods
While the line of querying is specific to the problem at hand, here are a few examples of how to apply the 5 Whys to your operations to get a clear idea of what’s gone wrong.
Problem: Spill
Why? Chemicals spilled into a work area
Why? Staff dropped the drum
Why? The staff member found the drum difficult to carry
Why? There was no handling equipment for the staff to use
Why? The wheel of the drum dolly required a replacement and was unusable
Root Cause
A lack of handling equipment and procedures for drum management puts the workplace at risk of a chemical spill.
Corrective Controls
- Maintain all handling equipment
- Regularly inspect equipment to maintain safety
- Write procedures to ensure safe chemical handling
- Ensure spill procedures are up to date and spill kits are available onsite
- Maintain bunding in storage and handling areas
- Retrain staff in chemical handling to reduce risk
Root cause analysis can help you identify the problem and correct it before it happens again.
Problem: Chemical Burn
Why? Staff received a chemical burn from handling dangerous goods
Why? They were handling them without PPE
Why? Staff could not find the equipment
Why? It was being used elsewhere
Why? We had extra staff on that needed it
Root Cause
A lack of appropriate personal protective equipment has led to unsafe practices with hazardous substances.
Corrective Controls
- Order new PPE that is fit-for-purpose, suitable for the chemicals, tasks and personnel responsible
- Inspect PPE regularly to ensure it’s being cleaned, maintained, stored and used properly
- Develop strict PPE procedures so staff are using the correct equipment at all times
- Implement PPE cabinets near chemical stores so staff have easy access to the equipment
- Ensure emergency decontamination equipment is available and in good working order
- Train staff to use emergency showers and eyewash to reduce impact of exposure accidents
Problem: Fire
Why? A fire began when staff were working with flammable gas
Why? Heat from machinery started the blaze
Why? The machinery was too close to the goods
Why? Space is limited, so staff moved the gas store last week
Why? They didn’t know it would be dangerous
Root Cause
Untrained staff choosing the location of a flammable gas store, and unknowingly placing the store too close to an ignition source.
Corrective Controls
- Develop regular training refreshers for gas safety
- Implement fixed locations for stores
- Write procedures to prohibit staff from moving dangerous goods stores
- Prohibit machinery or igintion sources from coming within set distances of gas stores
- Undertake weekly inspections to check all ignition sources and separation distances
Determining Root Cause to Lower Incident Rate
If you’d like to learn more about reducing risk in your operations, why not access our easy-to-read eBook. This book highlights how to undertake an investigation of a hazardous chemical or dangerous goods incident, so you can better manage the various risks in your organisation. Get your copy of the free guide today.
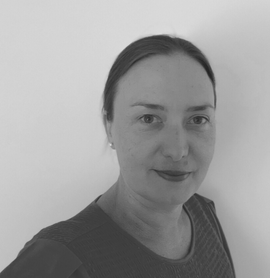
Living life by the 4 C’s of marketing – communication, coffee, compliance… and more coffee – Leisa Andersen is Storemasta’s Content Marketing Manager. When she’s not writing, you’ll find her enjoying all the good things in life, including shopping, travel and gluten free donuts.