Contents
- Understanding Flammable Liquids Fires
- Class 3 Chemical Safety Data Sheets
- Ignition Sources
- Source of Ignition
- How Can You Prevent Fire From Flammable Liquids?
- What are the Control Measures for Flammable Liquids
- Fire Safety and other Dangerous Goods Stores
- The Cost of a Flammable Liquids Fire
- Protecting Your Business From Flammable Liquid Fires
Understanding Flammable Liquids Fires
Class 3 Chemical Safety Data Sheets
Ignition Sources
Source of Ignition
How Can You Prevent Fire From Flammable Liquids?
What are the Control Measures for Flammable Liquids
Fire Safety and other Dangerous Goods Stores
The Cost of a Flammable Liquids Fire
Protecting Your Business From Flammable Liquid Fires
The key to fire prevention is understanding exactly how a fire can get started and burn. In this post, we’ll detail all the important points you need to understand about fires that involve flammable liquids. We’ll discuss ignition sources, workplace and community safety, combustible materials and the costs involved with flammable liquid fires.
Understanding Flammable Liquids Fires
What causes Class 3 flammable liquids to burn?
Many people don’t know that the liquid form of Class 3 Flammable Liquids isn’t actually what burns in a fire. It’s the flammable vapours from the liquid chemical that actually ignite and sustain the blaze.
To fully understand how flammable liquids create fires, you need some background knowledge on Class 3 Dangerous Goods.
Class 3 Chemical Safety Data Sheets
It’s a good idea to become familiar with the properties of your flammable liquids. This means you’ll have to dive into your current safety data sheets to learn more about:
It’s a good idea to become familiar with the following:
-
Flash point: this is the temperature range in which the chemical will burn. Your fire risk assessment should consider if the chemicals you hold onsite are used or stored at temperatures inside the flashpoint range. For many common flammable liquids (eg, petrol), the flashpoint is normal room temperature.
-
Flashback: flammable liquids emit vapours that are heavier than air. When a chemical container is opened (or if chemicals spill) vapours can travel long distances and remain flammable. This is called flashback. Your risk assessment should consider work operations (or unplanned incidents) that could produce a flammable vapour trail.
-
Auto-ignition: most flammable liquids have an auto-ignition temperature. Chemicals used or stored within their auto-ignition temperature range don’t need an ignition source to ignite. Your risk assessment should consider if the chemicals onsite could reach their auto-ignition temperature (eg, could an unventilated cabinet stored outside in the sun reach the auto-ignition temperatures).
-
Explosive range: flammable liquids also have an explosive range. When vapour concentrations and temperatures are within a certain range, if ignited the flammable liquids will explode. Your risk assessment should assess the possibility and likelihood of chemicals reaching their explosive range.
Ignition Sources
Once you have a solid understanding of the conditions that could produce a flammable liquids fire, you should then identify possible ignition sources.
Under Section 355 of the WHS Regulations, Australian workplaces have a responsibility to ensure that ignition sources are not brought into work or storage areas that contain flammable liquids.
When it comes to storing or handling flammable liquids, learning how to identify and eliminate ignition sources is crucial for the safety of your organisation.
Source of Ignition
What potential ignition sources are present at your job site? When it comes to storing or handling flammable liquids, learning how to identify and eliminate ignition sources is crucial for the safety of your organisation.
The Australian Standards offer us this definition of an ignition source:
A source of energy sufficient to ignite a flammable or explosive atmosphere. Examples of ignition sources include naked flames, hot surfaces, exposed incandescent material, electrical wiring arcs, mechanical or static sparks, hot particles, electrical discharge, and electrical or mechanical equipment not suitable for use in hazardous locations.
You must apply this definition to the equipment, machinery and processes in your workplace where flammable liquids are carried.
Remember, Class 3 Flammable Liquids are extremely volatile substances that can easily ignite and cause fast-burning and intense fires. You must identify and control ignition sources, ensuring they are not located within 3 metres of your flammable liquids. That includes any work areas, such as waste management vicinities or personal workstations, where flammable liquids may be stored, handled or transferred through.
Let’s examine some commonly found ignition sources, so you can identify and eliminate them from your flammable liquid work areas:
- Naked flames: matches, lighters, bunsen burners, pilot lights.
- Hot surfaces: cigarettes, hotplates, welders or flame cutting equipment, machinery that has overheated or malfunctioned, friction from loose belts and worn bearings.
- Exposed incandescent materials: incandescent light bulbs, halogen lights.
- Electrical wiring arcs: loose wiring and faulty electrical connections.
- Mechanical or static sparks: grinders, electric drills, spark ignition systems, hand tools.
- Hot particles: welding slag and hot metals.
- Electrical discharge: power points, light switches, static electricity.
- Electrical or mechanical equipment not suitable for use in hazardous locations: non-flameproof electrical cables, cords, switches, lights, connectors or fittings.
Controlling Risk of Flammable Liquid Fire
Using the Hierarchy of Controls, we can offer a framework for how you can control risk in your workplace. This includes the control of flammable liquid fire risks.
To control the risks associated with flammable liquid fires, you should first look for ways to eliminate and substitute your business’ dangerous goods.
Apply Elimination and Substitution Controls
To control the risks associated with flammable liquid fires, you should first look for ways to eliminate and substitute your business’ Dangerous Goods.
If there is no feasible way for you to eliminate Class 3 Flammable Liquids from your business, then you should consider using chemicals with a higher flash point. By substituting your flammable liquids for chemicals with a higher flash point, you’ll be reducing your risk of ignition.
A few quick examples (for demonstration purposes only) of substitution may include:
- Switching to water-based paints.
- Using electric-powered forklifts instead of diesel.
- Purchasing diesel outdoor appliances instead of petrol fuel.
Minimise Chemical Quantities
The next step in fire prevention is to minimise the quantities of flammable chemicals that you have in your workplace.
This can be achieved in two ways: First, implement a solid purchasing policy and develop supply chain relationships so you can order smaller quantities of chemicals, more often. Second, keep only immediate requirements in work areas (eg, labs and warehouses), store the remainder of the flammable liquids in an isolated outdoor store.
If it is practical to do so, you can minimise the quantities of Class 3 Flammable Liquids that you have in your organisation.
Control Combustible Materials
Once a fire has been lit, it requires both oxygen and fuel to continue burning. ‘Fuel’ refers to the flammable and combustible materials that sustains a fire.
Once ignited, a fire requires both oxygen and fuel in order to keep burning.
Some examples of fuel (combustibles) may include:
- Flammable and combustible chemicals.
- Vegetation, tree litter and plant debris.
- Refuse and waste stations.
- Pallets, plastic containers, IBCs, packaging materials, and plastics.
- Office equipment, documents and files, stationery, IT hardware.
- Cleaning utensils, hand tools, toilet paper, PPE, uniforms, signs, rags etc.
Any fire prevention strategy must acknowledge the types and quantities of combustible items at the job site. You must then look at ways to minimise, secure or remove these combustible items completely.
Remember, the principles of elimination and substitution (risk) controls can also be applied to combustible items and materials.
Here are some suggestions:
- Remove wooden cupboards (or combustible shelving) and replacing with stainless steel cabinets (shelving) to store combustible sundries (PPE, brooms, rags).
- Increase the frequency of waste removal from the jobs site.
- Keep combustible items away from flammable liquids and other dangerous goods stores.
- Minimise paper files and store archives digitally, or in the cloud.
- Use fire-resistant construction materials where possible.
Implement Good Housekeeping
Good housekeeping in your workplace can assist in fire prevention and risk control. This means implementing a system to ensure that the workplace is kept tidy, with flammable liquids handled and stored correctly, and combustible materials kept away from your Class 3 dangerous goods.
Inspecting and maintaining your flammable liquids stores will help you reduce the risk of a fire.
Here are some simple housekeeping guidelines:
- Never storing combustible materials (archive boxes of files) and refuse (even temporarily) in escape routes (walkways, corridors, stairways, foyers).
- Regularly inspect unoccupied areas of the job site (eg, storerooms, empty offices, basements) — don’t allow them to become a dumping point for non-essential combustible materials.
- Inspect and maintain all chemical storage equipment to ensure that there are no excessive vapours or spills. Ensure that storage areas are kept clean and organised, so that any maintenance issues can be easily noticed — and promptly rectified.
- Clear undergrowth, tree debris and dry grass from wastelands on adjoining properties (if possible).
- Reduce tree litter onsite (and around the perimeter fences). This includes regularly clearing roofs, guttering and vents of combustible debris .
How Can You Prevent Fire From Flammable Liquids?
Our team always recommend carrying out a risk assessment if your workplace carries Class 3 Flammable Liquids.
When conducting your workplace fire risk assessment, you will need to gain an understanding of a range of factors that may contribute to the likelihood and severity of a flammable liquids fire.
REMEMBER: Risk assessments are an essential step in a compliant Risk Management Methodology that systematically identifies, assesses, eliminates (or controls) and reviews each chemical hazard at the workplace.
Your risk assessment should consider:
- Physical properties of the chemicals and how they could ignite or explode. Eg, flashpoint, auto-ignition temperatures, explosive range, incompatible substances.
- Overall site conditions that could support or intensify a fire. Eg, combustible materials, neighbouring vegetation, reactive or oxidising chemicals also kept onsite, other Dangerous Goods stores.
- Quantities of flammable liquids and the potential size/reach of a fire. Eg, 6 tins of enamel paint kept in a flammable liquids cabinet vs 2,000 litres of unleaded petrol kept in bulk tanks. Could the fire impact the whole site, or be quickly contained?
- Location of flammable liquids stores in relation to workplace operations. Eg, 4 drums of fuel sitting outside on an unbunded pallet near the loading dock — vulnerable to forklifts, delivery vehicles and tampering.
- Likelihood of a fire occurring at different areas of the jobsite. Eg, chemicals decanted from fuel drums once a week vs once a day.
- Fire protection equipment and emergency procedures in place at the worksite. Eg, mandatory inductions and reviews, fire evacuation drills and fire equipment training.
- Attitude and awareness of workers toward fire safety and prevention. Eg, workers always wear PPE, report system failures, and are proactive about fire safety.
What are the Control Measures for Flammable Liquids
However, without even conducting a risk assessment, you could easily implement the following safety measures:
- Storing flammable liquids in a Class 3 Flammable Liquids cabinet.
- Locating the cabinet away from electric tools, power sockets, furnaces, heaters, electronics that can discharge static electricity, machinery that could create friction, sparks, or heat.
- Banning smoking and personal electronics within 5 metres of flammable liquids stores.
- Restricting workplace activities (eg, welding, vehicular repairs, deliveries, forklift loading) near safety cabinets and chemical stores.
- Keeping the lids on chemical containers when not in use.
- Controlling the use, storage and disposal of rags that have been used to clean up flammable liquids.
- Ensuring spilled chemicals are contained and cleaned up immediately, with flammable waste disposed of safely and carefully.
- Ensuring workers and maintenance contractors use only tested electrical tools and don’t overload circuits.
- Replacing electric and gas heaters with central heating.
- Carry out preventative maintenance on plant and machinery. Eg, clearing dust and refuse from vents on machinery — clogged vents can cause the machines to overheat.
- Training staff to understand the hazards associated with onsite chemicals
Fire Safety and other Dangerous Goods Stores
What incompatible chemicals and substances do you have onsite? Once a fire has started burning, and it has plenty of oxygen and fuel, it will intensify if it penetrates other chemical and Dangerous Goods stores.
Therefore, you must carefully consider where you use and store:
- Oxidisers
- Organic Peroxides
- Explosives
- Gas cylinders
- Unstable substances
The Cost of a Flammable Liquids Fire
A flammable liquids fire could impact your workplace in many ways, including:
- Human costs: during a flammable liquids fire evacuation, there may be a threat to the safety of staff, as well as fire and emergency responders, site visitors and members of the public. Physical harm, mental and emotional trauma, rehabilitation and loss of income are just some of the human costs associated with incidents such as workplace fires.
- Health hazards: burning materials (eg, plastics) and chemicals often produce toxic gases and smokes — very often carbon monoxide, hydrogen cyanide and nitrogen oxides.
- Community impact: fires can damage public buildings and community facilities, but also cause public interruptions to essential services like electricity, water, gas and broadband.
- Financial costs: of course, there are financial costs associated with the damage to buildings and property. But it’s also important to consider the interruptions to production and trade, as well as the time lost during rebuilding. Other financial burdens can include an increase in insurance premiums and workers compensation, penalties from your WHS Regulator and loss of business reputation.
- Property loss: chemical fires can quickly lead to the destruction of buildings, operating plant, machinery, files and data, computer servers and IT hardware. Even with insurance, the loss of data, production equipment and raw materials can be the end of many businesses.
- Environmental damage: fires that escape into native forests, parklands, or agricultural properties can destroy crops, kill native wildlife and livestock. Fires can force the long-term closure of national parks or nature reserves, and limit community access to other public places.
Protecting Your Business From Flammable Liquid Fires
As we’ve highlighted in this post, there are multiple steps you can take to reduce the likelihood and impact of a flammable liquids fire in your workplace. Identifying and assessing your risk, as well as controlling them, are key considerations when bringing flammable liquids onto a job site.
If you’re serious about preventing the flammable liquids at your job site from igniting or contributing to a workplace fire, why not download free eBook Essential Considerations When Storing Flammable Liquids Indoors? Our book is a comprehensive guide that will lead you step-by-step through selecting and installing a fully compliant flammable liquids cabinet at your workplace.
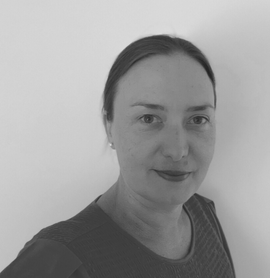
Living life by the 4 C’s of marketing – communication, coffee, compliance… and more coffee – Leisa Andersen is Storemasta’s Content Marketing Manager. When she’s not writing, you’ll find her enjoying all the good things in life, including shopping, travel and gluten free donuts.