Flammable liquids, such as petrol, diesel fuel, acetone and benzene, may be common in many workplaces — but they are still classed as Dangerous Goods. These chemicals have the potential to burn, explode, emit hazardous vapours, and react dangerously with other substances. Whether you carry small or large quantities of flammable liquids, you need to ensure that they are handled and stored carefully to avoid such incidences occurring in your workplace. If flammable liquids aren’t used or stored properly, these chemicals can damage or destroy property, pollute the natural environment, harm the health of workers or cause fatalities. In this blog, we’ll offer our advice on how to effectively manage the many risks associated with flammable liquids through taking a risk management approach to your Dangerous Goods areas.
But first, let’s look at risk management and why it’s so important when dealing with workplaces that carry any type of Dangerous Goods.
So, What Exactly is Risk Management?
Keeping your workplace safe requires focus as well as consistent and deliberate action. Risk Management is a practice that is used in all areas of a business to:
- identify potential risks and threats
- assess their capacity for harm
- take the necessary steps to reduce the risk (or eliminate it completely)
REMEMBER: If it is possible in your workplace, you should aim to first eliminate the risk entirely from your organisation. When this is not achievable, you should then move on to the next steps in the Hierarchy Of Controls. These include considering if you can find a suitable substitute for the hazard, before implementing engineering and administrative controls, and finally, protecting staff with PPE.
Risk management can be used to manage a vast range of risks associated with your business. You can apply this process to areas such as:
- Legal compliance
- Supply chains
- Cash flow
- Staff retention
- Software upgrades
- Workplace safety
- Management of hazardous chemicals
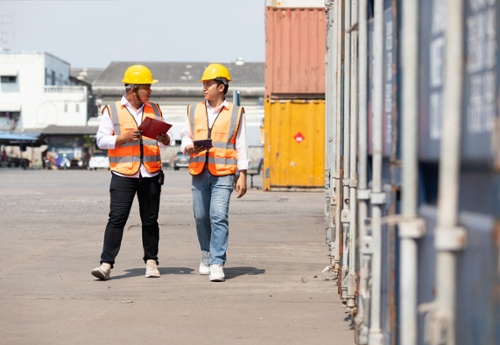
Risk management can be applied to any area of your business including workplace safety and the management of Dangerous Goods and hazardous chemicals.
In Australia, risk management is a mandatory practice under the WHS Regulations in each state and territory. The risk management approach can be used to minimise (or eliminate) all work health and safety risks, but in practice would be broken down into manageable sub-sections.
For example:
Your HSE Manager might apply risk management to all the hazards in the warehouse (eg, chemicals, manual handling, plant and machinery, electrical hazards), or they might apply risk management to a single hazard class across the entire job site (eg, flammable liquids).
Risk Management vs Risk Assessment vs Risk Control
You’ve probably heard the terms risk assessment and risk management and risk control. These terms are often interchanged, but they refer to three different things.
Let’s apply each of the three terms to flammable liquids:
- Risk Management - is a method or approach to ensure that all hazards at your worksite are systematically identified, assessed and controlled, as well as periodically reviewed. Eg, your HSE Manager implements a 4-STEP risk management methodology to ensure the Class 3 Flammable Liquids at the job site are stored in compliance with Australian Standard AS1940:2017.
- Risk Assessment - is an action taken to identify individual hazards and assess the level of harm they could cause. A risk assessment is an essential part of a risk management methodology. Eg, you inspect the flammable liquids storage areas and notice that fuel containers are being left on top of safety cabinets instead of being put away inside. You discover the flammable liquids cabinet is also being used to store workers’ PPE — leaving no room for the flammable liquids. Your assessment determines this is creating a high risk of fire and chemical exposure.
- Risk Control - is a measure you implement to control individual hazards. Eg, you purchase a dedicated PPE cabinet and issue a housekeeping procedure requiring PPE and flammable liquids to be separated and put away in different cabinets. You also meet with supervisors to ensure they enforce this policy
How To Implement A Risk Management Methodology
To ensure your flammable liquids (as well as other hazardous chemicals and Dangerous Goods) are in compliance with Australian WHS Regulations, we recommend using Storemasta’s 4-step risk management methodology.
Our risk management methodology is as follows:
STEP 1: IDENTIFY
Conduct a site inspection and identify all the flammable liquids you carry at the job site. Record the chemical quantities, container types and sizes, plus the storage location. Note any hazardous practices, damaged equipment and overloaded stores.
STEP 2: ASSESS
The next step in your risk management methodology is to carry out a risk assessment to evaluate the level of risk created by the flammable liquids and each chemical hazard they have created. For full details of how to conduct a risk assessment, please refer to the next section in this blog.
STEP 3: CONTROL
In order to control the hazards that you’ve identified, you should aim to find a way to eliminate each of the identified chemical hazards. If this is not possible in your workplace, you may consider implementing suitable risk control measures while applying the Hierarchy of Controls.
STEP 4: SUSTAIN
The final step in the methodology is to carry out post-installation inspections and testing to verify the controls are set up and working correctly. You should implement systemised monitoring and reviews to ensure that new hazards aren’t being introduced — and each chemical control remains effective.
How Should You Conduct a Risk Assessment on Flammable Liquids in Your Workplace?
As we outlined in the previous section, a risk assessment forms part of a full risk management methodology. It’s the important process of evaluating individual chemical hazards — and assessing how much harm they could cause.
Let’s now take a quick look at how you might carry out a risk assessment on your stores of flammable liquids. Please note that this is just a basic example to illustrate the risk assessment process and should not be used as a complete model for your own chemical risk assessments.
During your risk assessment, you should consider the following points:
Determine the health and physical hazards associated with each chemical
Eg, petrol is highly flammable, can explode at certain temperatures/ concentrations. It’s corrosive to the skin and eyes and is carcinogenic. Petrol is also a mutagen and toxic to aquatic life. This chemical also emits hazardous vapours that can result in asphyxiation, human harm, fire and explosion. Petrol may react dangerously with incompatible substances or materials.
List the type of hazardous events or injuries the chemical could cause
Eg,a petrol fire could potentially break out in the lab. Fuel could be spilled by staff at the decanting station causing health issues or fire. Staff may succumb to hazardous vapour exposure at the fuel depot.
During your risk assessment, you should list the hazardous events or injuries that a chemical, such as fuel, could cause.
Assess the potential for damage
Eg, a petrol fire could destroy the lab and place 10 workers at risk of fatal injuries. A fuel spill could escape into waterways and kill aquatic life. Vapour exposure could cause respiratory complications, asthma and cancer.
Evaluate the likelihood of each hazardous event occurring
Eg, petrol is used once per week in the lab. Decanting is done twice a week. Workers at the fuel depot are exposed to fumes at least 6 hours per day.
Create a chemical control action plan which prioritises the chemical hazards with the highest level of risk
Eg, your action plan might flag the vapours at the fuel depot to be the hazard with the highest risk of harm because the exposure is continuous. The other hazards, including fire and explosion, would be addressed, but the vapour hazard would take priority as it is the most likely to occur.
How to Apply a Risk Management Methodology to Your Dangerous Goods
We’ve written this blog in an easy-to-understand format, so you can easily take the information in this blog and apply it to your own Class 3 Flammable Liquids storage and handling areas. We hope you can gain an understanding of how to better manage flammable liquids at your workplace or job site by applying this risk management approach. Would you like further details on chemical risk reduction? Essential Considerations When Storing Flammable Liquids Indoors contains all the information you need to select, install and maintain an indoor flammable liquids cabinet. Safety cabinets are proven risk control measures that are widely used across a broad range of industries and workplaces. Find out how storing your flammable liquids in this manner can help you reduce your risk. Access your copy of our guide for free today by simply clicking on the image below.
Joining the team as a Dangerous Goods Storage Consultant, Melissa Hampton became Storemasta's Marketing Manager in late 2021. With extensive knowledge and experience in chemical compliance, Melissa is responsible for leading the Marketing team and helping shape their marketing strategy. In her spare time, you can find Melissa hiking, swimming and enjoying the great outdoors in beautiful north-west Tasmania.