An effective HAZCHEM risk assessment is only possible when all chemical hazards have been properly identified. Chemicals often bring multiple hazards to a job site and your risk assessment should evaluate individual hazards as opposed to a single chemical. This blog recommends four clear steps to follow when carrying out your chemical risk assessment.
1. Identify both physical and health hazards
The first step involves looking at the physical and health hazards associated with the substances you have onsite. There are two types of hazards:
- Physical hazards, which exist when a chemical can burn, ignite or sustain a fire, explode, or react dangerously.
- And Health hazards, when a chemical can damage the health of humans, aquatic life, animals, or the environment generally.
At this stage you are merely identifying the chemical’s potential for harm, and it is important to remember that you cannot assess a physical or health hazard in isolation.
EXAMPLE: You are using a liquid concrete cleaner which is corrosive to metals, skin, and eyes. It should not be inhaled, swallowed, ingested, or allowed to directly contact the skin and eyes. The substance is non-flammable but it can react violently with aluminium and zinc, creating an explosive hydrogen gas.
2. Identify everywhere the chemical is used or stored
Once you’ve identified the hazardous properties of the chemical you will need to evaluate the ways the chemical is used, stored and handled. You’ll be looking at every point to see how the chemical could contact the skin, eyes, incompatible substances and metal; or be inhaled or ingested.
From our example in section 1, you might identify the following:
- Chemical arrives at the worksite in a cardboard carton containing 8 plastic containers. Each container has an plastic screw-top lid. Orders are usually 3 boxes at a time and stretch wrapped together.
- The boxes are carried by hand on the worker’s shoulder (stretch wrap in place). The boxes are separated and the containers put into the corrosives cabinet at the back of the warehouse. The cabinet is made of polyethylene and has no metal componentry.
- When required to clean the concrete driveway in front of the warehouse, a container is removed from the cabinet and poured into a plastic bucket already full of water. Water is taken from a tap outside the warehouse near the emergency shower. The bucket has a metal handle. Workers wear gloves, masks and aprons.
- According to the SDS, the chemical must always be poured into water (and never first). There is a verbal understanding of this but no documented procedure.
- After use, excess chemical is poured down the drain near the tap — it is the same drain that serves the safety shower.
- Container is placed back in the store with the cap in place.
- Empty containers and soiled PPE are thrown into the general waste area.
Your list might also include the number of workers who come in contact with the chemical, the concentration levels, how often it is received/put away/diluted/applied to concrete, as well as other substances/work procedures being conducted while the concrete is being cleaned.
3. Identify potential dangerous events, illnesses or injuries
Once you have a list in place you can then expand on that list by including each way the hazardous properties of the chemical could create a dangerous event, illness or injury. As a simple example you might determine that:
- If a plastic container is damaged in transit or dropped during loading/unloading/carried to the warehouse, the chemical would leak and potentially contact the worker’s skin or eyes.
- Workers could contact the chemical while pouring into the bucket for dilution. They could drop the container or spill undiluted chemicals direct from the bottle onto their skin, chemical could splash up into their eyes from the bucket.
- A violent reaction can occur if the chemical is poured into the bucket and water added at pressure.
- Corrosive chemicals poured down the drain of the safety shower could contaminate the shower station and make it unsafe for use in an emergency. It could also create an environmental hazard.
- Waste is unregulated so discarded empty containers and soiled PPE will have chemical residue and could contact aluminium or zinc in the waste area. This could create a dangerous reaction.
- Chemical containers put back into the corrosive store may have residue on the outside, potentially burning another worker or causing a build-up of fumes in the cabinet. There is no documented procedure for cleaning chemical containers or checking that caps are properly in place.
4. Identify the severity of each dangerous event, illness or injury
Even though you have a long list of potential hazards, you’ll also want to make a realistic appraisal on the severity if an incident did occur. As well as the likelihood of it happening. From our example you would be considering:
- If undiluted chemical did reach a worker’s eyes, what could actually happen? Irritation that will disappear after the eyes are flushed with water? Severe pain and hospitalisation and a real danger of permanent blindness?
- How hazardous to the environment is the chemical? Is it actually acceptable to pour it down the drain?
- What incompatible substances are kept onsite. If the discarded containers and soiled PPE did contact an incompatible material or substance what could happen? Could an volatile gas explode and cause a fire in the refuse station?
Depending on the hazard class of the chemical, the quantities, and way it is being used, you may have to put in place a number of measures to control each hazard created by the chemical.
Chemical Risk Assessments and Hazard Management
For a complete understanding of the HAZCHEM risk assessment process and how to effectively evaluate the level of risk to your business, we recommend downloading our free eBook How to manage the risk of Hazardous Chemicals in the workplace. We introduce the STOREMASTA risk management methodology and detail how to use it in your own workplace. Download and read it today by clicking on the image below:
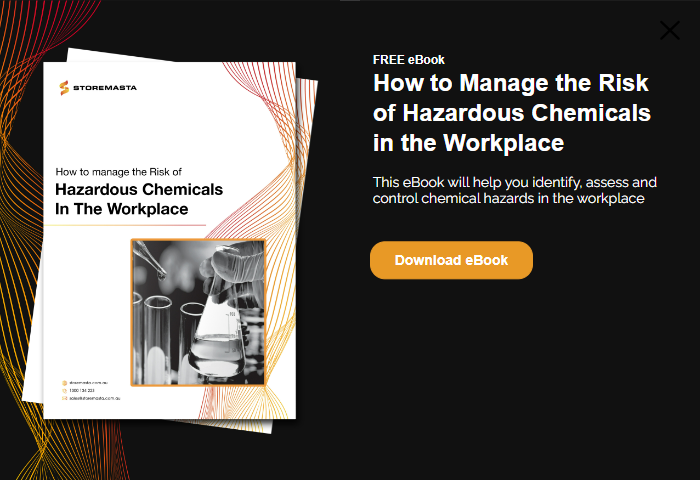
Joining the team as a Dangerous Goods Storage Consultant, Melissa Hampton became Storemasta's Marketing Manager in late 2021. With extensive knowledge and experience in chemical compliance, Melissa is responsible for leading the Marketing team and helping shape their marketing strategy. In her spare time, you can find Melissa hiking, swimming and enjoying the great outdoors in beautiful north-west Tasmania.