Are you new to the subject of chemical safety in the workplace? Or are you concerned that you’re not ticking all the boxes with chemical compliance? In this post, we share some of our top do’s and don’ts for chemical safety, so you can create a workplace that’s actively minimising risk and improving health and safety.
DO: Install Bunding and Bunded Storage
If you’re carrying substances in the workplace that are hazardous or classed as dangerous goods, your bunding can be the difference between an accidental chemical release — or a serious accident.
From flammable liquids to corrosive chemicals and toxic substances, there are a range of risks associated with dangerous goods – and these are only amplified when there is a workplace leak or spill.
Spills can happen almost anywhere where chemicals are generated, used, transferred or stored. Leaks and spills should be contained by an effective spill containment system that includes the provision for a fast and safe clean-up.
Bunding provides workplaces with a physical barrier capable of containing a chemical leak or spill. The spill bund capacities for your dangerous goods are detailed in the relevant Australian Standard. The capacity of your bund is an important consideration as the bunding must be able to contain the spill, not just slow it down.
Bunding, when it’s installed correctly and maintained properly, prevents accidental releases of chemicals from travelling into other areas of the workplace — or out into the natural environment. It also gives staff time to action the spill response plan.
Whether it’s floor bunding in a warehouse or a spill containment system build into the bottom of a cabinet, installing compliant bunding is one of the key measures you can take to improve chemical safety — and decrease the risk of human harm, property damage and environmental pollution.
DON’T: Forget To Clean Up After Spills and Leaks
Many substances produce gases and vapours when they’re not contained in secure chemical packages.
In the event of a leak or spill, these vapours can travel throughout a workplace, sparking a range of safety issues range from ignition to asphyxiation.
It’s important to include clear instructions on spill clean-ups as part of your spill containment system. When a leak or spill occurs, authorised staff must be able to quickly deal with the situation.
This will include:
- Containing the spilled chemicals
- Not allowing unauthorised staff within the spill site
- Cleaning up the liquids and resulting effluent
- Decontaminating the area
- Neutralising the area (if applicable to your chemicals)
- Disposing of the waste accordingly
- Reviewing the incident; making adjustments to any handling or storage procedures
Don’t forget to implement a spill clean-up procedure that includes the correct disposal of spilled chemicals and any resulting effluent.
DO: Segregate Incompatible Chemicals
If you’ve been reading our blogs for some time, you will have learned about the dangers of handling and storing incompatible substances.
Across the 9 classes of dangerous goods, there are many substances that are incompatible and must be segregated to ensure chemical safety.
Segregation can be actioned in one of two ways:
- By choosing compliant storage that offers built-in segregation; or
- Adhering to the segregation guidelines (separation distances) for your dangerous goods
As space is often an issue in workplaces, many businesses choose to store their chemicals in cabinets and containers that offer segregation from other incompatible substances. By doing this, you don’t have to follow the separation distances that apply to stores of incompatible substances.
DON’T: Overlook Risks Associated with Handling and Transfer Tasks
While you may have your stores in order, incompatible substances can still be a risk if diligent transfer and handling practices aren’t implemented.
All staff must be trained to understand the importance of chemical segregation, in both the handling and storage of their dangerous goods.
Using incompatible chemicals in the same work area could result in serious safety issues, such as chemical reactivity or hazardous vapour emissions. Therefore, it’s vital that staff know the class and hazards associated with their chemical products, as well as any guidelines for dangerous goods segregation that applies to that class.
REMEMBER: There are some classes of dangerous goods that may be incompatible with substances within their own class. Find out more about incompatible dangerous goods by downloading our free segregation chart.
DO: Display Correct DG and Hazard Signage
So far, we’ve spoken about the chemical controls that you can implement and maintain to improve onsite safety. However, how can staff keep their organisations and team members safe from chemical risk if they’re not aware of the dangerous goods that are being kept in their workplace?
Dangerous goods and hazard signage is not just a WHS obligation, it’s a visual warning sign for staff, contractors and visitors that alerts them to potential chemical risks.
It’s your responsibility to ensure that you have the correct dangerous goods signage installed in storage and handling areas. Dangerous goods signage is generally the DG diamond that illustrates the class of chemical that you have onsite.Hazard signage is additional signage that highlights the physical or health hazards associated with the substance – and the precautionary measures that personnel should take when entering that area.
Examples of hazard signage include the DANGER Chemical Storage, DANGER No Smoking, No Ignition Sources within 3m, and Corrosive Material signs. These signs must be installed, along with your DG diamond, in all appropriate storage and handling areas in your organisation.
DON’T: Forget to Replace, Update or Maintain Signage
Whether you’re keeping chemicals indoors or out, signage can be affected by age, impact damage or the elements. Signage may also go missing or be wrongly allocated to a work zone.
To comply with WHS Regulations, you must ensure that your signage is in good condition and clearly visible at all times. This means that any damaged or missing signage be replaced with the relevant dangerous goods diamond or hazard sign.
If you’re ordering new chemicals for your site, make sure that you have the controls and the signage in place before it arrives at your workplace. From the time the chemicals are delivered to your site, you must be able to alert staff to the potential hazards – as well as decrease chemical risk.
Don't forget to replace or update your signage as this can increase risk in your workplace.
DO: Install Compliant Dangerous Goods Storage
The hazards associated with your chemicals are particular to the dangerous goods class or sub-class of those substances. Therefore, to properly store and segregate your products, you require compliant chemical storage suitable for the substance you’re looking to store.
Not every chemical has the same DG class, regardless of whether it’s the same product from another supplier or a new version of an old product. To determine the class and hazards of your chemical products, you must always refer to your chemical safety data sheet and choose DG storage that is suitable for that class (and sub-class, if applicable).
Compliant storage refers to the detailed design and construction requirements that are outlined in the relevant Australian Standard. If your DG storage doesn’t meet these requirements, then it won’t be recognised as compliant – and may cost your organisation in both safety and non-compliance penalties.
DON’T: Allow Poor Housekeeping Practices
While you may have chosen the best chemical storage equipment for your workplace, it won’t protect your people, property and environment if it’s not used correctly. In fact, you’re simply negating the many benefits of your storage solution if it’s not properly used, cleaned and maintained by your staff.
Key points to consider when looking at the upkeep of your cabinets and outdoor containers include:
- Are the chemical packages sitting neatly on the shelves and not inhibiting the door closing mechanisms?
- If you’re storing drums, are they stacked safety and according to the requirements of the Australian Standard?
- Do you have other materials — such as cleaning rags or paperwork — sitting on or in your store?
- Have you removed all packaging from the chemical containers before they’re placed into storage?
- In the event of a leak or spill, have all surfaces (not just the spill sump) been cleaned out and decontaminated?
- Is there any residue left on the chemical packages?
- Does the shelving require cleaning; do you need to adjust the height of the shelves to comfortably fit the packages?
- Is the cabinet located in a position that is free from rubbish, work materials, tools and other items which may cause or add to a fire hazard?
- Do you have a regular roster of cabinet inspections and housekeeping tasks to ensure that the cabinet and its contents remain in order?
How your storage is being used and maintained is integral for chemical safety in the workplace.
What To Do For Better Chemical Safety
While we’ve highlighted four do’s and don’ts that you can apply to almost any workplace that carries hazardous chemicals or dangerous goods, there are many more factors to consider when you’re looking at chemical safety for your site. To help you with your research, you can download our free guide. Controlling Risks Associated with Hazardous Chemicals offers practical advice that you can immediately apply to your own workplace. Access your copy for free today and improve chemical safety in your operations.
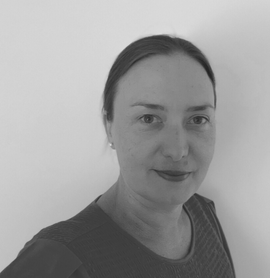
Living life by the 4 C’s of marketing – communication, coffee, compliance… and more coffee – Leisa Andersen is Storemasta’s Content Marketing Manager. When she’s not writing, you’ll find her enjoying all the good things in life, including shopping, travel and gluten free donuts.