Are you searching for information about engineering controls for hazardous chemicals? As a key control within the Hierarchy of Controls, engineering controls are essential for maintaining chemical safety. This blog discusses engineering controls and how they fit into the overall hazard control hierarchy. We’ll also discuss some examples of engineering controls and explain how a measure can fail — and what you can do to ensure its effectiveness.
What are Engineering Controls?
Controls are those measures which can improve safety and minimise the risks associated with hazards, such as harmful chemicals. An engineering control is an essential type of control that assists in isolating or protecting staff from hazardous substances.
Determining the most effective engineering controls for your workplace can minimise the likelihood and impact of chemical exposure for staff.
Engineering controls may be a piece of equipment, a machine or a mechanical device.
These controls can reduce harm through a variety of ways, including:
- Isolating workers from chemicals (eg, using a self-contained lube station)
- Enclosing high risk operations in sealed areas (eg, sealing off an area that is only opened during maintenance and cleaning)
- Extracting contaminants from the breathing zone of workers (eg, installing a local exhaust ventilation (LEV) system)
- Automating tasks so workers no longer need to perform them (eg, using robots to spray paint new cars)
- Segregating incompatible chemicals from one another (eg, installing compliant safety cabinets and chemical stores).
Need more info on incompatible substances?
Access your free segregation guide
Engineering controls can change the physical layout of a work area or even the entire workplace Some examples of this include using a local exhaust ventilation system when cutting timber or relocating chemical stores to isolate dangerous goods from incompatible substances and high traffic areas.
However, it’s essential to consult the workers and contractors who work in those areas as some engineering controls (machinery, equipment, contained environments) will require changes to operating procedures and housekeeping practices. If you’re staff aren’t part of the process, they might resist embracing the new technologies and place themselves at further risk.
IMPORTANT: Even if an engineering control completely isolates (or removes) workers from a task, you will probably still need to implement administrative controls (training, supervision, operating procedures) and personal protective equipment (breathing apparatus, protective clothing, gloves etc).
Engineering Controls Examples
Like all hazard control measures, engineering controls should be selected after careful analysis of the workplace, the job tasks being undertaken, as well as the physical and health hazards presented by the chemicals.
Some engineering controls examples include:
Hazardous Chemical Storage Equipment
When chemicals are stored correctly and in full conformance with Australian Standards, there is reduced risk of vapours and substances potentially harming the staff that are working with or near them. Indoor safety cabinets and outdoor chemical storage containers are recognised as effective engineering controls.
Compliant chemical storage is one of the most significant engineering controls that workplaces must consider.
Bunded Handling Equipment
Handling equipment reduces the risk of chemical leaks and spillage during transfer operations. This in turn minimises incidents such as chemical burns, poisoning and asphyxiation. Bunded handling equipment isolates workers from the substance by providing containment for leaks and spills.
Bunding
Chemical bunding is a barrier that prohibits hazardous liquids from travelling further throughout the work area. There are a multitude of bunding solutions on offer including floor bunding, bunded shelving and portable bunding. Whether bunding is integrated into shelving systems or it’s a portable solution for remote worksites, it contains hazardous chemicals and prevents harm to staff, property and the environment.
Decantng Equipment
Decanting is another job task that can create a hazardous situation for the employee responsible. Ill fitting, worn or chemically incompatible decanting equipment can increase risk for your organisation. Decanting assistors and spill funnel lids are just two examples of decanting equipment which can reduce hazardous spillage.
Lubrication Stations
Dispensing hazardous chemicals is just part of the job for many workers, however, this can result in accidental releases. Fires, explosions, contamination and human harm can occur if all-in-one dispensing solutions aren’t implemented in workplace operations.
Other engineering control examples may include:
- Ventilation systems
- Wet methods for tasks including grinding and drilling
- Laboratory ventilation hoods
- Automated work tasks via industrial robots
- Spray painting booths
- Designed sealed work areas
How Do Engineering Controls Fit into the Hierarchy Of Controls?
The Hierarchy of Controls is a recommended method for selecting hazard control measures by grouping different types, then ranking them in order of effectiveness.
There are 5 different groups ranked in the following order:
- Elimination Controls - any control measure that results in the chemical hazard being completely eliminated.
- Substitution Controls - control measures that look for safer ways of carrying out the same task, or using less harmful chemicals.
- Engineering Controls - an engineering control is a control measure that is physical in nature. Engineering controls focus on machinery, tools, equipment, and workplace design to reduce chemical exposure.
- Administrative Controls - control measures that are carried out by management, workers and contractors through safe work methods, operating procedures, housekeeping, and hygiene practices.
- Personal Protective Equipment (PPE) Controls - any control measure that requires a worker to wear or use PPE.
To use the Hierarchy of Control, for each chemical hazard work your way through the 5 different types of control measures and look for different ways to minimise the effect of the hazard. Always try to eliminate the hazard completely if you can (that’s why Elimination Controls are ranked #1) and then implement other measures giving priority to control measures with the highest rankings.
The Hierarchy of Control recognises that for many chemical hazards, more than control measure is required. This is especially true for engineering controls which rely heavily on correct operating procedures, preventative maintenance, and cleaning. You should always be looking at the way control measures support (or negate) each other.
What Causes an Engineering Control To Fail?
While engineering controls can fail for a number of reasons, the cause can generally be traced back to a human factor — either direct or indirect.
Let’s look at the 3 key ways in which engineering controls can fail in the workplace:
1. Inappropriate Risk Assessment
Many engineering control measures fail because a thorough risk assessment was not conducted in the initial stages. Workplaces purchasing expensive equipment and machinery based on industry ‘best-practices’ alone, and without considering the unique setup and operations of their own workplace run the risk of equipment that just doesn’t work or introduces new hazards.
Here’s a few examples of situations that could have been avoided with a risk assessment:
- A local exhaust ventilation system is choking. This is because the local exhaust ventilation system doesn’t have the capacity for the amount of wood dust produced daily.
- A flammable liquids store was relocated to an outdoor area. However, the new location sits within the turning circle of forklifts and supplier delivery trucks, and now is at risk of impact damage.
2. Technical Problems
An engineering control can fail if the equipment or device has not been installed correctly. It may also fail if it has mechanical faults.
Again, you need to ensure that your risk assessment completely evaluates the installation phase as well as any ongoing maintenance program.
REMEMBER: It’s part of your WHS duties to ensure that engineering controls are properly inspected and maintained to ensure safety and compliance.
3. Human Factors
Human factors are the main reason engineering controls fail. Operators may use equipment incorrectly or not at all. Other times, the problem begins when management have not consulted the workers and contractors who use (or are affected by) the engineered devices and machinery.
Involving your staff in the risk assessment process can improve their understanding of the importance of engineering controls.
Workers (understandably) become upset when their workplace changes and they don’t understand why. However, when workers are involved in the risk assessment process, they have a greater understanding about how a piece of machinery or a change to the layout of their work bench is improving their personal safety.
Consulting your staff will help you understand the most practical methods and help you to avoid engineering controls that are misused or avoided by your staff.
Here’s a few examples:
- Machinery shields that restrict movement and vision (staff don’t feel comfortable using them)
- LEV systems that require frequent repositioning (staff don’t want to waste time setting them up)
- Dust collectors that choke and shutdown machinery (workers aren’t clearing them regularly)
- Chemical stores that were originally installed correctly but now contain substances from different hazard classes, and chemicals in open containers (management aren’t enforcing strict housekeeping and hygiene procedures)
Engineering controls can also fail when workers and contractors have not received proper training and don’t know how to use, clean, and maintain the machinery and plant that has been implemented for their safety. Training must also be supported with proper supervision and remedial actions if workers are observed to be not following safety protocols.
Engineering Controls and Your Workplace
To create a safer working environment, it’s important that you implement and maintain the correct engineering controls for your business. However, this is not possible without first completing a thorough risk assessment.
If you’re ready to conduct a full risk assessment on the chemical hazards at your workplace, why not access our free eBook? How To Manage The Risk Of Hazardous Chemicals In The Workplace features easy-to-follow instructions, as well as practical templates and tools that you can use in your own organisation. Get your copy today to learn more about risk assessments and controlling chemical hazards.
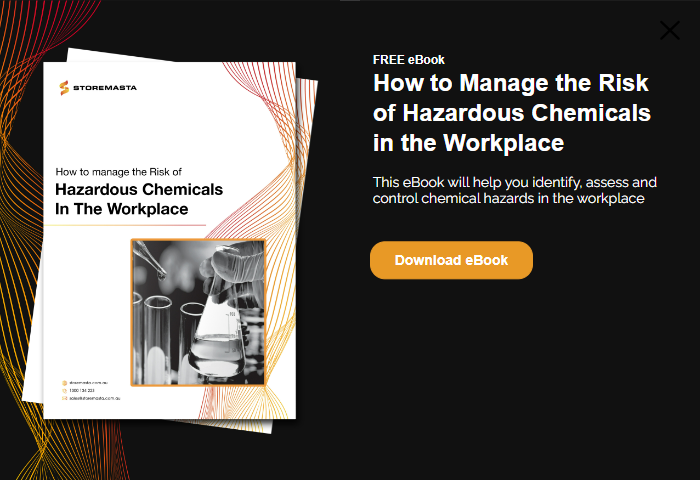
Joining the team as a Dangerous Goods Storage Consultant, Melissa Hampton became Storemasta's Marketing Manager in late 2021. With extensive knowledge and experience in chemical compliance, Melissa is responsible for leading the Marketing team and helping shape their marketing strategy. In her spare time, you can find Melissa hiking, swimming and enjoying the great outdoors in beautiful north-west Tasmania.