Contents
- What are Administrative Controls for Flammable Liquids Storage?
- Hierarchy of Control: Administrative Controls
- Controlling Flammable Liquid Hazards
- Examples of Administrative Controls for Flammable Storage
- Creating an Administrative Control for Flammable Cabinets
- Standard Operating Procedures
- Policies
- Housekeeping
- Maintenance
- Training
- Supervision
- Administrative Controls and Flammable Liquids Safety
What are Administrative Controls for Flammable Liquids Storage?
Hierarchy of Control: Administrative Controls
Controlling Flammable Liquid Hazards
Examples of Administrative Controls for Flammable Storage
Creating an Administrative Control for Flammable Cabinets
Standard Operating Procedures
Policies
Housekeeping
Maintenance
Training
Supervision
Administrative Controls and Flammable Liquids Safety
If you’ve been reading our posts for a while, you’ll understand how important the Hierarchy of Controls is when implementing a risk management process in your business. Administrative controls are the 4th step in the Hierarchy of Control. These controls include documents, training, policies and procedures which help bolster the safety and effectiveness of the other controls.
When storing flammable liquids at your site, choosing the correct storage method is only the first step in ensuring compliance. By developing a range of administrative controls to apply to your flammable liquids storage, you can ensure that your staff and community remain safe through the diligent creation and adherence to these administrative documents. Keep reading to find out what administrative controls can help you in your own organisation – specifically for use with flammable cabinets.
What are Administrative Controls for Flammable Liquids Storage?
Administrative controls are the safe work methods and operating procedures that support other hazard control measures.
These important controls will guide the way work is done, therefore increasing awareness and safety of your team. Without chemical controls, you are exposing your staff to health and safety risks including chemical burns, inhalation of harmful fumes and incidents including spills and fire.
Chemical controls are important as they reduce the likelihood and severity of incidents and accidents with flammable liquids.
Hierarchy of Control: Administrative Controls
The Hierarchy of Control is a system that has been developed to control risks in the workplace. As a step-by-step approach to eliminating a risk or reducing it, the Hierarchy of Control is usually depicted as an upside down triangle with 5 steps.
When controlling risks, the Hierarchy control structure should be implemented with elimination as the first and most effective step, followed by the substitution of chemical risks (whether they are work practices or the chemical itself).
Administrative Controls are the next step, offering the required documentation to ensure the elimination, substitution and engineering controls are carried out to optimum effectiveness.
The last step, albeit essential control, is PPE which should be used in conjunction with the higher controls, not instead of them.
The Hierarchy of Control lists the steps of control from the most effective to least effective, with all controls being essential to consider.
Controlling Flammable Liquid Hazards
As we know, there are a wide range of hazards associated with Class 3 Flammable Liquids. These include, but are not limited to:
- Exposure to flammable liquids through inhalation, contact with the skin or eyes, or accidental ingestion
- Fire and explosion risk, when flammable liquid vapours are concentrated and ignite
- Environmental pollution and harm, if liquids leak or spill into the environment
Flammable liquids storage, including storage in Flammable Cabinets, allows these liquids to be contained in a secure and safe environment where the likelihood and impact of an incident is controlled. For example, if a flammable drum leaks when in storage, the Flammable Cabinet will contain the spillage in a liquid-tight sump, so it may be cleaned out by the spill response team to minimise chemical exposure and the release of flammable vapours.
Examples of Administrative Controls for Flammable Storage
While your storage is an important engineering control, it can’t do its job if it’s not being:
- Installed properly
- Used safely
- Inspected regularly
- Cleaned out and organised
- Maintained to ensure compliance
- Audited to check ongoing suitabilitly
Some administrative controls may include:
- Inductions
- Training
- Follow-up training
- Contractor registration
- Site rules
- Housekeeping guidelines
- Maintenance schedules
- Personal hygiene procedures
- Staff supervision
- Emergency preparedness
However, due to the many risks and requirements associated with Class 3 Flammable Liquids, you’ll also need to consider a wide range of documents including cabinet loading procedures, segregation of incompatible substances, installation procedures and a firm training (and re-training) process so all staff are aware of:
- Flammable liquids safety requirements
- The hazards related to using and storing these substances
- How to use the flammable cabinet or flammable outdoor store
- Who and when to call when there is a spill or potentially dangerous incident
IMPORTANT: Compliant flammable liquids storage is an engineering control that requires inspection, maintenance and audits so they can continue to perform as they should.
Creating an Administrative Control for Flammable Cabinets
The Australian WHS Regulations state the need for inspection and maintenance procedures for all controls.
However, the Australian Standard 1940 lays out very specific information on how to approach both the handling and storage of flammable liquids, specifically in safety cabinets. These requirements can greatly assist with the creation of your admin documents.
When developing your administrative controls – and any controls for chemicals onsite – make sure you first identify and assess the risks, collating the safety data sheets for each flammable liquid that you’re storing. This will help you develop a tailored administrative control process that will target the risks specific to your flammable liquid storage areas.
Access your free Safety Cabinet Checklist
Important Admin Controls for Flammable cabinets include:
Standard Operating Procedures
- Loading the cabinet: never load a flammable cabinet past its approved capacity. Stack containers so they don’t block the self-closing doors, with no more than 2 drums (60L each) in stacks. The self-closing doors of a Storemasta flammable cabinet must never be propped open and they must always close in sequence, automatically.
- Segregation of flammable liquids: create clear policies for segregating incompatible substances (eg, flammables are incompatible with most dangerous goods including oxidisers and organic peroxides).
- Ignition sources: procedures dictating that ignition sources are identified and isolated from any flammable cabinets, with written procedures on the types of gadgets and electronics that are allowed in the area.
- Signage: ensure the correct Class 3 diamond is on the cabinet, as well as the NO SMOKING, NO IGNITION SOURCE 3M sign. Signage must be legible and visible, with aged or damaged signage replaced.
Policies
- Purchasing: keep flammable liquid quantities to the minimum. Schedule chemical deliveries so there is always someone to put the order in storage.
- Aggregate quantities: make sure that you’re not exceeding aggregate quantity requirements for your premises. See 1940 for full details.
- Site rules: no smoking or bringing ignition sources onsite, no eating or drinking in work areas, PPE to be worn while handling chemicals.
- Emergency procedures: create procedures for what to do in the event of a fire, explosion, chemical spill, or dangerous chemical reaction — including personal safety, contacting emergency services, evacuation and muster points.
- Personal hygiene: policies should include prohibiting food or drink near flammable liquid storage areas, and ensuring hand-washing facilities for workers who handle chemicals.
Housekeeping
- Inside the flammable cabinet: make sure only flammable liquids are stored inside the cabinets, keeping lids and seals on containers, wiping down chemical residue from containers before putting away.
- Exterior of the cabinet: put chemical containers away immediately after use. Don’t ever use the top of the cabinet as a shelf, or the spill bund as storage. Don’t have combustible materials near the cabinet location.
For the indoor storage of flammable liquids, cabinets are an ideal solution - but they must be installed, used and maintained to ensure safety and compliance.
Maintenance
- Regular inspections: inspect the structural integrity of cabinets and ensuring they remain free of dents, chipping and corrosion. Check that self-closing doors close in sequence without jamming.
- Repairs and maintenance: replace missing signage or damaged parts, repairing faulty exterior lighting. Storemasta provides a full range of spare parts to ensure easy maintenance of your Class 3 Flammable Cabinets.
- Cleaning schedule: clean up up spilled chemicals, wiping chemical contaminants from cabinet walls and surfaces. Dispose of out-of-date or contaminated substances.
- Register of Hazardous Chemicals: a master list of chemicals inside the cabinet must be available, as well as the current Safety Data Sheet (SDS) for each substance. We recommend attaching a document holder to your flammable cabinet with the updated documents within.
Training
- Induction training for all site visitors, worker and contractors: train personnel on flammable liquid hazard awareness, location of flammable liquids stores, site rules, restricted areas, prohibited items and substances etc.
- Manual handling procedures: considerations when moving containers of flammable liquids including the use of handling equipment such as trolleys and drum dollies.
- On-the-job training for workers in the chemical stores: comprehensive training that shows staff how to identify hazards, use the equipment and ensure flammable liquids safety at all times.
- Personal Protective Equipment: staff need to be aware of the correct personal protective equipment for flammable liquids, including how to put it on, take it off and ensure it’s been cleaned and maintained after use.
Supervision
- General supervision: all staff and contractors must be competent in their duties and providing remedial training and instruction if they don’t meet accepted standards.
- Job rotation: rotate workers who handle flammable liquids to reduce long-term chemical exposure.
- Restricted access: control the number of people accessing HAZCHEM work areas, but make sure staff are never working alone.
- Contractors: escort any maintenance personnel and other contractors around your site to ensure there are no issues with health and safety.
Administrative Controls and Flammable Liquids Safety
As we’ve highlighted here in this post, flammable liquids safety is only improved and made simpler with the development of administrative controls such as restricted access, on-the-job staff training, standard operating procedures for flammable cabinets and a set cleaning schedule.
If you’d like to learn more about Class 3 Flammable Liquids, why not grab a copy of our popular eBook. Essential Considerations When Storing Flammable Liquids Indoors will guide you through the risk assessment process, offering suitable engineering controls to help you minimise risk in your operations. Get your free copy today and create a healthier, safer work environment.
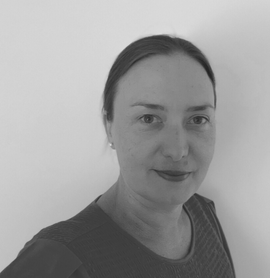
Living life by the 4 C’s of marketing – communication, coffee, compliance… and more coffee – Leisa Andersen is Storemasta’s Content Marketing Manager. When she’s not writing, you’ll find her enjoying all the good things in life, including shopping, travel and gluten free donuts.