Administrative controls play a crucial role in chemical safety by helping to manage and reduce the risks associated with the handling, storage, and use of hazardous chemicals in the workplace. As part of the Hierarchy of Control, administrative controls are an essential safety measure to help organisations reduce risk. While these admin controls can be suitable for all types of hazards, this post will be focused on how developing the right kind of administrative controls can bolster chemical safety in your business.
What are Administrative Controls?
Administrative controls are an essential part of the Hierarchy of Control.
The Hierarchy offers a systematic way to control workplace hazards by providing 5 different tiers of controls, starting with the most effective and ending with the least effective.
Illustrated in an upside pyramid model, the Hierarchy involves the following steps:
- Elimination
- Substitution
- Engineering Controls
- Administrative Controls
- Personal Protective Equipment
Administrative controls are the fourth tier of the Hierarchy of Controls pyramid, falling after the implementation of engineering controls. Often, the engineering controls effectiveness are bolstered by the administrative procedures developed to assist staff with ensuring chemical safety.
Some general examples of administrative controls include policies, procedures, training and management practices that can help workplaces in controlling chemical hazards.
IMPORTANT: Control measures are used to control hazards, to create a compliant and safe environment for people, as well as place and environment. Controlling hazards are essential for maintaining compliance and safety, as per the WHS laws in your region.
Why are Control Methods Needed?
In every workplace (and in fact, any type of environment) there are hazards that can pose risk.
Due to these risks, there is the necessity to identify and assess the situation, while them selecting the most suitable and effective control measure to mitigate risk.
Risk in the workplace must be controlled.
Furthermore, the maintenance and ongoing inspection and assessment of the control measures ensures that safety is still provided as the workplace changes. Remember, risk management is not a one-off project; it’s a continual circular cycle that responds to the everchanging factors in a workplace, such as new staff, different work tasks, increased quantities of certain chemicals, environmental conditions and more.
INTERESTED IN RISK MANAGEMENT? For a comprehensive guide to risk management, including details about applying the Hierarchy of Control to your operations, you can download our free eBook which will lead you step by step through the process.
Can More Than One Control Method Be Used or Followed?
When thinking about dangerous goods management and chemical safety as an ongoing process that involves multiple levels of controls, it’s essential to realise the significance of each tier on the Hierarchy of Control.
Without one tier, the other control measures won’t be effective.
Why are Administrative Controls Important for Chemical Safety?
There are a multitude of reasons why administrative controls are important for chemical safety, including:
- Risk Management: Administrative controls help in the identification, assessment, and management of risks associated with chemical hazards. By implementing proper administrative measures, organisations can develop strategies to reduce the likelihood of accidents and the severity of potential consequences.
- Compliance: Administrative controls can help companies and organisations comply with WHS laws through the establishment of suitable chemical safety procedures and protocols. The regulatory body in your region can also assist with resources that can help you formulate your chemical controls, including administrative controls.
- Training and Education: Effective staff training and education programs are essential components of administrative controls. They ensure that employees are knowledgeable about the hazards of the chemicals they work with. Well-informed workers are less likely to make mistakes that could lead to accidents — and are better equipped to deal with situations that may arise, such as accidental releases of hazardous substances.
- Emergency Preparedness: Administrative controls contribute to the development of emergency response plans. These plans include procedures for dealing with chemical spills, fires and other emergencies. Effective planning and communication are critical to minimising the impact of an incident and protecting both personnel and the environment.
- Communication and Documentation: Clear communication and documentation of procedures, policies and safety protocols are vital for chemical safety. Administrative controls help establish documentation systems that record chemical inventories, risk assessments, safety data sheets (SDS) and other important information. This documentation ensures that relevant information is readily available to those who need it.
- Continuous Improvement: Administrative controls allow workplaces to implement feedback mechanisms, inspections and audits to rectify any chemical hazards or poor work practices. This continuous improvement process helps identify areas for enhancement, ensuring that safety measures remain effective and up to date.
By incorporating administrative controls into a comprehensive dangerous goods management strategy, you can promote a culture of safety, reduce the likelihood of accidents, and protect the well-being of workers, the community and surrounding environment where hazardous chemicals are present.
What Kind of Administrative Controls Can Boost Dangerous Goods Safety?
When working with any kind of dangerous goods, it’s important to understand how administrative controls can help your team control risks.
Some types of administrative controls that may assist this process include:
Workplace Policies and Procedures: Establishing and enforcing policies and procedures related to the handling, storage, and use of chemicals. This may include guidelines on proper storage practices, handling procedures, and emergency response protocols.
Standard Operating Procedures: Providing clear and written instructions for tasks involving hazardous chemicals. This may include detailed standard operating procedures (SOPs) that outline step-by-step instructions for work tasks as well as how to use and maintain chemical storage and handling equipment. SOPs in conjunction with regular training can help raise the awareness of staff so that human error is reduced.
Training and Education: Providing employees with comprehensive training on the hazards of chemicals in the workplace, safe handling practices, and emergency response procedures. Training helps ensure that workers are knowledgeable about the risks associated with their tasks and are equipped to perform their jobs safely.
- Workplace Signage and Labelling: As well as being a compliance obligation, it’s important that all workplace dangerous goods signage and chemical labelling meets the requirements. This includes the inspection and maintenance of signage and labels to make sure all workers are aware of the hazards in that area.
- Security or Access Control: Limiting access to areas where hazardous chemicals are present to authorised personnel only. This control helps prevent unauthorized individuals from entering potentially dangerous areas, reducing the likelihood of accidents.
- Emergency Preparedness and Response Planning: Developing and regularly practicing emergency response plans for incidents involving hazardous chemicals. This includes procedures for spills, leaks, fires, and other emergencies, as well as providing training on how to respond appropriately.
- Health Monitoring: Ensuring health and safety for staff working with dangerous goods is of the utmost importance. Therefore, implementing programs to monitor the health of workers who may be exposed to hazardous chemicals is essential. This may involve regular health check-ups and monitoring for early signs of adverse health effects. It may also include the assessment of health records to note any unusual illnesses or unexplained absences that may signify a hazard that requires control.
- Job Rotation and Scheduling: Exposure to harmful substances can be controlled if staff are not put in that environment for excessive periods of time. This can be achieved by implementing job rotation or scheduling practices to prevent overexposure to chemicals which may affect health and safety.
- Management Systems: Establishing safety management systems that include regular audits, inspections, and reviews to ensure that administrative controls are effective and up-to-date. This continuous improvement process helps identify areas for enhancement.
- Chemical Documentation: Record keeping may include the maintenance of chemical inventory documents, up to date safety data sheets (SDS), training sessions, and other relevant information. Documentation helps in tracking compliance, facilitates audits, and ensures that information is readily available when needed.
- Storage and Segregation Procedures: As most classes of dangerous goods are incompatible with multiple other classes, ensuring that the chemical classes are properly segregated is a crucial part of workplace health and safety. We recommend developing procedures, based on your own risk assessment, to guide staff training and implement safe procedures for the storage and segregation of dangerous goods.
Segregating dangerous goods that are incompatible is made easier when administrative controls, such as standard operating procedures for DG storage. are in place.
Controlling Hazardous Chemicals
Administrative controls are a critical component of an effective chemical safety program. They complement other control measures and contribute to a comprehensive risk management approach aimed at reducing the risks associated with dangerous goods and hazardous chemicals in the workplace.
If you’d like to learn more about the steps involved with the control of dangerous goods and hazardous substances in the workplace, why not access a copy of Storemasta's eBook. This resource will give you the tools to identify, assess and control potential chemical hazards in your own business.
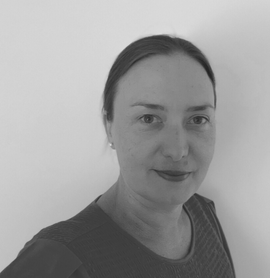
Living life by the 4 C’s of marketing – communication, coffee, compliance… and more coffee – Leisa Andersen is Storemasta’s Content Marketing Manager. When she’s not writing, you’ll find her enjoying all the good things in life, including shopping, travel and gluten free donuts.