Understanding the Hierarchy of Control
How Does the Hierarchy of Control Work?
Using a Combination of Control Measures
Hierarchy of Control to Improve DG Safety Practices
Controlling Risks
Using the Hierarchy to Minimise Your Risk
If you’re new to chemical safety and risk management, you may have heard about the Hierarchy of Control. As an important tool for any workplace managing risks, the Hierarchy of Control gives clear steps for the implementation of controls.
In this post, we’ll look at the Hierarchy of Control and explain how it can be implemented to reduce chemical risk.
Understanding the Hierarchy of Control
The hierarchy of control is a systematic approach to managing occupational hazards and risks in the workplace. It provides a framework for selecting and implementing control measures to reduce or eliminate hazards.
The hierarchy is typically presented as a pyramid, with control measures ranked from most effective to least effective.
Employers and their teams are encouraged to follow the hierarchy of control principles to systematically identify and implement measures that prioritise hazard elimination or reduction. The goal is to prioritise measures that directly address the source of the hazard and provide the greatest level of protection for workers.
How Does the Hierarchy of Control Work?
By following the hierarchy, businesses and organisations carrying dangerous goods can create safer work environments.
The hierarchy of control includes 5 essential levels, listed from most effective to least effective:
Elimination
Completely removing the hazard or process that poses a risk to workers.
Substitution
Replacing a hazardous substance or process with a less hazardous one.
Engineering Controls
Implementing physical changes to the workplace or equipment to isolate workers from the hazard.
Administrative Controls
Introducing work practices, policies, and procedures to minimize exposure to hazards.
Personal Protective Equipment (PPE)
Providing protective clothing, equipment or devices to reduce the exposure of individual workers to hazards.
Using a Combination of Control Measures
While the hierarchy of control is presented as a pyramid, it's important to note that effective risk management often involves a combination of control measures from multiple levels.
The goal of the hierarchy is to create a comprehensive and layered approach to risk management that maximises efficacy.
For example, PPE may be necessary in addition to other control measures, but it is generally considered the least effective and relied upon only when higher-level controls are not feasible or during the transition to more effective measures.
Hierarchy of Control to Improve DG Safety Practices
If you look at the 5 tiers of the Hierarchy of Control pyramid, you can apply them to some simple everyday situations that you may find in your own workplace.
While risk management should be applied to every identifiable hazard, this is just a quick example to help you understand how the hierarchy would apply in a situation involving dangerous goods or hazardous chemicals.
Example of using the Hierarchy of Controls:
- Elimination
Example: Hazard identification of harmful chemicals will require the consideration of eliminating hazards. This means that you may be able to eliminate the risk. An example of this is redesigning a process to eliminate the need for a hazardous substance. As the most effective control measure, elimination must be considered before all other control methods are examined.
- Substitution
Example: When substituting chemicals, consider the effectiveness of using another product instead of a more harmful one. This may not always be practical for every work task, but it is essential that you endeavour to substitute the chemical as it's a simple way to take away the initial risk. An example may be using a water-based paint instead of a solvent-based paint to reduce exposure to harmful volatile organic compounds (VOCs).
- Engineering Controls
Example: As the third tier on the hierarchy pyramid, engineering controls play an essential roll in risk control. You may choose the installation of ventilation systems, enclosures, or barriers to contain or remove hazardous substances and prevent exposure. Engineering controls will also include your dangerous goods storage, and any chemical handling products that can minimise the harmful effects of the chemicals, as well as manual injuries from handling.
- Administrative Controls
Example: Implementing administrative controls may include establishing proper training programs, job rotation, and scheduling breaks to reduce the duration and intensity of exposure to chemicals. Administrative controls are the procedures and protocols that can help bolster your other controls in the hierarchy.
- Personal Protective Equipment (PPE)
Example: Your personal protective equipment is an essential control measure, but should be relevant to the chemicals being used, as well as kept in good condition, and suitable for the staff member and their tasks. An example of PPE includes using gloves, masks, goggles, or respirators for your hazardous chemical to protect staff against chemical exposure while handling the substance.
Engineering controls, including DG storage, offer a crucial control when reducing chemical risk.
Controlling Risks
Controlling chemical risks in the workplace is crucial. Some key reasons why controlling chemical risks is essential includes:
Protecting Worker Health and Safety
Exposure to hazardous chemicals can lead to a range of adverse health effects, including acute toxicity, chronic illnesses, respiratory problems, skin disorders, and more.
Controlling chemical risks through proper handling, storage, and use helps minimise the likelihood of accidents, spills, or accidental chemical releases that could harm workers.
Legal Compliance
Many countries have regulations and standards in place to protect workers from chemical hazards. Compliance with these regulations is often mandatory and failure to adhere to them can result in legal consequences and/or fines.
Examples of such regulations include the WHS laws in your state or territory, although these laws may not always provide the detailed guidance required for risk control. However, there is more information available from the Safe Work authority in your area on the regulations and laws affecting your enterprise, as well as ways that you can create a safer working environment for your people.
The Australian Standards also provide requirements that relate to dangerous goods storage and handling, which can be followed in detail to ensure the optimum safety procedures are being met.
There are also legal requirements for the labelling of hazardous chemicals through the Globally Harmonised System (GHS) that pertain to any classification and labelling of chemicals, to ensure safety when chemicals are being transported or used.
Maintaining Productivity
Accidents involving chemicals can disrupt workflow, cause downtime, and result in financial losses for businesses.
Implementing effective chemical risk control measures contributes to a safe and productive work environment, reducing the likelihood of disruptions due to accidents or injuries.
Productivity and safety can be maintained when the correct risk controls are implemented.
Protecting Profits
Investing in effective chemical risk management can lead to long-term cost savings. Preventing accidents and occupational illnesses reduces healthcare costs, workers' compensation claims, and potential legal expenses.
Implementing proper controls from the outset can be more cost-effective than addressing issues after they arise.
Corporate Responsibility
Demonstration of a commitment to the health and safety of employees and the environment is a fundamental aspect of corporate responsibility. Companies that prioritize these values enhance their reputation and stakeholder trust.
Employee Morale and Retention
Providing a safe and healthy work environment positively influences employee morale and contributes to higher job satisfaction.
Employees are more likely to stay with an organization that prioritizes their well-being and actively manages risks associated with hazardous substances.
Community Wellbeing
Chemical incidents can have far-reaching effects beyond the workplace, impacting nearby communities. Controlling chemical risks helps protect the well-being of the broader community by preventing accidental releases and exposures.
Environmental Protection
Uncontrolled release or improper disposal of hazardous chemicals can lead to environmental pollution, affecting air, water, and soil quality.
Regulatory agencies often enforce strict guidelines for the management and disposal of chemicals to prevent environmental contamination and protect ecosystems.
Using the Hierarchy to Minimise Your Risk
Controlling the risk of dangerous goods is essential for protecting the health and safety of workers, as well as fulfilling corporate responsibilities, maintaining or improving productivity, reducing environmental impacts, and compliance with your work health and safety laws in your state or territory.
A comprehensive risk management approach is necessary to address chemical hazards effectively, with the Hierarchy of Control recognised as the systemised and universal method of effectively controlling workplace hazards. Without such systems, it’s difficult to create a safe, compliant workplace due to the complexities of hazards.
However, it doesn’t have to feel like an overwhelming task. If you’d like to find out more about risk control for your chemicals, download our free eBook. In this guide, we offer expert tips and practical guidance to help you get your workplace in great shape. Get your copy now to continue your learning journey.
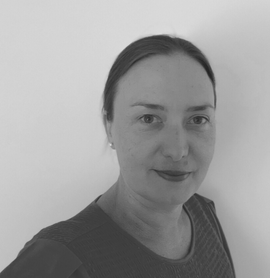
Living life by the 4 C’s of marketing – communication, coffee, compliance… and more coffee – Leisa Andersen is Storemasta’s Content Marketing Manager. When she’s not writing, you’ll find her enjoying all the good things in life, including shopping, travel and gluten free donuts.