You’ve carried out a full risk assessment and implemented HAZCHEM risk controls to reduce health and safety risks. But your responsibilities don’t end there. According to the WHS Regulations, you must ensure that any ‘risk control measure is maintained so it remains effective’. This post looks at Section 37 of the WHS Regulations and unpacks what 'maintenance of control measures' means for your business through ensuring controls are:
- Fit for the Purpose
- Suitable for the Nature and Duration of the Work
- Installed, Setup and Used Correctly
WHS Compliance and HAZCHEM Control Measures
Chemical risk controls can be any type of control that reduces the risks associated with your dangerous goods and hazardous chemicals.
This could be safety cabinets, outdoor chemical stores, bunding, gas cages, gas cylinder trolleys, bunded drum dollies or any other solution that can help you manage the hazards of your onsite chemicals.
Your control measures, such as this outdoor IBC chemical store, must be maintained for compliance and safety.
The selection, installation and use of your chemical risk controls is only the beginning of your compliance journey. Remember to pay attention to the inspection and maintenance of your controls to ensure they effectively reduce risk for your operations.
We’ll now look at the 3 key points involved with maintaining HAZCHEM risk controls to meet your WHS compliance obligations.
1. Ensure the HAZCHEM Controls are Fit for the Purpose
Your first responsibility is to ensure that the chemical control measures you have implemented are (and remain) fit for the purpose.
In terms of chemical hazards, a fit for purpose control measure is one that is compatible with the hazard class of the chemical. This control should align with the recommendations in the chemical’s safety data sheet, as well as the requirements of the relevant Australian Standard/s.
WHS Standards Examples
To illustrate how chemical controls can be fit for purpose, we’ve included some general examples below.
Examples of fit for purpose controls that can assist with compliance with WHS laws include:
- Engineering controls required by Australian Standards. Eg, flammable liquids cabinet made from double-walled sheet steel.
- PPE controls recommended by a safety data sheet (SDS). Eg, impervious gloves made from polyvinyl alcohol or teflon when handling a flammable, corrosive solvent.
- Isolation controls recommended by an SDS. Eg, keeping a highly flammable liquid in a tightly closed container and under 30°C.
At the time of implementation, these chemical controls may be fit for the purpose, but if things change (and they always do) the controls you have in place may no longer be suitable. Such changes may include the updating of a safety data sheet or Australian Standard. It may also include a change in the quantity of chemicals that you have onsite or even the way the chemical is used during your work processes. Therefore, remember that controls must remain fit for purpose by continually inspecting and reviewing your HAZCHEM risk controls to ensure safety compliance.
- EXAMPLE 1: You’ve been storing paints and jerrycans of petrol in an old flammable liquids cabinet that was purchased 15 years ago. Even though the cabinet was purpose-built and has the correct signage it does not have doors that automatically close. It is a requirement of the Australian Standard AS1940 - The storage and handling of flammable and combustible liquids that ‘cabinet doors shall be self-closing, close-fitting and held shut automatically by catches at two or more points.’ This cabinet is no longer ‘fit for the purpose’ and would not comply with work health regulations.
Storage requirements for dangerous goods, such as flammable liquids or paints, may change over time. It's important to keep up with any legislative changes or Australian Standard updates to ensure continued compliance.
- EXAMPLE 2: You’ve been storing 200 litres of paint in a dedicated flammable liquids cabinet, purpose built with self-closing doors. It is 2.2 metres tall. You increase your stocks to 260 litres. According to the Australian Standard, a cabinet holding more than 250 litres of flammable liquids cannot be more than 2 metres high. This cabinet is no longer ‘fit for the purpose’.
REMEMBER: One of the most common issues we find at the worksites of our clients, is chemical stores and safety cabinets that were purchased many years ago (and still in use) but no longer meet the requirements of the current Australian Standards.
2. Suitable for the Nature and Duration of the Work
Your next responsibility is to ensure that the controls remain suited to the nature and duration of the work. A hazard control measure like PPE might be suitable for a quick task that lasts only 2 minutes but the same item of PPE may not be able to withstand 3 hours of continuous use. Here are some examples:
- EXAMPLE 1: You transfer several drums of chemicals to an outdoor area. You have been using a drum dolly to hold and transport the chemicals around the warehouse. An inspection reveals sun damage to the dolly after only a few months of outdoor use. After checking the original specs, you realised the dolly was never designed for outdoor use and has no UV protection. The dolly is therefore not suited to the nature of the work.
- EXAMPLE 2: Your cleaning staff use a new corrosive floor stripper to clean the floors of the warehouse, dispatch dock, and factory every day. You issue chemical resistant gloves and aprons from your usual supplier but discover that the gloves and aprons are failing after only 1-2 hours of use. While they are suited to the chemical under light use, they cannot withstand a heavy workload. The gloves and aprons are not fit for the duration of the work.
Your personal protective equipment is a risk control that must be suitable for the nature of the work.
3. Installed, Set Up and Used Correctly
Finally, you will need to have systematic review procedures in place to ensure that each chemical control measure has been installed, set up and used correctly.
Sometimes problems don’t emerge with chemical risk control measures until after the equipment, machine or safety device is in use.
Consider these examples of how the improper installation, set up or use of risk controls can impact the safety of your workplace:
- EXAMPLE 1: You have purchased a gas bottle cage and have your maintenance crew install it outside. But a site inspection indicates the cage is located within the turning circle of delivery vehicles and has no protection from vehicular impact. It is a requirement of AS4332 - The storage and handling of gases in cylinders that cylinder stores have bollards, crash barriers or other protective devices when there is a risk of damage from vehicles. The gas bottle cage has not been installed correctly.
- EXAMPLE 2: You create a Register of Hazardous Chemicals and purchase a waterproof document box to attach it to the chemical stores. But the box only contains a list of the chemicals in the store and does not include any of the Safety Data Sheets (SDS). The Register of Hazardous Chemicals has not been set up correctly.
- EXAMPLE 3: You have purchased a gas bottle trolley for transferring cylinders around the job site. The trolley is manufactured to Australian Standards and is complete with straps to restrain the cylinders while on the trolley. After a safety audit you notice that some workers are transporting cylinders without properly securing the cylinders with the straps. The gas bottle trolley is not being used correctly and is likely to fail as a control measure.
Ensuring WHS Compliance with Your HAZCHEM and Dangerous Goods
The best way of ensuring that your chemical risk control measures are installed, used, and maintained correctly is to implement Storemasta’s 4-step risk management methodology. To learn more about it, simply access your free copy of our eBook to ensure workplace health and safety. This eBook can guide health and safety representatives in your workplace to control chemical risks with practical tools and templates. Access your copy to control safety risks straight away.
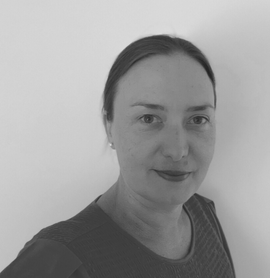
Living life by the 4 C’s of marketing – communication, coffee, compliance… and more coffee – Leisa Andersen is Storemasta’s Content Marketing Manager. When she’s not writing, you’ll find her enjoying all the good things in life, including shopping, travel and gluten free donuts.