Contents
- What is a Dangerous Goods Training Course?
- What Topics are Included in DG Awareness Training?
- How Often Should Dangerous Goods Training Occur?
- Who Should Take a Dangerous Goods Course?
- What DG Training is Required?
- What Types of Dangerous Goods Training are Available?
- How do you Keep Staff Interested in DG Training?
- DG Training Courses for your Workplace
What is a Dangerous Goods Training Course?
What Topics are Included in DG Awareness Training?
How Often Should Dangerous Goods Training Occur?
Who Should Take a Dangerous Goods Course?
What DG Training is Required?
What Types of Dangerous Goods Training are Available?
How do you Keep Staff Interested in DG Training?
DG Training Courses for your Workplace
In every organisation there is risk — and (hopefully) — sufficient measures to control it.
But one of the most crucial and often overlooked safety measures is adequate staff training to help staff identify any dangers on-site and prevent incidents from occurring. When hazardous chemicals and dangerous goods are involved, the training of staff needs to be performed to ensure health and safety for the workplace.
In every state of Australia there is legislation requiring employees to provide a duty of care to ensure the health and safety of workers, which includes provision of training to employees to ensure they are informed and educated on the risks in the workplace they may be exposed to.
As it relates to hazardous chemicals and dangerous goods, some of the common questions from employers are, 'What topics need to be covered, how often should training occur, and in what formats should dangerous goods courses be held?"
This post will give you the answers to these common questions, so you can consider how to incorporate dangerous goods training into your operations.
We spoke with DG Trainer Managing Director David Irvine from Storemasta Academy to find out more about dangerous goods training for organisations handling these harmful substances and articles.
What is a Dangerous Goods Training Course?
There are various types of dangerous goods training that range from the safe storage and handling of dangerous goods all the way to the transportation of dangerous goods safely by air, sea or road/rail.
This training focuses on making participants aware of situations where compliance requirements may occur and how to do things in a safe manner.
"Dangerous goods courses are a vital part of site safety and must address the general hazards that staff are managing, as well as the vital controls that are required to reduce risk," explains David Irvine from DG Trainer. "
"Training courses can span from an hour to a full day (or multiple days) of training, depending on the nature of work being done, the amount and type of dangerous goods that are being eealt with and the relevant regulatory compliance obligations."
IMPORTANT: Storemasta Academy offers on-site and online training, which is flexible, affordable and practical for any workplace managing DG risk. Learn more about the dangerous goods training options here.
What Topics are Included in DG Awareness Training?
When it comes to dangerous goods awareness, staff require a broad overview of the potential hazards associated with their substances, as well as the controls to decrease risk and their legal requirements.
Dangerous goods awareness may cover a wide range of topics designed to educate workers on the safe handling, storage and transportation of goods.
Training for dangerous goods handling, storage and transport is an essential safety measure.
It will also cover the compliance requirements associated with hazardous chemicals or dangerous goods, as per the regulatory bodies in the region ie. WHS laws for that state or territory in Australia, or the Dangerous Goods Laws (DG Act) that applies to workplaces in Victoria.
Here is a general rundown of some of the topics that you may find in a dangerous goods awareness course:
- Dangerous Goods Essentials – including the classes and divisions of dangerous goods, their hazards and their UN numbers.
- Legal Requirements – including state, national, and international regulations that apply to the storage and handling of dangerous goods, and transportation. The responsibilities of employers and staff, plus consequences for non-compliance with these laws.
- Labelling and Packaging - understanding Safety Data Sheets (SDS), labelling and GHS classification systems/pictograms for hazardous chemicals.
- Storage Requirements for Dangerous Goods – covering all the essential requirements for safe DG storage including spill prevention, segregation, ventilation and storage equipment. Staff must also be able to read and understand SDSs and signage, so that they are aware of how to store these sometimes volatile substances and articles.
- Handling and Transport of Dangerous Goods – including requirements from the relevant regulations if transporting by air (IATA DGR), sea (IMDG Code), road & rail (ADG Code) to cover hazards during transport, packaging and documentation of goods in transport.
- Risk Controls – from risk assessments of the site to storage, handling, transport controls, as well as the use of personal protective equipment and administrative controls.
- Emergency Response – staff must be trained for emergency response and evacuation procedures. They must know exactly what to do in the event of a spill, incident of human harm or other dangerous goods accident onsite.
IMPORTANT: Like to learn more about the training required for hazardous chemicals and dangerous goods? Visit the Knowledge Centre for information about online and on-site training to improve safety and compliance with your team.
How Often Should Dangerous Goods Training Occur?
When it comes to sustaining health and safety in a work environment, there’s a myriad of factors to consider. And one of the most important measures is ensuring that staff are properly trained to both understand the risks at the site, as well as know how to prevent any accidents and incidents.
When staff are working with dangerous goods and hazardous chemicals, this importance is compounded, as there are so many hazards associated with a chemical product. Staff must also understand how chemicals could harm staff, property or even the surrounding environment.
This is where the importance of dangerous goods training comes in. But how often does it need to be conducted?
Generally dangerous goods training should occur every 1 to 2 years, depending on any regulatory requirements or significant changes in personnel, processes, hazards and other circumstance.
“In most cases, the training should occur at least before an employee is required to perform a new role or operate within an environment that involves dangerous goods.”
- David Irvine, DG Trainer
Staff communication and training is a vital part of the entire risk control process for any organisation carrying dangerous goods or hazardous chemicals in any quantity.
It’s important to have dangerous goods awareness training from the moment staff set foot on site. Whether staff are handling dangerous goods or working in a space close to storage or handling operations, all team members must have a general understanding (at a minimum) of the dangers that may be present at their site so they can fulfil their workplace health and safety obligations.
Ongoing training, to both refresh the awareness of existing staff as well as combat new risks at the site, is an important part of sustaining WHS compliance. Without a cohesive and ongoing training program, your staff may not be fully equipped to deal with the dangers that are present in their working lives.
IMPORTANT: Like to know more about your obligations in relation to dangerous goods? Read our popular blog to find out what your responsibilities are in relation to ensuring workplace health and safety.
Who Should Take a Dangerous Goods Course?
“Anyone required to handle dangerous goods or to work around dangerous goods requires training under WHS requirements, but workplaces should consider some form of training for anyone on site,” explains David Irvine from DG Trainer.
If staff are handling or storing dangerous goods, they may also have to undertake specialised training, such as Spill Response Training, so they are fully equipped to deal with hazardous situations in their daily duties. Without adequate training in the safe handling of dangerous goods or managing incidents, staff risk serious injury or even death.
Even staff who aren’t directly handling or storing goods – such as office personnel – must have a general understanding of the dangerous goods and the hazards they present.
In an emergency or evacuation, all staff must have the knowledge to safely exit the site and understand the hazards posed by the dangerous goods on-site.
What DG Training is Required?
But what DG training is required in Australia?
“The first thing to say is that there is some training (such as the consigning of dangerous goods by air and sea) that has mandated training content and frequency of training that is managed by a Regulator,” says David Irvine, DG Trainer.
“There is the general workplace health and safety requirement to provide training for any person or employee that is required to function in a workplace environment that includes the hazards caused by the storage or handling of dangerous goods."
"Examples include warehouses where dangerous goods are stored, or loaded/unloaded, manufacturing processes, maintenance and hot work around dangerous goods,” he explains.
Warehouse require DG training due to the many hazards that are present, as well as the safety issues of manufacturing processes, ignition sources and other risk management considerations.
REMEMBER: Staff must also be suitably trained on other aspects of their work environment, including how to perform their duties in a safe manner, how to put on and take off PPE, and how to use chemical storage equipment, bunds, handling equipment and other chemical risk control measures.
What Types of Dangerous Goods Training are Available?
It’s a good idea to think about the types of dangerous goods training that would be most effective for your team and your organisation. Keeping the sessions engaging, interesting and relevant for the job site is an essential part of DG courses.
Options can include onsite courses, webinars and online DG courses. You can also incorporate various other formats to make sure that staff are continually engaged in their learning process. Training, just like the jobsite, is continually changing, and keeping abreast of new technologies, as well as the latest information, is imperative for organisations that are dealing with the hazards of dangerous goods.
"Training and information provision can include induction of new employees, team meetings and toolbox sessions. Meetings that include consultation and feedback can also be an effective addition to formal training.”
- David Irvine, DG Trainer
How do you Keep Staff Interested in DG Training?
If staff are struggling to understand the information or maintain concentration during the sessions, consider giving them a follow-up training session – perhaps with an online component or onsite module that directly speaks to the tasks they perform during their work week.
As people learn at different speeds – and in different ways – it’s vital that all staff have the ability to absorb the information. Afterall, the dangerous goods training could be the difference between them staying safe at work – or being responsible for an incident, such as a chemical spill or flammable liquids fire.
Any staff members working with dangerous goods need to understand how they must handle, store and transport the chemicals in order to maintain safety.
Engagement, understand, interest and accountability are all important components of the staff training process. In addition to this, if staff are properly informed of the potential dangers at their site - they will more likely absorb the information as it appears more relevant to them.
If staff aren't actioning the procedures and protocols explained in the training, perhaps do some one-on-one training with them onsite, and ensure that supervision is always carried out, so they remain safe in their daily duties.
REMEMBER: It's not just the workplace that is obligated to perform training. Staff must ensure a safe work environment. This is a requirement of the WHS Regulations. Therefore, if there are any unsafe practices, the staff member must be notified immediately so that more training - or disciplinary action - can be undertaken. Failure to do so could result in non-compliance and/or an incident.
DG Training Courses for your Workplace
To find out more about hazardous chemical and dangerous goods training for your organisation, why not get in touch with us for a group booking price. In addition to this, you can download our easy-to-read eBook so you can understand how our 4-Step Risk Management Methodology can improve health and safety in your operations. The eBoo How To Manage The Risk Of Hazardous Chemicals In The Workplace includes a downloadable risk management matrix template, plus helpful tips on hazchem and DG risk management. Get your copy today to find out more about ensuring a healthy, safe environment for your team and community.
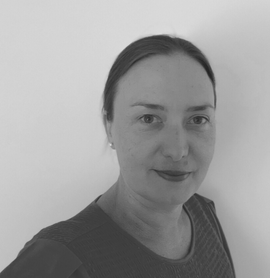
Living life by the 4 C’s of marketing – communication, coffee, compliance… and more coffee – Leisa Andersen is Storemasta’s Content Marketing Manager. When she’s not writing, you’ll find her enjoying all the good things in life, including shopping, travel and gluten free donuts.