Why Do Golf Club Operators Need to Consider Chemical Safety?
What are Some Dangerous Goods used at Golf Courses?
Why is Chemical Safety Important for Golf Courses?
Dangerous Goods Storage Solutions for Golf Clubs and Golf Courses
Managing Hazardous Chemicals in Golf Clubs
When you think of the golf course, it's all about vast greens, linen shorts and having a relaxing drink at the end of a game. But for operators of golf courses — and related businesses such as golf buggy maintenance — there are some safety hazards to consider and control to ensure that everything is above par. In this post, we look at dangerous goods risk management for golf clubs - highlighting some simple tips to apply at your business to control risk with commonly used DG classes including flammable liquids, corrosives and toxic substances.
Why Do Golf Club Operators Need to Consider Chemical Safety?
Managing dangerous goods, such as certain chemicals or substances associated with golf clubs, involves careful consideration of safety protocols, regulations, and best practices.
This is to ensure that the required chemicals being used as being done so safely, as well as their storage and handling is being controlled in a way that effectively reduces risk. Chemical safety is a vital issue for golf courses and club as it impacts the health and safety of members and guests and the protection of the natural environment. It also allows the club to maintain it's manicured and pristine environment, which is essential for operational purposes.
While golf clubs themselves are not typically considered dangerous goods, some associated items or materials — such as cleaning agents, fertilisers, fuels or batteries — may pose risks.
There are a range of chemicals used to operate and maintain golf courses and clubs, including pesticides and other garden chemicals.
Here are some general guidelines for dangerous goods risk management that apply to golf clubs:
Identify and Classify Hazardous Materials
Identify any hazardous materials associated with golf club maintenance or operations. This could include chemicals used for cleaning, pesticides, or fuels for maintenance equipment.
Understand Regulatory Requirements
Familiarise yourself with regulations governing the transportation, storage, and use of dangerous goods. Information about your local regulator and additional information and resources, such as Codes of Practice, can be found on the Safe Work Australia website.
Implement Safety Procedures
Develop and implement safety protocols for handling, storing and transporting of hazardous chemicals and dangerous goods. This may include proper labelling, DG signage and hazard signage, storage in designated areas, ventilation for handling or storage areas, and the use of personal protective equipment (PPE). Standard operating procedures for chemical storage equipment and chemical safety training should also be integrated into your strategy to ensure procedures are being followed.
Training and Awareness
Ensure that staff involved in handling or managing dangerous goods receive proper training. This should cover safe handling practices, emergency response procedures, and awareness of potential risks.
Emergency Response Plan
Develop and communicate an emergency response plan that includes procedures for dealing with spills, leaks, or other incidents involving hazardous materials. Ensure that all staff members are familiar with these procedures. Don’t overlook emerging risks, such as lithium-ion batteries, as these can also cause hazards for businesses – especially golf clubs that are charging buggies and other equipment.
Secure Transportation
If transporting dangerous goods, ensure that the vehicles used comply with transportation regulations for hazardous materials. Proper labelling, packaging and documentation are essential.
Regular Inspections and Maintenance
Conduct regular inspections of storage areas, equipment, and facilities to identify and address potential hazards. Regular maintenance of equipment can also help prevent accidents caused by misuse, vandalism, damage or aged equipment.
Communication and Coordination
Foster open communication between staff members, suppliers, and relevant authorities regarding the handling and transportation of dangerous goods. Establish clear lines of communication in case of emergencies.
Record-Keeping
Maintain accurate records of all hazardous materials on-site, including quantities, storage locations, and relevant safety data sheets (SDS). This information is crucial for emergency responders and regulatory compliance.
Review and Update Policies
Regularly review and update your dangerous goods risk management policies to incorporate any changes in regulations, technology, or best practices.
It's essential to tailor these general guidelines to the specific needs and circumstances of your golf club facility. Consulting with relevant regulatory authorities or seeking professional advice can also help ensure comprehensive and compliant dangerous goods risk management.
What are Some Dangerous Goods used at Golf Courses?
While golf courses typically don’t use a large number of hazardous chemicals, as compared with manufacturing or industrial operations, there are some substances that can be considered hazardous or dangerous goods due to their potential risks to human health or the environment.
The specific chemicals used can vary depending on the maintenance practices, pest control measures, and landscaping requirements of each golf course.
Here are some examples of dangerous goods used for golf course operations:
Pesticides and Herbicides:
Many golf courses use pesticides and herbicides to control weeds, insects, and diseases on the turf. Common chemicals include glyphosate (found in some herbicides), insecticides like bifenthrin or imidacloprid, and fungicides.
Class 3 Fuels:
Golf course maintenance equipment, such as lawnmowers and tractors, often use petrol or diesel fuel. These fuels are either flammable or combustible, and therefore can create a fire or explosion hazard if they’re not managed properly.
Paints and Turf Marking Dyes:
Some maintenance activities involve the use of paints or turf marking dyes. These products may contain hazardous substances, and their use requires proper handling and disposal.
Aerosols:
Products like insect repellents, lubricants, or cleaning sprays in aerosol form may be used at golf clubs for a range of applications. These aerosols contain harmful and flammable substances. The can can also present a projectile risk if kept near heat, direct sunlight or incompatible materials.
Lithium-ion Batteries:
Whether it’s charging golf buggies, phones, laptops or other devices, lithium-ion batteries are recognised as a Class 9 dangerous goods that can pose a fire hazard. Special consideration needs to be given with the handling, storage and charging of this energy source.
Pond and Water Treatment Chemicals:
Golf courses often feature ponds, waterfalls and other water features. However, there is maintenance to consider with any bodies of water to ensure water quality. Chlorine, algaecides or herbicides may be required to maintain golf course water features.
Cleaning Agents:
Various cleaning agents may be used for equipment maintenance or clubhouse cleaning. These can include solvents, degreasers, or other chemicals that may be flammable or harmful if not handled correctly.
Why is Chemical Safety Important for Golf Courses?
It's important for golf courses to carefully manage and monitor the use of these chemicals, following safety guidelines, proper storage practices, and disposal regulations. Without these controls, any business may be susceptible to hazards including leaks and spills, fires, chemical reactions and harmful vapour emissions.
Golf Club staff should be trained on the safe handling of dangerous goods, as well as the correct use of all chemical storage and handling equipment. Safety Data Sheets (SDS) must be readily available for all substances used on the golf course, ideally stored in a document holder attached to a chemical cabinet or store.
Regular inspections and risk assessments of the golf club and golf course can help ensure a safe environment for both employees and visitors. Whenever a new hazard is introduced, such as a different chemical for use or an altered work practice, the controls must again be inspected and assessed to ensure that they’re doing their job. In addition to this, emergency plans need to be updated to include all current hazards identified in the reports.
Protecting people, property and environment is essential for any business managing dangerous goods.
Dangerous Goods Storage Solutions for Golf Clubs and Golf Courses
If you’re wondering what controls are best suited to your onsite dangerous goods, we’ve compiled a visual list of products that can be utilised at golf courses and golf clubs to control the hazards associated with the various chemical classes.
Problem: Fuel and other flammable liquids
Solution: Choose a Class 3 Cabinet to store smaller volumes
Problem: Pesticides
Solution: Purpose-built Pesticide Cabinet for indoor storage
Problem: Lithium-ion batteries
Solution: 8 or 18 outlet Battery Charging Cabinet to control battery fire hazards
Problem: Toxic chemicals
Solution: If chemicals are classed as toxic, they may stored in a Class 6 Safety Cabinet or, for larger quantities such as IBCs, a Class 6 Outdoor Store
Problem: Aerosol cans
Solution: Aerosol cages reduce risk of fire and projectile damage
REMEMBER: Always check your safety data sheets to ensure that the chemicals that you’re storing are suitable for the class of cabinet or store that you’re considering. There are some restrictions on the volumes of chemicals that can be stored indoors, so this must also be determined. Alternatively, speak to our Dangerous Goods Storage Consultants who can guide you in the right direction.
Managing Hazardous Chemicals in Golf Clubs
If you’d like to learn more about improving dangerous goods safety for your golf club, we have an easy-to-read guide that can help make the whole process simpler. This eBook offers the Storemasta risk management methodology so you can systematically Identify – Assess – Control – Sustain chemical compliance at your golf course and club. Get your copy for free today or reach out to one of our trained DG Storage Consultants for a tailored solution.
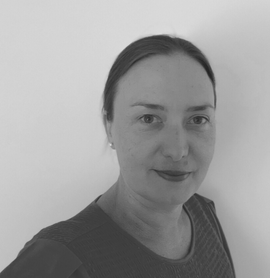
Living life by the 4 C’s of marketing – communication, coffee, compliance… and more coffee – Leisa Andersen is Storemasta’s Content Marketing Manager. When she’s not writing, you’ll find her enjoying all the good things in life, including shopping, travel and gluten free donuts.