We often discuss controls for onsite chemical risks, but we don’t always discuss the challenges that face remote worksites. Many businesses operate in isolated locations, with mining, agriculture, gas and oil just some of the industries that rely on remote worksites. To help keep all staff safe and operations running smoothly, we have created this blog to specifically discuss dangerous goods safety on remote worksites. We’ll be detailing some key points to consider, as well as offering a range of chemical controls that can be implemented at remote sites.
What Chemical Risks are Present at Remote Worksites?
When you’re working in a remote location, you’re dealing with several main issues that can affect chemical safety: isolation from services and emergency assistance, and temporary and/or harsh environments for staff to operate from.
Many industries have remote workers, temporary staff or FIFO teams who man their operations. Whether it’s an agricultural enterprise, a gold mine, an oil & gas site or a forestry department, the vast majority of these businesses rely on some type of hazardous chemical or dangerous goods in their day-to-day duties.
However, without a static working environment, such as an established factory or workshop in a more central location, there are many extra considerations that businesses and their staff have to make to ensure the chemical safety of their operations.
Many industries rely on remote worksites to power their daily operations.
Add to this a range of factors — including new or temporary workers, extreme weather conditions, limited communications, and a lack of fire or ambulance services — and you have a situation where chemical hazards can become major incidents.
Some chemical hazards on a remote site could include:
- Flammable liquids fire that spreads to the outdoor environment
- Toxic spillage, leading to human harm
- Corrosion of equipment, property and living tissue
- Combustion of oxidizing substances resulting in fire or explosion
- Chemical reactions caused by improper chemical segregation
- The unintended ignition of explosive devices
Like to know more about chemical segregation?
However, there are some staple solutions that you can implement and maintain at remote worksites. These layers of protection will assist in reducing harm to your workers, as well as helping to protect place and environment from the various risks associated with dangerous goods.
Weather and Climate
From the Northern Territory to Tasmania, our country is home to some extreme weather conditions that can impact the chemical safety of remote operations.
Cyclones, floods, heatwaves, bushfires and dust storms are just some of the natural phenomena that Australian businesses must navigate when they set up shop in remote locations. The dangers associated with hazardous chemicals and dangerous goods increase when you’re also dealing with extreme weather conditions and large variations in temperature.
Whether chemicals are being transported, transferred, stored or handled, staff must be aware of the conditions required to keep chemicals and dangerous goods safe and stable.
We suggest the following when considering chemical storage and handling:
- Always make sure that the temperatures at your site are within the safe range for your chemical products
- Choose storage locations that are above the known flood level
- Ensure that any trees, bushes and grass are trimmed and kept away from your chemical stores and handling areas
- Remove rubbish and debris from your site daily as this can create a fire hazard, as well as impact damage during storms
- Select outdoor storage that is equipped for your environment with correct cyclone rating
- Have cambered roofs on outdoor stores to assist with rain run-off
- Install a parasol shade above your outdoor stores if sunlight and extreme heat are an issue at your site
- Have adequate fire protection onsite, even in your vehicles and temporary operations
- Create emergency plans for natural disasters such as floods, cyclones or bushfires
You must implement measures to help protect your chemical handling and storage areas from extreme weather conditions and natural disasters.
Dangerous Goods Security
In remote locations, you can’t just call up your local supplier and get a small order of Class 3 Flammable Liquids delivered the next day.
Remote worksites rely on bulk chemical shipments and larger quantities of onsite chemicals to run their operations. In addition to the volume of dangerous goods that need to be kept on the worksite, there is also the need to provide security to ensure that your chemical products aren’t tampered with, stolen or used for malicious purposes.
Chemicals should always be kept in a secure location – whether that’s in an indoor cabinet in a secure building, or in a dangerous goods container with durable locking bars.
Outdoor chemical storage is often the most practical option for remote sites, due to the volume of chemicals that remote worksites require. However, you should make sure that your outdoor storage containers are equipped with suitable locks, such as ISO locking bars for maximum protection.
Security for your dangerous goods stores must be a top priority when working in remote locations.
Emergency Equipment
Is your site prepared to effectively deal with a chemical emergency? Would each of your staff members, including temporary and FIFO workers, know exactly what to do if a large chemical spill occurred or a toxic gas was released?
The provision of emergency equipment and decontamination stations is vital for all businesses. However, when emergency services are sometimes hours away, remote worksites must be prepared for any type of emergency situation that may occur.
In addition to the provision of emergency equipment and decontamination facilities, remote operations must also make sure that there is sufficient:
- Cleaning and maintenance of safety showers and eyewash stations
- Restocking of first aid kits
- Refilling and re-ordering of spill kits and their contents
- Staff training and supervision
- Regular inspections and reviews of all emergency facilities
Relocatable Chemical Storage
While many businesses can manage working with a few safety cabinets kept in an indoor location, remote worksites often rely on outdoor relocatable storage.
Relocatable outdoor chemical storage can be a durable and cost-effective option for organisations in remote locations.
Outdoor chemical storage can be in the form of:
- Dangerous goods containers – fully relocatable models that can be transported by road or air to the remote location. Some models can be lifted when stocked, as well as stacked on top of each other for larger volumes of chemical storage. Maximum capacity of 8000L.
- IBC or drum stores – suitable for the storage of most classes of dangerous goods, IBC and drum stores offer a secure, bunded storage space for toxic substances, organic peroxides, flammables and more. This type of store is capable of storing up to 10 chemical IBCs.
- Smaller chemical stores – if your site has multiple classes of chemicals or smaller quantities of a particular class, a small chemical store (such as our Miniseries) may be a preferable option. These compliant stores can hold 250 – 850L of chemicals.
Remember, if your business is working with dangerous goods, you must conduct a risk assessment to determine the type of storage that is required. Generally, your Safety Data Sheets should be the first documents that you reference to gain details about the handling and storage of your chemical product. You can then determine the dangerous goods class of your products, before selecting relocatable outdoor chemical storage that suits your operational needs and capacity requirements.
IMPORTANT: Our team at STOREMASTA can assist with advice on storage solutions that are safe and practical for your specific chemical products.
Vehicles and Transport
A key consideration when dealing with remote worksites is the reliance on vehicles and transport for staff.
Spill kits must be placed in vehicles, in case of an oil or fuel leak when staff are on-the-move.
When staff are carrying dangerous goods in work vehicles, consider the provision of:
- Personal protective equipment (ie. clothing, footwear, glasses, breathing apparatus), suitable for the type of chemicals that are being transported
- Vehicle spill kit (ie. chemical spill kits, hydrocarbon kits, marine kits etc.) to use in the event of a leak or spill
- Collapsible portable bunds to contain leaks and spills
- Correct storage for transported dangerous goods, such as gas bottle cages for trucks and utes
- Handling equipment to assist with work tasks, such as a gas cylinder trolley
- Communication devices appropriate for the location, such as satellite phones or 2-way radios
- First-aid equipment, such as trauma bandages, splints and eye wash kits
- Portable eyewash stations for emergency decontamination
- Implement GPS tracking or an emergency position-indicating radio beacon, in the event of a breakdown, incident or emergency
Spill Containment
Whether you’re carrying a small quantity of chemicals or you order in bulk, you must prevent, contain and clean-up any hazardous chemical spills or leaks. Even the smallest leak — from a damaged fuel tank or a split chemical container — can cause major issues for a workplace, let alone a remote worksite.
The issue of spill prevention and containment, however, is made a little more complicated when you’re dealing with temporary sites or remote locations.
Remote sites may rely on a mixture of fixed and portable secondary containment solutions.
Consider the following spill prevention equipment, to stop spills affecting staff, property and the natural environment:
- Temporary bunding – this light-weight and easy-to-use bunding is perfect for remote locations. Use the bunding under drums or IBCs, as a temporary spill containment solution.
- Drive-in bunding – if your vehicles require servicing, repairs or re-fueling, use the drive-in collapsible bunding to prevent fuels and oils from contaminating the natural environment.
- Bunded storage – all indoor and outdoor storage should be equipped with a compliant spill containment system that meets the requirements of the Australian Standards.
- IBC bunds – when staff are accessing IBCs for chemical transferal, make sure they are using an IBC bund to catch any chemical spillage.
- Drum bunds – if your operations require the use of oil or chemical drums, use a drum bund to contain leaks and spills.
- Bunded handling equipment – spills don’t only happen during storage or transferal, they can also occur when containers and drums are being moved around a site. Use bunded handling equipment to prevent chemical spillage during daily operations.
t’s extremely important, in a remote and natural environment, that hazardous chemicals don’t enter land or waterways, as this will affect flora and fauna.
Dangerous Goods Safety For Your Remote Site
From spillage prevention to emergency decontamination, being prepared is key when working with dangerous goods in a remote location. If you’d like to find out more about creating a safer working environment, why not download our eBook?
Our guide will lead you through the key considerations for spill prevention, so you can avoid dangerous and costly situations such as corrosion of property, toxic contamination, and fire and explosion. Grab a copy of our eBook today and learn more about improving chemical safety through secondary spill containment.
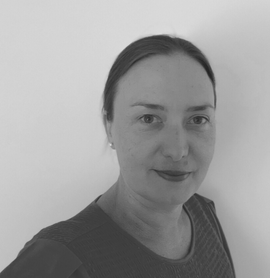
Living life by the 4 C’s of marketing – communication, coffee, compliance… and more coffee – Leisa Andersen is Storemasta’s Content Marketing Manager. When she’s not writing, you’ll find her enjoying all the good things in life, including shopping, travel and gluten free donuts.