Improving chemical safety is crucial for protecting health and the environment. But many businesses don’t know where to begin. But the good news is we’re here to tell you that is doesn’t have to be a drawn-out, overwhelming task. In fact, there’s some vitally important steps you can take TODAY that will immediately improve chemical safety in your workplace.
What are we waiting for? Let’s get into the 10 tips now:
1. Control your Chemical Inventory
The quantity of dangerous goods at your site can increase your risk. So why not start with keeping better control over your chemical inventory.
Where possible, substitute hazardous chemicals with less hazardous alternatives, and implement processes to minimise the quantities of chemicals used. This may mean only ordering when you need to, reducing stockpiles and looking for alternatives that may not pose the degree of harm that your existing chemicals do.
Controlling your chemical inventory will not only reduce the volume of harmful substances that you’re storing onsite, but it will increase your awareness of quantities and usage. Therefore, you’ll be more likely to notice any unauthorised access, spillage or other chemical wastage associated with your substances.
REMEMBER: Controlling your inventory of chemicals can be part of an administrative controls strategy. Find out more about administrative controls for dangerous goods by reading our blog.
2. Ensure Correct Labelling and Signage
Awareness is such a crucial part of risk management. And something as obvious as a chemical label, dangerous goods diamond, hazard or warning sign may be the difference between an incident or just another day on the job.
GHS labelling system is an internationally recognised way of identifying and labelling substances. While new products should be marked in line with this system, it’s also imperative that your staff understand how to interpret these labels and signs, to ensure health and safety with their usage. Identification of the symbols and hazard warnings will alert your staff to any safety issues that may occur. Without this understanding of the labelling and signage, you won’t be able to ensure health, safety and compliance in your operations.
Which brings us to the next point…
3. Train your People
You can’t lower the risks involved with dangerous goods and hazardous chemicals if your staff are in the dark about the dangers involved with handling and storage – and how to protect themselves by using the appropriate controls. Train all employees on the hazards and properties of each chemical that they use, as well as how they should be managed to reduce the likelihood and impact of those hazards. This includes a full range of training on chemical safety protocols, proper handling including PPE, workplace hygiene, storage equipment usage, first aid, emergency decontamination processes, and evacuation and emergency procedures.
IMPORTANT: Training your team to identify and control hazards is a WHS obligation. Find out more on how to implement Hazchem Safety Training by reading our popular blog post.
4. Store Safely
You may call us biased, but the truth is – safe, compliant storage is one of the simplest and fastest ways to reduce chemical risk.
The storage should be designed and made to meet safety and quality standards. It must also be suitable for the class or division of dangerous goods that you’re storing — as well as the quantity.
Storage is one of the most important ways to reduce chemical risk in a workplace.
Within the storage equipment, whether it’s a Dangerous Goods Storage Container or a Flammable Cabinet, it’s important to ensure that all containers, drums and IBCs are fit-for-purpose and in good condition. This will prevent incompatibilities with chemicals, as well as prevent leaks and spills from cracked containers or those will ill-fitting lids.
It’s also essential to consider how staff are using the DG storage – how to load and stack chemical containers, how to close doors or inspect for spills, and when to alert supervisors if there appears to be an issue with the functionality of the equipment (such as a door that’s been damaged and won’t shut, or a spill sump that hasn’t been cleaned out)
IMPORTANT: Also consider how you are keeping your ‘empty’ gas cylinders or chemical containers. Often, these vessels must be stored and segregated in the same way that a full container must be as harmful residue will remain. Keeping empty chemical vessels safe during the waste recycling or disposal process is part of ensuring dangerous goods safety.
5. Segregate
While dedicated storage for each dangerous goods class or division is the first step to controlling hazards, ensuring successful segregation in all handling and storage areas is vital for health and safety.
Segregation is the task of identifying substances or materials which should be separated to avoid further hazards. Some chemicals may react with each other or create an incident such as a fire or explosion.
Check your safety data sheet and refer to the dangerous goods segregation chart to further determine the correct distances and procedures for segregating incompatible goods in your workplace.
REMEMBER: Look at the primary risk as well as the subsidiary risk of any dangerous goods that you’re storing. These goods must be segregated, with both primary and subsidiary risks considered.
6. Inspect Bunding
Your spill containment bund – whether it’s floor bunding, a bund in a safety cabinet, an IBC bund or a portable option – is your best protection against accidental releases in the workplace. However, there’s no safety benefits to this equipment if you aren’t regularly inspecting and cleaning out your bunds.
Dangerous goods can quickly pool in bunds, creating issues such as flammable or corrosive vapours, or oxidising gases. The sooner leaks and spills are identified, controlled and cleaned up, the sooner the hazardous situation will be effectively managed. When inspecting your bunds, you'll also notice if the bund is no longer suitable for the chemical or the quantity that you're carrying. Alternatively, you'll notice any signs of age or damage that may decrease the effectiveness of your spill bunding systems.
REMEMBER: Spill protection is required to reduce chemical risk. Get your copy of our free eBook How to Protect Your Business from Chemical Spills for easy, actionable steps to ensuring spill safety.
7. Use PPE Properly
Using Personal Protective Equipment (PPE) properly is crucial for ensuring chemical safety for several reasons including protection against exposure, prevention of illnesses or injuries, creating a safety culture and hazard awareness,
However, personal protective equipment is only effective when used as intended. Improper use, such as wearing ill-fitting equipment or poorly maintained equipment, reduces its ability to protect you. Therefore, choosing the correct PPE for your chemicals, staff and task – as well as training staff on how to put it on and take it off safely, should be part of your safety training. In addition to this, we recommend you store your PPE in a dedicated PPE cabinet, so it will be easily accessible and remain in good condition for longer.
PPE must be decontaminated and maintained properly, so it’s suitable for use for the next chemical handling task. Don’t forget to regularly review and inspect your PPE maintenance practices, as well as staff training, to ensure everyone is maximising the effectiveness of the protective gear.
8. Review Accident, Incident and Illness Reports
How can reviewing incident reports help you improve safety? While it’s unfortunate that workplaces accidents and illnesses do occur, there are valuable and timely lessons that can be learned if the appropriate investigations and reviews are completed.
While major incidents, known as ‘notifiable incidents’ must be reported to Regulators, there are many other near-misses, exposure incidents and mishaps that may be overlooked in a workplace.
That’s why it’s good practice to record and investigate each safety issue that may arise, so that you can discuss how to control the hazard in the future and prevent further accidents, incidents or illnesses from occurring.
9. Check your Safety Data Sheets are Current
Your safety data sheet is the quiet achiever when lowering chemical risk. This document outlines all the necessary precautions you need to take to make sure your chemicals are being handled, stored and transported in the right way. However, Australian regulations state that these safety data sheets must be updated after 5 years, so if you’re not using the latest safety data sheet, get in touch with your supplier or distributor to obtain the updated copy.
Storing SDS in a dedicated folder and waterproof holder helps to maintain scompliance and safety.
Without a current safety data sheet for your staff to refer to, you are risking non-compliance. You’re also potentially putting your organisation at risk, if the properties, hazards and subsequent precautions of the substance have changed.
We also recommend keeping your safety data sheets in a waterproof document holder attached to your particular dangerous goods cabinets or stores, so staff instantly know where to look for information on the stored chemicals.
REMEMBER: Storemasta offer a range of SDS Folders and Document Holders that can keep all your safety data sheets and chemical information safe and dry. Explore the secure storage range online to find out more.
10. Conduct Regular Inspections & Audits
Workplaces are forever changing, with new chemicals, quantities, staff, tasks and equipment to keep you on your toes when managing risks.
That’s why creating a regular inspection and chemical safety audit plan will help you stay on top of your WHS matters. If your team don’t have the expertise to conduct thorough inspections and audits, why not consider a Dangerous Goods Consultant who can help you accurately manage risks in your organisation?
We recommend creating inspection checklists for all your controls, so you can quickly identify issues such as cracked chemical containers, excessive chemical vapours, damaged storage equipment, damaged PPE, damaged dangerous goods signage and more.
IMPORTANT: If you work with safety cabinets, get a copy of our handy Cabinet Checklist to kick off your regular storage equipment inspections.
Simplifying Chemical Safety
By following these 10 tips, you can significantly reduce the risk of chemical accidents and create a safer environment for everyone involved. However, there are many considerations to make when working with dangerous goods and hazardous chemicals in your operations. To learn more about managing risks, why not access a copy of our free eBook. This guide will take you through the Storemasta 4-step risk management methodology and offer simple solutions to help you create a healthier, safer workplace. Get your copy now to learn more.
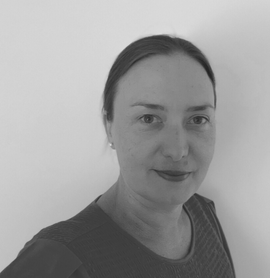
Living life by the 4 C’s of marketing – communication, coffee, compliance… and more coffee – Leisa Andersen is Storemasta’s Content Marketing Manager. When she’s not writing, you’ll find her enjoying all the good things in life, including shopping, travel and gluten free donuts.