Almost every workplace has equipment, machinery or vehicles powered by flammable or combustible fuels. From tractors to portable generators and passenger vehicles to heavy transport, we rely on refuelling to keep our businesses moving. Yet how do you ensure safety when dispensing and handling these Class 3 dangerous goods? Understanding the risks with flammable or combustible liquids is crucial for keeping your staff safe during the fuel transfer or dispensing process. In this post, we detail safety tips and requirements for fuel dispensing as per the Australian Standards 1940 – The storage and handling of flammable and combustible liquids.
What is Fuel Dispensing in the Workplace?
Fuel dispensing refers to the process of distributing fuel, such as petrol or diesel, from storage tanks to vehicles or equipment within a specific location. flammable or combustible liquids are dispensed into the fuel tanks of vehicles, boats or other containers.
This activity is common in various industries where vehicles and machinery require regular refuelling. Workplaces that require regular fuel dispensing operations may include manufacturing, construction, transportation, and agriculture,
Dispensing Class 3 flammable or combustible liquids is an everyday activity for many industries.
IMPORTANT: If decanting flammable liquids – or transferring them to another container, make sure staff treat the task with the utmost care. Dispensing pumps or self-closing metal taps should be used for these tasks as they will reduce the likelihood of spills, vapours and splash filling.
Key Considerations When Fuel Dispensing
The dispensing of petrol or diesel in workplace operations includes a range of risks. This is due to the complexity of the operation; that is, dispensing requires both the handling and storage of Class 3 dangerous goods, as well as the actual dispensing process.
There is a risk of ignition, spills, chemical exposure and incompatibilities with substances or materials.
We’ll look at each of these key hazards in more detail below.
How Does Fuel Ignite During the Dispensing Process?
Fuel ignition during the dispensing process can occur if certain conditions that support combustion are present. While the dispensing of fuel is generally a safe process when proper procedures are followed, there are potential ignition sources and factors that can contribute to the ignition of fuel vapours.
Fuel can ignite during the dispensing process due to:
- Static Electricity: Static electricity can build up during the fuel dispensing process, especially when fuel flows through pipes and hoses. If the accumulated static charge reaches a critical level and discharges in the presence of fuel vapours, it can ignite the fuel. To prevent this, grounding equipment and maintaining proper bonding between components can help dissipate static charges.
- Sparks or Flames: Sparks or open flames in the vicinity of the dispensing area pose a significant risk. This can include activities such as welding, cutting, or grinding. Additionally, the use of electronic devices that could generate sparks should be restricted in fuelling areas. Establishing designated fuelling zones and enforcing no-smoking policies can help minimise the risk of sparks or flames.
- Hot Surfaces: Equipment or surfaces that are hot can ignite fuel vapours. For example, the exhaust systems of vehicles or nearby machinery can reach high temperatures during operation. If fuel vapours meet these hot surfaces, it may lead to ignition. Adequate ventilation and keeping dispensing equipment away from heat sources can help mitigate this risk.
REMEMBER: You don’t have to spill much flammable liquid to create a serious fire hazard. Flammable vapours can be emitted from even a small spill, with these vapours capable of accumulating or travelling throughout work areas, creating risk due to ignition and flashback.
Fuel Leaks and Spills During Dispensing
There can be many factors that create an accidental release during the fuel dispensing process.
Things that may increase the chance of flammable liquid or combustible liquid spills include:
Faulty Equipment: Malfunctions or defects in fuel dispensing equipment can lead to leaks or spills, creating a hazardous situation.
TIP: Regular maintenance and inspection of dispensing equipment, including hoses, nozzles, and seals, are essential to ensure proper functioning and prevent fuel leaks. Make sure all equipment is fit for purpose and suitable to the type of fuel you’re using.
Improper Handling: Human error, such as overfilling fuel tanks or improperly connecting hoses, can contribute to the likelihood of fuel ignition.
TIP: Adequate training for personnel involved in fuel dispensing and strict adherence to established procedures are critical in preventing accidents.
Fuel Dispensers: These are machines or pumps designed to dispense a specific quantity of fuel into the tanks of vehicles or equipment. However, some older models may not be as safe or efficient in terms of liquid or vapour emissions.
TIP: Modern fuel dispensers often come equipped with electronic controls, digital displays, and safety features to ensure accurate fuelling and prevent spills or accidents.
Storage Tanks: Fuel is typically stored in on-site tanks, which can vary in size depending on the needs of the facility. These tanks are filled periodically by fuel delivery trucks, and the fuel is then dispensed to vehicles and equipment as needed.
Working with tanks of flammable or combustible fuels requries maintenance, consideration of the location, standard operating procedures for all equipment, the exclusion of ignition sources and highly trained staff to carry out the tasks.
Spill Kits for Containment and Clean Up
Remember, regardless of how maintained your equipment is or how trained your staff are, accidents will happen. Spill containment and clean up is an essential requirement under WHS laws, so providing the right equipment to combat a flammable liquids or combustible liquids spill is an important consideration. Spill kits can be purchased in ready-to-go packs, with refills available so you can always be ready to manage a fuel spill.
Best Practice for Fuel Dispensing and Refuelling
To mitigate the risk of fuel ignition during the dispensing process, it is crucial to follow industry best practices, adhere to safety regulations and the Australian Standard 1940, provide proper training to personnel, and regularly inspect and maintain equipment. Always dispense or transfer fuels in a well-ventilated area so that vapours don’t overpower staff or build up to create an ignition risk.
Dispensing stations provide bunded storage and oil or fuel dispensing in the one unit.
We also recommend investing in dispensing equipment that can alleviate the risks associated with fuel dispensing or liquid transfers. Storemasta offers a range of solutions to meet this need including Dispensing Stations for flammable or combustible liquids, including fuel and oil, and Outdoor Chemical Storage with Dispensing Stations for worry-free fuel dispensing.
IMPORTANT: Proper fuel dispensing practices help maintain the efficiency of operations, keep equipment running smoothly, and reduce the risk of accidents or environmental incidents. Additionally, adhering to safety guidelines and regulations is crucial to creating a secure work environment when handling flammable substances like fuel.
Requirements for Fuel Dispensing
Australian Standards 1940 – The storage and handling of flammable and combustible liquids details the requirements for Class 3 fuel dispensing in Section 7 of the standard.
These requirements assist in fire prevention with flammable liquids and combustible liquids during the fuel dispensing process. They include, but aren't limited to:
Signage
Display the following signage on or near the fuel dispenser, with letters at least 50mm high:
STOP ENGINE—NO SMOKING (or the internal symbol for ‘smoking prohibited’ instead of the text ‘no smoking’)
You may also add text placarding to say: ‘no flames, pilot lights or mobile phones’
Fixed, Portable or Mobile Ignition Sources
Any type of ignition source must be isolated from hazardous areas – including fuel dispensing areas.
While vehicles are allowed to enter or leave the area, identification and isolation of ignition sources is of the utmost importance.
Some exceptions may be made, including hearing aids or basic electronic watches.
Dispensing Equipment Requirements
Nozzles must incorporate a safety device to prevent fuel from flowing in a range of circumstances, including:
- Level of liquid in receiving vessel reaches end of nozzle
- The nozzle is dropped
- Nozzle value is tilted above horizontal from the normal operating position
The delivery hose and nozzle assembly must be able to dissipate static charge during refuelling. In addition to these requirements, the dispensing hose assembly needs to comply with Australian Standard AS 2683.
There are safety requirements for fuel dispensing equipment to reduce risk of ignition, spills and vapours.
Emergency Power Cut-Off
When dispensing fuel, make sure there is an easily accessible emergency power cut-off. This switch or circuit-breaker should be capable of shutting down all dispensing units in an emergency situation. Ideally, consider a single emergency power cut-off switch that stops all fuel from being dispensed in the entire refuelling area.
Drainage in Refuelling Areas
Any refuelling area must be graded so spilled liquids flow away from buildings but not off the site. Interceptors or oil separators must be accessible for cleaning and inspections.
Safety Measures
Due to the flammable nature of fuel, safety is a critical consideration in fuel dispensing. Safety measures may include fire prevention systems, proper grounding of equipment, emergency shut-off systems, and employee training on safe fuelling practices.
Safer Flammable Liquid Dispensing
If you’d like to continue the learning journey about flammable liquid safety, why not access our helpful eBook? This guide outlines expert tips for ensuring Class 3 safety in your operations. Get your copy of the eBook today – or contact our DG Storage Consultants for more information on solutions for fuel and oil dispensing.
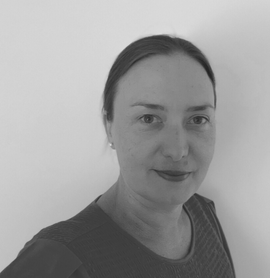
Living life by the 4 C’s of marketing – communication, coffee, compliance… and more coffee – Leisa Andersen is Storemasta’s Content Marketing Manager. When she’s not writing, you’ll find her enjoying all the good things in life, including shopping, travel and gluten free donuts.