Keeping a register of all the hazardous chemicals you use, store and carry is an essential requirement under Australia WHS legislation. But many of our clients ask us — ‘which is best’ — a hard copy (printed version) or soft copy (electronic version) of the hazardous chemical register?
In this post, we’ll identify the 4 essential areas to consider when choosing the best system for your register of hazardous chemicals. But our preference, is to have an electronic masterlist with hard copies attached to aggregate quantities and individual safety cabinets.
Hazardous Chemical Register Compliance
In Australia, failing to have a compliant register of hazardous chemicals attracts WHS penalties. Section 346 of Australian WHS Regulations requires you to keep a list of all the hazardous chemicals you keep onsite, as well as a current copy of the safety data sheet issued by the supplier of the chemicals.
There is no specific requirement in the legislation for using either an electronic or hardcopy system. However, you need to make sure that the HAZCHEM register is:
- Kept up-to-date
- Accessible to any workers using the chemicals
- Accessible to other people who are likely to be exposed or affected by the chemicals
We recommend using both a paper and digital version of your hazardous chemical register, to ensure it’s always available to staff and emergency services — regardless of their location, job duties, digital access or computer skills.
Ensuring HAZCHEM Register Efficiency
Choosing to implement both a hard copy and a soft copy of your chemical register will ensure safety and efficiency in the workplace.
To get started, we suggest you create a master-list of every chemical carried on the job site, then collating the safety data sheets. This task could be as simple as an Excel spreadsheet or as sophisticated as a centralised database.
According to the WHS Regulations, safety data sheets must be updated at least once every 5 years, so make sure there is nothing more than 5 years old in the register.
Once your master-list is created, upload it so there are digital documents available for staff.
Alternately, a hard copy register could be broken down into individual work areas, placed in purpose-built document boxes and attached to equipment, machinery and chemical safety cabinets.
Upload a copy of the chemical register to your online systems and ensure it’s updated if items on the register change.
REMEMBER: Only include substances that are classified as hazardous chemicals on your HAZCHEM register. You can learn more about hazardous chemicals via Safe Work Australia.
Accessibility to the Hazardous Chemical Register
A critical part of managing a workplace is maximising efficiencies so you don’t waste time and money duplicating documents and job tasks. The digital version of the HAZCHEM register can be incredibly efficient — because once uploaded it can be updated electronically from a central point without the need to visit individual work areas, replacing documents and throwing away paperwork. In addition, it can be quickly printed, so that a hard copy version is available to staff who don’t have access to workplace computers or devices.
One of the biggest problems with only using electronic chemical registers is that they are not always accessible. HAZCHEM registers must be immediately accessible to anyone who could possibly be affected by the chemicals or you could be in breach of the Regulations.
Hard copies should be available for staff who can’t access computers or devices.
If your register is only accessible electronically, could you encounter any of the following issues:
- Password protected workstation: would a visiting contractor or delivery driver know the password (or the steps) required to access the Register? What if the office was locked?
- Tablet: what if there is a WIFI or power outage, the tablet is LOWBAT, or left in a work vehicle?
- Smartphone: is it safe to use electronic devices in the proximity of flammable liquids or reactive chemicals? Is the screen large enough to accurately convey information during an emergency? Could a worker wearing gloves and bulky PPE be able to operate the gadget?
Having a paper register in a document box means the safety information is immediately available to anyone present in the area. Safety data sheets can be laminated or kept in individual sleeves of an SDS folder, so these important chemical documents can be accessed and read — even when staff are wearing gloves and personal protective equipment.
REMEMBER: The purpose of the HAZCHEM register is to provide critical safety and first aid information in case of an accidental spill, exposure incident, chemical burn or other injury.
HAZCHEM Registers: Hard Copy Vs Soft Copy
Your chemical register must be accurate, in good condition and readily available to all who need it. You don’t want to find yourself in an emergency only to discover that:
Hard Copies of Hazardous Chemicals Registers
- Pages are torn or crumpled.
- Paperwork has been damaged by water, dust, insects, or vermin.
- An SDS is missing because the last worker to access the register did not return the safety data sheets.
Soft Copies of Hazardous Chemicals Registers
- Safety data sheets have been scanned incorrectly and there are pages missing — or upside down.
- Documents are blurred or unreadable due to low resolution copying.
- A software update is required before you can read the PDF safety data sheet.
No matter what system you use (physical object or digital version) you will need to ensure there are supporting procedures. This will help you manage your HAZCHEM registers so they remain correct and compliant.
REMEMBER: Storemasta document boxes are tough, durable and made from corrosive-resistant materials. They keep out water, dust, pests and vermin, so your chemical register remains safe.
Chemical Safety for Workplaces
Thanks for reading our post that discusses the benefits of implementing both soft copies and hard copies of HAZCHEM registers in the workplace. As a leader in dangerous goods storage and handling solutions, Storemasta has developed chemical storage products and equipment that maximise human safety while ensuring compliance. To learn more about chemical safety and storage, why not access our eBook for the ultimate guide to DG storage or connect with our Dangerous Goods Storage Consultants who can help you achieve compliance in your own operations.
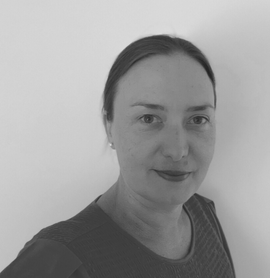
Living life by the 4 C’s of marketing – communication, coffee, compliance… and more coffee – Leisa Andersen is Storemasta’s Content Marketing Manager. When she’s not writing, you’ll find her enjoying all the good things in life, including shopping, travel and gluten free donuts.