1. Identify And Control Ignition Sources
2. Know the Flash Point of your Substance
3. Don’t Leave A Leak Or Spill Unattended
4. Choose Chemically Compatible Bunding
5. Develop First Aid & Decontamination Procedures
Need Some Help with Flammable Liquids?
Flammable and combustible liquids are found at almost every workplace. From the petrol or diesel that you put in your fleet to the acetone you use to thin your paints, flammable and combustible liquids are a class of dangerous goods that are often essential for all types of operations.
As they’re found in most working environments, staff may not be completely aware of the hazards that these chemicals present. If flammable liquids or combustible liquids aren’t stored or handled with care, they can cause a massive amount of damage to an organisation. You may be surprised to learn that our DG Storage Consultants have witnessed more than a few examples of dangerous practices involving flammable and combustible liquids, such as drums of flammables stored next to an ignition source, leaks and spills left on the ground while welding work was conducted, and containers of flammable liquids left in the sun without any type of storage.
To help you get you on the path towards improved compliance and safety, we’re offering you our 5 top tips for working safely with flammable and combustible liquids. While there are a wide range of controls that you can consider for chemical safety, these 5 tips are your starting point to safer flammable liquids storage and handling.
1. Identify And Control Ignition Sources
Let’s start right at the beginning – understanding the risk of ignition with flammable and combustible liquids. For those of you who are new to our blogs, there are 3 elements that are required to start a fire.
These are:
- Fuel – your flammable or combustible substance, for example
- Oxygen – found in the air
- Ignition Source – anything that can spark a fire or explosion
An ignition source is defined as something that can produce enough energy to ignite a fuel source – such as your flammable or combustible liquids.
There are 3 types of ignition sources:
- Flame – pilot lights, cigarettes, naked flames etc.
- Spark – powered circuits, radios, fans, static electricity etc.
- Heat – hot-cutting, welding, hot flues, exhaust pipes etc.
Ignition sources include fixed objects, such as power points or hot surfaces, as well as items which can be brought into the workplace, such as lighters or equipment that may produce a spark.
You must identify and isolate any type of ignition source from areas that handle or store a flammable or combustible liquid.
Therefore, you are required to identify and isolate all sources of ignition from your workplace – separating these by at least 3 metres from your flammable and combustible substances. Also ensure that your No Smoking, No Ignition Sources within 3m signage is displayed in all storage and handling areas to prevent people bringing ignition sources into the work area.
Identifying and isolating all ignition sources is an essential part of working safely with flammable and combustible liquids. However, equally important is ensuring that the liquids are stored below their flash point (the lowest temperature that can allow the chemical to emit sufficient flammable vapours), with the correct spill containment measures and in compliant storage. But we’ll get to those points a bit later…
EXPERT TIP: Check your safety data sheet to find out more about the flash point of your substance, as this will help you keep your liquids in a controlled and safe environment. Don’t ever assume that two similar substances have the same flash point. Always check your safety data sheets for each individual product – developing handling and storage controls accordingly.
2. Know the Flash Point of your Substance
Many people assume that the liquid itself is what catches on fire – when in fact, it’s the invisible vapours that are emitted from the chemical that can ignite in the presence of an ignition source. These vapours can travel through a workplace without staff being aware that a fire risk is being created. However, for a chemical to produce sufficient vapours to spark a fire, the product must be stored incorrectly – at a temperature equalling or exceeding its flash point.
Flammable liquids are categorised by their flash point, as per the Globally Harmonised System (GHS).
- GHS category 1 Substances with a flash point less than 23°C and initial boiling point equal or less than 35°C
- GHS category 2 Substances with a flash point less than 23°C and initial boiling point greater than 35°C
- GHS category 3 Substances with a flash point equal or greater than 23°C and equal or less than 60°C
- GHS category 4 Substances with a flash point greater than 60°C and equal or less than 93°C
Similarly, combustible liquids are also categorised by their flash point, as per below.
- Class C1 combustible liquid Substances with a closed cup flash point of greater than 60°C and no greater than 93°C (crossing over with the GHS category 4)
- Class C2 combustible liquid Substances with a flash point exceeding 93°C or a substance that has been excluded from being a flammable liquid by any of the criteria for sustaining combustion
If your liquids are handled or stored at temperatures that allow for ignition, you are creating a serious fire or explosion risk.
Therefore, understanding the flash point of your substances is an important part of ensuring safe storage and controlled fire risk. Keeping your flammable liquids and combustible liquids at a temperature below their flash point is just one of the considerations to apply when storing your chemicals.
EXPERT TIP: The Australian Standard AS 1940 outlines all the requirements that relate to all categories of flammable liquids and combustible liquids. By following the requirements of the Australian Standards, you’ll be applying the highest level of compliance and safety to your work operations.
3. Don’t Leave A Leak Or Spill Unattended
So, you accidentally drop a small amount of petrol or diesel on the ground – but you’re a bit too busy to clean it up. Sounds familiar?
When flammable and combustible liquids are leaked or spill out into the workplace, it can create a range of hazards. These include:
- Human harm – slipping on the spill or being splashed on the skin or in the eyes of staff
- Airborne contaminants – the accidental release of liquids can create an unsafe level of airborne contaminants
- Fire or explosion – if the vapours travel to an ignition source, the chemical may be ignited
- Incompatibilities – flammable and combustible liquids must be segregated from most other classes of dangerous goods, as reactions may occur between substances
Throwing a dirty rag over your spilled petrol isn’t enough to protect your team from danger. Instead, develop a spill response procedure that allows trained personnel to tend to the leak or spill when it occurs, containing the chemical, cleaning it up safely and disposing of it in accordance with local waste authority regulations.
EXPERT TIP: Due to the properties of flammable and combustible liquids, specific spill absorbents must be used to mitigate hazards. Before you purchase spill kits for your organisation, check with your distributor or supplier to ensure that the kit you are purchasing is suitable for the chemical that you’re intending to clean up.
4. Choose Chemically Compatible Bunding
As we’ve mentioned earlier in this post, the vapours emitted from leaking or spilled flammable and combustible chemicals can ignite if a source of ignition is present in the work area.
Therefore, it makes sense to tightly control the risk of leaks and spillage in your operations.
Just like the compatibility of your spill kit absorbents, it’s also essential that you choose chemical spill bunding that is suitable for your flammable or combustible liquids.
Bunding is essential for the containment of flammable liquids or combustible liquids.
Bunding can come in many forms — whether it’s floor bunding for your warehouse, spill bunds for your IBCs, bunded storage or bunded shelving. However, choosing a non-combustible material for your bunds, such as steel, is the safest and most effective spill containment option.
EXPERT TIP: Bunding is not just something that is suitable for static locations, such as flooring or storage. Leaks and spills can also occur when transferring flammable liquids or combustible liquids around a work site. Make sure that your handling equipment is bunded, to avoid leaks and spills occurring when your chemicals are being used or relocated.
5. Develop First Aid & Decontamination Procedures
In busy workplaces, accidents can – and do – happen. But when it comes to handling hazardous chemicals or dangerous goods, these accidents can have dire consequences.
Every hazardous chemical in your organisation can pose harm to your staff through the routes of exposure. This means that breathing in vapours, accidentally ingesting chemicals through poor hygiene practices, or having contact with harmful substances due to insufficient personal protective equipment or chemical controls can lead to health hazards.
If exposure does occur, you must act quickly. This means ensuring that your staff know the first aid measures that are required if chemical exposure occurs.
Your safety data sheets for each flammable liquid or combustible chemical will identify the correct first aid procedures. These may include:
- Flushing the eyes
- Washing off the skin
- Drenching contaminated clothing
- Removing footwear
- Going outside for fresh air
- Seeking medical attention
At least one person in your organisation must be trained in first aid, with a first aid station provided in a clean, organised area of your workplace. In addition to the first aid kit, you must include the safety data sheets for the hazardous substances that you have onsite.
The installation of the correct emergency decontamination equipment for your operations is also a crucial consideration when carrying any quantity of hazardous chemicals.
Emergency decontamination equipment may include a safety shower, eye wash or combination unit. You can refer to the Australian Standard AS 1940 for further information about the requirements that may apply to your site regarding the installation of emergency decontamination equipment.
Alternatively, you may choose to install your emergency decontamination equipment due to a hazard that’s been identified in your onsite chemical risk assessment.
Regardless of the equipment installed at your site, it’s important that it’s regularly activated (weekly) and maintained to ensure compliance. Make sure your staff know how to use the equipment, so that your people are protected — and your equipment is not damaged through misuse.
REMEMBER: A full risk assessment is the safest way to start controlling chemical risks. Whether you’re using a Dangerous Goods Consultant, or you have a trained risk assessment team, understanding the full range of risks present in your workplace will allow you to systematically and effectively control chemical hazards.
Need Some Help with Flammable Liquids?
While we’ve highlighted 5 simple ways to work more safely with flammable or combustible liquids, there are many more measures that you can implement to achieve compliance. If you need some help with flammable liquids safety, why not access your free eBook? Essential Considerations When Storing Flammable Liquids Indoors offers expert advice on how to control your risks, by using Storemasta’s 4-step risk management methodology. Grab your copy today and create a safer workplace.
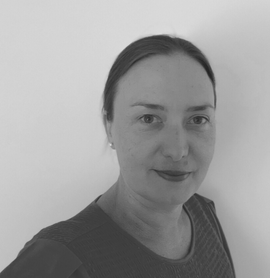
Living life by the 4 C’s of marketing – communication, coffee, compliance… and more coffee – Leisa Andersen is Storemasta’s Content Marketing Manager. When she’s not writing, you’ll find her enjoying all the good things in life, including shopping, travel and gluten free donuts.