While containing and managing chemical spills is part of your duties under WHS Regulations, the ongoing inspection and maintenance of your chemical spill kit is equally as important. Without developing (and sticking to) an inspection and maintenance schedule, your kits could prove to be ineffective when your staff go to use them. For example, have staff remembered to refill the kits after they’ve been used? Have the correct materials, that are chemically compatible, available in the kit? Has the kit been installed in a new spot — without the appropriate staff training and spill kit signage applied to the new location?
Just like any chemical control, whether it’s bunding, handling equipment, chemical cabinets or outdoor HAZCHEM stores, your spill kits are designed to help you reduce risk in the event of an accidental release. Under WHS Regulations, the ongoing inspection and maintenance of your chemical controls is also a key duty for any Australian contractor, organisation or business.
What Are The Inspection Requirements?
You may not have realised it, but there are requirements that relate to the inspection of chemical controls, such as spill kits.
WHS Regulations requires the maintenance and review of all hazardous chemical control measures.
In Section 357 of the Model Work Health and Safety Regulations (2021), it explains that:
37 Maintenance of control measures
A duty holder who implements a control measure to eliminate or minimise risks to health and safety must ensure that the control measure is, and is maintained so that it remains, effective, including by ensuring that the control measure is and remains:
(a) fit for purpose; and
(b) suitable for the nature and duration of the work; and
(c) installed, set up and used correctly.
Additionally, the reviewing of hazardous chemical controls is also detailed in the WHS Regulations with the following information:
38 Review of control measures
(1) A duty holder must review and as necessary revise control measures implemented under these Regulations so as to maintain, so far as is reasonably practicable, a work environment that is without risks to health or safety.
Just like a chemical cabinet inspection or the review of your spill containment system, your spill kits should be regularly inspected and maintained to ensure that they are fit for purpose, have the appropriate materials included, and are re-filled to meet the original requirements of the kit.
Like a free spill kit checklist?
But what’s the best way to ensure that your kits are properly inspected and maintained?
We recommend a weekly inspection and maintenance schedule for any chemical control that you have onsite. Let’s have a look at a potential inspection and maintenance checklist that can help you stay on top of your spill kit requirements.
Your Spill Kit Inspection Checklist
If you’re regularly using your spill kit, it’s a good idea to get into the habit of immediately replenishing your spill kit after it’s been used to clean up the hazardous chemical leak or spill.
If the spill kit has been used, make sure it’s immediately replenished by your staff, with the refill noted on the applicable records.
However, if you’ve been lucky enough to not have to use your kit in a while, it’s important that you maintain an inspection schedule in case staff have misappropriated items that are required for the next spill emergency.
Inspecting all controls – from your cabinets to your handling equipment – is a valuable task that can greatly improve the ongoing safety of your operations. We suggest implementing a weekly inspection schedule that can be followed by the refilling and maintenance of your kits.
Your spill kit inspection checklist should include:
- Is the kit clearly marked with the type of kit? Chemical, universal, fuel & oil, marine etc
- Is the list of contents still secured to the kit and visible? Kits come with a list of contents, usually displayed on the front of the bag or bin
- Are the contents of the kit still intact? Have you checked that your materials and equipment are still in place, with adequate quantities?
- Do any of the items show signs of ageing, soiling or disrepair? Have any items been put back in the kit instead of replaced with a new item?
IMPORTANT: While the inspection and maintenance of your spill kits is an important aspect of maintaining workplace safety, it’s also crucial to remember that the applicable staff must be trained in the appropriate spill response. If staff have changed departments or left the organisation, you must provide spill kit training to the new members of the spill response team. If any materials in the kit are changed, staff must be trained to correctly use these new items.
Refilling Your Spill Kit
If items in the kit are found to be old, worn or missing, then they must be replaced. Depending on the type of chemical spill kit that you have in your workplace, there will be a range of materials and equipment contained within.
Such items in your spill kit that may require a refill or replacement include:
- Booms for spill containment
- Absorbents including pillows, pads and/or mats
- Floor sweep granules for absorbency
- Other absorbent materials, such as socks or cloths
- Chemical containers to hold liquids from leaking packages
- Bins or large containers with lids to place liquid waste
- Waste bags for spilled chemicals and resulting effluent
- Clean-up tools including brooms, dust pans, shovel and other items
- Personal Protective Equipment (PPE) suitable for the type of chemical spilled
Once your kit has been refilled, you need to let other staff know that this task has been completed. So that everyone is on the same page about the current state of the spill kit, make sure that your records are updated to reflect the inspection and maintenance.
Create procedures that require staff to mark down the date that the spill kit has been inspected and refilled, as well as what staff were responsible for the duties. This will help you maintain your kit, and help you keep track of any items which may have gone missing.
REMEMBER: The chemical spill kit will have a list of contents displayed on the front. This will be a label or signage secured to the front of the bag or bin (whichever the kit is contained in). To make things easier for staff and supervisors, simply incorporate this list of contents into your inspection and maintenance routine, so refilling the kit is a clear, quick and simple task.
Chemical Compatibility
Under WHS Regulations, it states that a duty for workplaces that carry hazardous chemicals is to ensure that the spill containment system does not create any new hazards.
When it comes to spill clean-up kits, this means that the materials and equipment within the kit are compatible with the chemical product that may leak or spill.
Chemical compatibility is particularly important when choosing absorbent materials to contain and soak up the spill. Certain absorbent materials are not suitable with particular chemical products, due to their absorbency levels or their physical properties.
For example, oil and fuel spills require a highly absorbent material to ensure that the hydrocarbon liquid is soaked up properly. Certain absorbents can also repel water, making them suitable for use in wet locations or when staff are working on marine vessels.
Other absorbent materials, such as different types of floor sweep, must be purchased and placed in your spill kit after checking the chemical compatibility of the sweep with your particular chemical products.
Your absorbent materials should always be suitable for the chemicals that you’re carrying.
If you don’t ensure that the materials in your kit are suitable for the spill clean-up operation that is required, your staff won’t be properly equipped to manage this hazardous situation. Not only could the materials be ineffective in containing or cleaning up the spill, but some materials may also spark a reaction with incompatible substances.
Inspecting Your Spill Kit
The containment and management of chemical spills is one of the most crucial aspects of workplace health and safety. Without a properly maintained spill kit, your staff will not be able to stop the spill from becoming a hazardous situation for your organisation. Spills can easily travel through workplaces, coming into contact with ignition sources, flowing into drains, seeping into soil, and causing human harm. As part of your WHS obligations, you must keep spill kits in every area of your workplace that handles, uses, generates or stores any type or quantity of hazardous chemicals. To help you with your compliance obligations, we've created a handy Spill Kit Checklist so you can inspect and maintain your kits. Get your copy for free now and keep on top of your spill kit obligations.
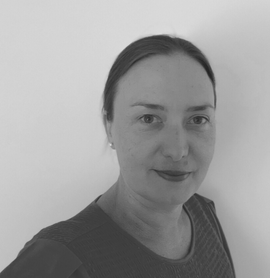
Living life by the 4 C’s of marketing – communication, coffee, compliance… and more coffee – Leisa Andersen is Storemasta’s Content Marketing Manager. When she’s not writing, you’ll find her enjoying all the good things in life, including shopping, travel and gluten free donuts.