Why Do I Need Risk Management in the Workplace?
How do you Start the Risk Management Process?
The 4 Steps of the Storemasta Risk Management Methodology
Step 1: Identify
Step 2: Assess
Step 3: Control
Step 4: Sustain
Identify, Assess and Control Your Hazards and Risks
It doesn’t matter if you own a small mechanical workshop or work for a large multi-national mining company; risk management is an essential process that is required by any business to minimise or eliminate risk. When it comes to workplaces with dangerous goods – whether that’s fuel, pesticides, cleaning chemicals or batteries – the risk management process is an important regular consideration that must be followed to ensure things remain safe and compliant.
Why Do I Need Risk Management in the Workplace?
Risk management is essential for several reasons, however, when it comes to dangerous goods – it could be the difference between a devastating incident or a safe and healthy work environment.
Risk management processes assist with:
- Protection: Risk management helps protect your team, community, workplace, assets and even reputation by identifying potential risks and implementing strategies to mitigate them.
- Cost Reduction: Effective risk management can reduce the costs associated with unexpected events or losses. By identifying and addressing risks early on, you can avoid or minimize the financial impact of potential disasters.
- Compliance: Implementing a risk management framework can assist with safety and compliance, so that you avoid potential legal or regulatory penalties.
- Decision Making: Risk management provides valuable insights that can inform decision-making processes. Understanding the potential risks associated with different options allows you to make more informed choices.
- Business Stability: By identifying and planning for potential risks, you can ensure that your business operations can continue, even in challenging circumstances. Risk management not only allows you to protect yourself from risks but ensure that any issues can be handled quickly so the affects are minimised.
Risk management is about understanding hazards and the level of risk, while taking proactive steps to protect your people, property and environment. Whether you're running a small business or a large, complex operation, incorporating risk management practices can help you reduce your risk more effectively.
“Risk management is a proactive process that helps you respond to change and facilitate continuous improvement in your business. It should be planned, systematic and cover all reasonably foreseeable hazards and associated risks.”
Code of Practice – How to Manage Work Health and Safety Risks
Safe Work Australia
How do you Start the Risk Management Process?
Starting the risk management process for dangerous goods is important – but so is continuing it. As a circular model, the risk management process for dangerous goods involves 4 key steps, as per Storemasta’s Risk Management Methodology.
The first step in this process is an important one: it’s the correct and thorough identification of the hazards in your workplace.
To do this, you’ll need:
- Experienced and trained staff who are capable of correctly identifying all dangerous goods (Classes and divisions 1-9) and their specific hazards, including incompatibilities with other classes.
- Current safety data sheets, no more than 5 years old.
- An onsite walkthrough of your site to get a full overview of the situation.
- Access to other company documents, such as sick leave and supplier invoices, to assist with your hazard identification process.
- Requirements and regulations that apply to your site, specific to your state or territory.
Your risk management team will require a firm understanding of the regulations and requirements that apply to your operations, to ensure that you’re clearly identifying anything that may be hazardous to people, property and environment. This may include WHS laws and regulations, the Australian Standards pertaining to your dangerous goods, and Codes of Practice.
When in doubt, speak with a professional who can assist with your risk management process, including qualified Dangerous Goods Consultants who have the expertise to help you achieve safety and compliance. We recommend connecting with AIDGC who can assist with your search for a professional auditor.
The 4 Steps of the Storemasta Risk Management Methodology
The steps of this risk management methodology are: identify, assess, control, sustain.
We’ll go through each of these below, to give you a general overview of the
Step 1: Identify
Hazard identification is more than doing a single walk around the job site noting the chemicals and dangerous goods used and stored. Your risk management plan should have trigger points in place, so that the identification process is an ongoing activity.
Many hazards in your workplace may be identified dangerous goods labels and safety data sheets, but you must also be aware that some chemical hazards are not immediately obvious. Others may not even be noticed until a review of your plan and a follow-up risk assessment takes place.
The Step 1: Identify section of your risk management plan will schedule these checks and balances into ongoing safety audits and risk assessment reviews to ensure continuing compliance, health and safety in your workplace.
There are a multitude of ways that you may be able to determine an unseen hazard, including the review of incident reports, sick leave records and checks of chemical inventory.
We recommend regularly reviewing:
- Safety data sheets, current regulations and requirements: to identify a hazard or a lack of compliance, it’s essential that all chemical documents and legal obligations are understood. This includes chemicals being handled and stored correctly, providing the proper training for staff, ensuring isolation and segregation rules to dangerous goods, and keeping up with any changes in regulations and law.
- Minutes from safety meetings: Reporting is an important tool in keeping hazards under control. There may have been a lack of communication, with information not actioned and changes not made.
- Supplier invoices: check supplier invoices for any unusual behaviour, as it may lead to uncovering accidental releases of chemicals or other issues which can lead to an incident.
- Incident, accident and near-miss reports: these reports may signify unsafe work procedures, ineffective PPE, inadequate training and supervision.
- Sick leave records: sick leave records may lead you to understand a link between work practices and chemical exposure or unsafe working conditions.
Step 2: Assess
Next is the assessment process, where the identification of hazards with dangerous goods becomes a detailed assessment of the level of risk.
Consider the following when working through Step 2 of the risk management process:
- What type of accidents, incidents, illnesses or otherwise dangerous events could be caused by the dangerous goods?
- How frequently could these dangerous incidents occur?
- What are the possible consequences of each dangerous incident?
- What is the total risk to your worksite?
REMEMBER: Like to learn more about the risk assessment process? Read our popular blog now to get the 7 steps of risk assessments.
Step 3: Control
A compliant risk management plan uses the Hierarchy of Control when introducing hazard control measures.
The Hierarchy of Control places control measures into groups ,and then ranks them in order of reliability and effectiveness. For every hazard you should consider at least one control measure from each group.
The steps in the Hierarchy of Control are:
- Elimination: How could you eliminate the need to use dangerous goods or hazardous substances?
- Substitution: What chemicals could you use in work operations that pose less harmful?
- Control: What controls could be put in place to reduce this risk? Options may include bunding, compliant storage, dangerous goods handling equipment, ventilation systems and other engineering controls.
- Administration: What safe operating procedures, policies or training programs could you introduce to assist with controlling the risk of dangerous goods?
- Personal Protective Equipment: Review safety data sheets and your risk assessment to determine which personal protective equipment workers must wear or use to minimise exposure.
REMEMBER: Look for better and safer ways of operating. Strive to eliminate hazards completely, before mitigating them — even if that does not happen the first time during the risk management process. Elimination is always the highest form of control when it comes to the Hierarchy of Control and your risk management process.
Step 4: Sustain
Sustaining safety and compliance is an important step in this process.
This may include scheduling preventative maintenance, site inspections, and safety audits as well as conducting follow up safety training.
You might consider establishing a WHS committee at your workplace. This committee could meet regularly to review chemical hazards. Alternatively, you may appoint a Safety Manager who is solely responsible for risk management.
What Triggers the Risk Management Process to Start Again?
Your risk management plan also needs review triggers as new chemicals are introduced into work areas, new staff are appointed, management changes, or the job site undergoes significant renovations/damage/expansion. You’ll also need to review when legislative changes occur or the Australian Standards update, which could affect your compliance.
Dangerous goods safety can only occur when you have enough regular reviews to ensure that every single hazard on site has been identified and controlled.
IMPORTANT: To sustain compliance, your dangerous goods risk management plan will need to ensure that this assessment process continues. When new hazards emerge, procedures must be in place to make sure they are quickly identified, assessed and controlled.
Identify, Assess and Control Your Hazards and Risks
To make the process of risk management a little easier, we’ve developed a handy Risk Assessment Template Pack that can help you document all the goods at your site that will be involved in your risk assessment. This pack is available for free download at any time, so you can start your own risk management strategy for your workplace.
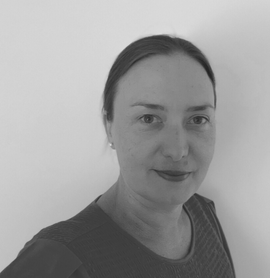
Living life by the 4 C’s of marketing – communication, coffee, compliance… and more coffee – Leisa Andersen is Storemasta’s Content Marketing Manager. When she’s not writing, you’ll find her enjoying all the good things in life, including shopping, travel and gluten free donuts.