What Areas Require A Spill Kit?
Determining Your Spill Kit Needs
What Are The Contents Of A Spill Kit?
Other Factors To Consider
Ticking Off Your Spill Response Duties
Are you searching for a spill kit checklist? You’ve come to the right place. This post is dedicated to helping you tick off your obligations when it comes to the installation and maintenance of your chemical spill kits. While hazardous spillage is a key concern for any organisation that carries dangerous goods, knowing that you’re equipped to contain and manage the accidental release of chemicals is the first step in reducing your risk. If workplaces aren’t provided with the right types of spill kits, or kits are not properly inspected or maintained, there is a real risk of the spillage causing a range of incidents from flammable liquid fires to environmental contamination and human harm. To make sure you’re meeting your chemical safety obligations, we’ve compiled a handy spill kit checklist. Use our checklist when you’re creating, adjusting or maintaining your spill kit, so you can keep track of its contents and ensure your staff are prepared for chemical leaks and spills.
What Areas Require A Spill Kit?
Regardless of the size of your organisation or the quantity of chemicals that you hold, if you have any area in your organisation that uses, handles, generates or stores hazardous chemicals – you need a spill kit.
Your chemical spill cleanup kit is your first line of defense against an accidental release of chemicals. This can occur in any area of your organisation, including:
- Loading docks
- Storage areas
- Distribution centres
- Workshops
- Manufacturing floors
- Maintenance storerooms
- Vehicle servicing and repair areas
- Outdoor work areas
- Decanting stations
- Hospitality premises
- Warehouses
- Vehicles, boats and other transport
While measures such as chemical storage containers, safety cabinets, bunded handling equipment, floor bunding and portable spill containment are effective secondary spill containment systems, the management of any leaks or spills is still a necessary obligation for Australian workplaces.
Workplaces and fleet vehicles require spill kits if there is a risk that a hazardous chemical could leak or spill.
However, knowing what kits to place in what areas can only be accurately determined by conducting an onsite spill risk assessment. We’ll talk about the importance of these assessments in the next section of our post.
Determining Your Spill Kit Needs
Before you can create and use a spill kit checklist, you need to first determine what type of spill kit (and how many) you are going to place in your particular work area.
This onsite assessment is referred to as a spill risk assessment, which is an essential process involving the identifcation, assessment and control of any potential spill hazards in your business.
An onsite spill risk assessment will help you determine your spill containment and clean-up requirements.
Some basic factors that can determine your spill kit needs will include:
- The requirements of the relevant Australian Standard – the Standard that applies to your particular type of chemical class may include specific details about the materials required in your kit.
- Type of chemical product that you’re carrying – referring to the Safety Data Sheet of your chemical products is a crucial factor that determines the type of materials needed in your kit.
- Quantity of chemical – leaks and spills come in all sizes, so the quantity of chemical that could be accidentally released will determine the quantity of absorbent materials and decontaminating substances that you’ll need.
- Work areas that could be affected – your spill risk assessment must identify which areas of the workplace could be potentially affected in the event of a spill.
- Work practices that could cause a leak or spill – to ensure that you’re equipped to handle spillage, your risk assessment will need to look at all work practices (handling, storage, transfer) that could contribute to a possible spill.
Every chemical product in your organisation will need to have a spill kit that is suitable for that chemical class. When conducting your risk assessment, make sure your team are studying the SDS of each chemical product, so that the appropriate precautions can be taken.
IMPORTANT: WHS Regulations states that your spill containment system should not bring together materials that could create a further hazard. This includes materials that may be found in your spill kit, such as absorbents, that may not be suitable for use with particular chemical products.
What Are The Contents Of A Spill Kit?
While there are several types of spill kits on the market — such as universal kits, chemical spill clean-up kits, marine spill kits, and oil and fuel kits — they all share some common materials and equipment.
There are many types of spill kits to suit the type and quantity of chemical that you have onsite.
The basic contents of a spill kit should be determined by your risk assessment, but there are some general guidelines as to what is required in a kit.
The contents of a spill clean-up kit may include:
- Containment materials – this includes materials that will prevent the spread of chemicals further into the workplace and surrounding areas. Contents may include booms, mini booms and other absorbent materials that will prevent spillage from travelling.
- Absorbents – there are many options for absorbents, including mats, wipes, pillows and pads. Each type of absorbent is useful for a particular application, such as slowing down a chemical leak from faulty equipment or machinery (pillows) or wiping down surfaces to remove the chemical liquid and any remaining residue (absorbent wipes).
- Floor sweep – another type of absorbent, the floor sweep is a bag of granulated absorbents that is designed to soak up larger amounts of chemicals spilled on the floor. There are many different types of floor sweep, so check with the supplier or manufacturer about the chemical compatibility of the product.
- Clean-up equipment – to remove the spillage from the site, a range of clean-up equipment may be required. This could include a mixed bag of items, such as shovels, brooms and brushes.
- Chemical waste bags – the safe removal of chemical waste, and any resulting effluent, is a requirement under WHS Regulations. Therefore, waste bags and ties are an essential part of your spill kit content.
- Containers – if chemical packages have split, there may be an opportunity to salvage leaking chemicals by placing them in a new container. If you are containing leaking packages, make sure the new container is clearly labelled so any chemical hazards are immediately identifiable to staff. Split or damaged packages should be disposed of in a compliant manner.
- Decontamination solutions – when cleaning up the leak or spill, you’ll also need to decontaminate the site. Refer to the SDS of your chemical products to determine the correct decontamination fluids for the job.
- Neutralisers – some chemical products may require a neutraliser during the clean-up process. Neutralisers are generally used when cleaning up acids and other dangerous chemicals. Again, refer to the SDS to determine your need for neutralising agents.
- Wheelie bin – when dealing with larger volumes of spilled chemicals, a wheelie bin is a handy tool. Use the bin to bring the spill kit quickly to the site, then fill it with soiled items and transport the closed bin to the appropriate chemical waste disposal area.
- Gloves and PPE – before any containment or clean-up can occur, staff should be dressed in the appropriate PPE. Most spill kits include chemically compatible gloves (such as nitrile gloves) to assist workers with the handling of soiled containment and absorbent materials.
- Label and instructions – spill kits must be clearly labelled with the type of spill kit that it is, its capacity, as well as the list of contents in the kit. There should also be instructions included in the kit. While these basic instructions should always be backed up with formal spill kit training, it’s important to keep the instructions attached to your spill kit at all times.
Other Factors To Consider
While you may have compiled the ideal spill kit for your work area, they must be maintained to be compliant and effective.
Need a spill kit checklist?
In addition to your contents checklist, you should also inspect and tick off the following queries for each and every spill kit that you have onsite.
Consider the following:
- Do the contents of the spill kit match the label?
- Are the instructions still current and applicable for the kit?
- Is the equipment, including the wheelie bin, PPE and clean-up tools, in good working order?
- Are there sufficient quantities of materials (containment, absorbents, waste bags etc) within the kit?
- Is there any chemical residue or smell on the materials or equipment?
- Are all materials within the spill kit still compatible with the chemical product?
IMPORTANT: When ticking off the items in your chemical spill clean-up kit, don’t forget to make sure that it’s placed in a highly visible and accessible location. Staff should be informed about the location of the spill kit, so no valuable time is wasted in the event of a leak or spill.
Ticking Off Your Spill Response Duties
While there may be many factors to consider when containing and cleaning up a chemical spill, knowing that your spill kits are complete, chemically compatible and in good working order, is a good first step towards reducing your risk. If you’d like to simplify the spill kit inspection and maintenance process, why not download a copy of our free checklist? Our checklist is a straightforward and simple to use tool that will help you keep your spill kits in good working order. Get your copy now by clicking on the image below.
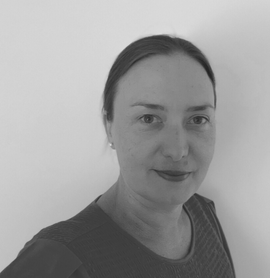
Living life by the 4 C’s of marketing – communication, coffee, compliance… and more coffee – Leisa Andersen is Storemasta’s Content Marketing Manager. When she’s not writing, you’ll find her enjoying all the good things in life, including shopping, travel and gluten free donuts.