In our blog posts, we often discuss the human and environmental costs associated with chemical spills. However, this time, we’ll be looking at the financial cost of a chemical spill – something that can vary wildly depending on the type and quantity of chemical spilled, and the environment and circumstances in which it is released. Using some hypotheticals, we’ll give you a general idea of how quickly financial costs can add up when dealing with leaks and spillage in the workplace. We hope these hypothetical situations can give you a better understanding of how important it is to implement a successful spill containment system and bunding in your own organisation.
Costs Associated with Chemical Spillage
Penalties for non-compliance, clean up costs, labor, damaged vehicles, equipment rendered useless and lost chemicals. When it comes to adding up the costs of hazardous chemical spillage, the toll can be great.
While major chemical spills such an oil spill at sea or tanker overturning on the highway can come with massive financial, human and environmental costs, even smaller hazardous chemical spills can affect the operational costs of a business.
What Financial Costs May Occur with a Hazardous Chemical Spill?
Consider some of the financial complications that are a result of a hazardous chemical spill:
- Loss of chemical inventory
- Wages for staff to physically clean up the spill
- Chemical waste removal costs
- Production halted while spill is taken care of
- Equipment damaged by the spill having to be repaired or replaced
- Products affected by the spillage, leaving them unable to be sold
- Decontamination and cleaning of personal protective equipment
- Replacement of absorbents and other spill kit essentials
- Higher premiums for insurance if damage has occurred
- Damage to the reputation of your business if the spill affects the local community or environment
Hazards caused by the chemical type (or the circumstances in which the chemical is released) can also havily impact the bottom line or organisations that hold Hazchem substances.
Consider some of these hazards and how the costs would stack up for your business:
- Fire or explosion when flammable liquids ignite
- Chemical reactions when incompatible substances make contact
- Corrosion to vehicles, property and other materials at the worksite
- Specialised clean ups for toxic chemicals that enter the environment
- Pay outs to staff who were affected by the spill, hazardous vapours or the hazard that the spill created
In addition to all of these costs, there are also a wide range of penalties that businesses may face from their regulatory body. Some costs for non-compliance (as per the Model WHS Regulations) may include the following.
WHS Chemical Spill Incident |
Maximum penalty in the case of an individual |
Maximum penalty in the case of a body corporate |
Failure to provide spill containment system |
$6 000 |
$30 000 |
Failure to prevent hazards caused by bringing together of different incompatible substances |
$6 000 |
$30 000 |
Failure to cleanup and dispose of hazardous chemical spill and resulting effluent |
$6 000 |
$30 000 |
Examples of Estimated Financial Costs
While there are some obvious costs associated with spills (ie the cost of spilled chemicals, spill kits, lost production hours), there are other costs that you may not anticipate such as damage to property and the environment, increased insurances and the very serious risk of a chemical hazard affecting the reputation of your business and the confidence of shareholders.
To give you a general idea of the costs that may be associated with hazardous chemical spillage at your site, we’ve created some hypothetical scenarios. Using rough estimates, we've tried to demonstrate some of the immediate and long-term costs that may be placed upon your business if you don’t effectively prevent leaks and spills from occurring.
Your obligations, under WHS law in your state or territory, include providing a containment system for spills, preventing incompatible substances from causing hazards and cleaning up the waste.
Corrosive Chemical Spills
Corrosive chemicals have the ability to corrode a variety of materials from human flesh to metal and stone. Consider a situation where a large container filled with a highly corrosive substance was left on a work bench, surrounded by expensive tools, equipment and technology. A staff member unknowingly knocked over the container, and the unsecured cap caused the contents of the container to flow out across the work bench and surrounding area.
Possible costs could include:
- Destruction of tools and property - $100,000s
- Lost production time - $10,000s
- Staff hours for clean up - $1,000s
-
Replenishment of spill kits - $100s
- Increased insurance - $1,000s
- Chemical replacement - $100s
Toxic Chemical Spills
Toxic chemicals, while common in workplaces, can pollute the environment, as well as harm humans or animals that come in contact with the hazardous substance. Imagine a workplace scenario where an old and damaged IBC full of toxic chemicals split overnight. The chemicals flooded out of the container and travelled into the soil, as well as down drains into waterways.
Possible costs could include:
- Fines for non-compliance - $10,000s
- EPA fines river/creek pollution - $10,000s
- Lost production time - $10,000s
- Staff hours for clean up -$10,000s
- Soil removal, replacement, testing - $10,000s
- Replenishment of kits - $1,000s
- Chemical replacement - $1,000s
Flammable Liquid Spills
In this scenario, imagine a small drum of flammable liquids was spilled when a forklift knocked over the unbunded drum. The spill quickly reached an ignition source, and a small fire engulfed some combustibles lying around the jobsite — before it was extinguished by staff and the local fire service. Luckily, no staff were injured in the fire. However, some damage to the exterior of the building occurred.
Possible costs could include:
- Fire damage - $10,000s
- Lost production time - $10,000s
- Staff hours for clean up - $1,000s
- Replenishment of kits - $1,000s
- Call out for fire dept/emergency responders - $1,000s
- Chemical replacement - $100s
Prevention of Hazardous Spillage
It’s far more economical to prevent a chemical spill than deal with the consequences of an accidental release. In addition to the terrible costs associated with harm to human health, pollution of waterways or soil, damage to wildlife or farm animals, there are a far-reaching range of financial costs associated with hazardous spills.
Bunding and bunded storage are simple ways to prevent hazardous chemical spillage from affecting your workplace and surrounds.
If you’re carrying any type of hazardous substance, it’s important that you make sure you invest in the prevention and management of chemical spills to safeguard your future financial interests.
Some cost-effective options that greatly reduce the risk of spillage include:
Bunded storage – compliant indoor cabinets or outdoor storage features liquid-tight spill containment, so leaks and spills can be captured and easily cleaned out.
- Safety Cabinets $1,000 - $6,000, Outdoor Stores $2,000 - $30,000 approx. costs
- $500 - $4000 approx. costs
- $500 - $5,000 approx. costs
- $1,000 - $4,000 approx. cost
- $100 - $500 approx. costs
- $100 - $500 approx. costs
Controlling Risks and Costs of Hazardous Spillage
While these are just 3 minor spill incidents that may occur in a real-life setting, there are countless ways that spills can occur in a workplace. Whether you’re carrying a bottle of toxic chemicals or scores of flammable liquid IBCs, it’s essential to conduct a risk assessment at your site to ensure that all potential hazards are identified and controlled. To find out more about the prevention of hazardous spillage in your organisation, you can access our FREE guide. We’ll lead you through the steps that you can take to implement secondary containment solutions, such as bunded safety cabinets, floor bunding, and bunded handling equipment, to prevent the costs associated with leaks and spillage. The implementation of spill bunding and bunded storage is a worthwhile investment that will pay dividends long into the future.
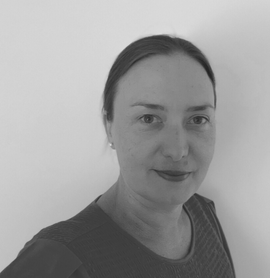
Living life by the 4 C’s of marketing – communication, coffee, compliance… and more coffee – Leisa Andersen is Storemasta’s Content Marketing Manager. When she’s not writing, you’ll find her enjoying all the good things in life, including shopping, travel and gluten free donuts.