Why Do You Need Chemical Bunding?
What are the Legal Regulations for Bunding?
What Hazardous Chemicals Do You Have Onsite?
Common Safety Issues with Chemical Bunding
Chemical Bunding Requirements
The term ‘chemical bunding’ refers to bund products which are used to create an effective spill containment solution. If you’re focused on creating a safer workplace, implementing the right chemical bunding measures can be a key element in your risk minimisation strategy. Read our blog to find out more about spill containment and the regulations for chemical bunding in Australia.
Why Do You Need Chemical Bunding?
Bunding is a necessary part of your spill containment measures, as it provides an impervious barrier that workplace chemicals will not be able to pass through. Chemical bunding may also be referred to as bunding, spill bunding or spill containment bunding.
If a spill or leak does occur onsite, bunding is designed to stop the flow of chemicals before they pose a more serious risk to your workplace. This safety measure is designed to minimise the potential for the hazards that are associated with chemicals in the workplace including harm to human health, destruction of property and environmental contamination and pollution.
Bunds are designed to:
- Contain the leak or spill
- Minimise the risk of fire or explosion
- Aid the recovery and clean-up of chemicals
An impervious, chemical resistant, and fire-resistant spill bund
What are the Legal Regulations for Bunding?
In Australia, your bunding requirements are determined by WHS Regulations. The regulation outlines the requirements for the containment and management of spills.
It reads:
Subdivision 2 Spills and damage
357 Containing and managing spills
A person conducting a business or undertaking at a workplace must ensure, so far as is reasonably practicable, that where there is a risk from a spill or leak of a hazardous chemical in a solid or liquid form, provision is made in each part of the workplace where the hazardous chemical is used, handled, generated or stored for a spill containment system that contains within the workplace any part of the hazardous chemical that spills or leaks, and any resulting effluent.
According to the regulations, provision must be made in workplaces to ensure a spill containment system in areas where the chemical is “used, handled, generated or stored”. This means that any area in your workplace that has hazardous chemicals — from your storage areas to your decanting areas — must have bunding and spill containment measures in place.
Australian Standards
To comply with WHS Regulations, you must meet the legal requirements for bunding and spill containment in any area that has hazardous chemicals.
As the WHS Regulations are rather broad, some organisations find it hard to interpret them or put their requirements into specific actions. If you have this problem, you might find it easier to refer to the Australian Standards. Standards are documents that set out specifications, procedures and guidelines that aim to ensure products, services, and systems are safe, consistent, and reliable. While the standards are not law, the regulators accept their recommendations as a means of complying with the regulation. The Australian Standards are more specific — and therefore easier to implement in the workplace.
What Hazardous Chemicals Do You Have Onsite?
One of the first steps to determining the bunding requirements for your organisation is by studying the standard which refers to the type of dangerous goods or hazardous substance that you have onsite.
These standards include:
- Class 3 Flammable Liquids: AS 1940 – The storage and handling of flammable and combustible liquids
- Class 4 Flammable Solids: AS/NZS 5026 – The storage and handling of class 4 dangerous goods
- Class 5.1 Oxidizing Agent: AS 4326– The storage and handling of oxidizing agents
- Class 5.2 Organic Peroxide: AS 2714 – The storage and handling of organic peroxides
- Class 6 Toxic Substances: AS/NZS 4452 – The storage and handling of toxic substances
- Class 8 Corrosives: AS 3780 – The storage and handling of corrosive substances
- Class 9 Miscellaneous Dangerous Goods: AS/NZS 4681 - The storage and handling of Class 9 (Miscellaneous Dangerous Goods) dangerous goods and articles
To make the process a little simpler for you, we have provided a brief summary of the chemical bunding requirements for each dangerous goods class, including bund design and construction, capacity and any maintenance requirements.
However, as these summaries are not complete, we encourage you to refer to the appropriate standard for the type of dangerous goods that you are storing at your workplace.
You may also organise an onsite risk assessment with a dangerous goods specialist who can properly determine your chemical bunding requirements.
Class 3 Flammable Liquids AS 1940
4.4.3 Spillage containment Provision shall be made to contain any leaks or spillages, and to prevent them from contaminating the surrounding soil or entering any watercourse or water drainage system.
The standard details a range of requirements including the construction of the spill containment compound, which must be sufficiently impervious to retain and recover spillage, as well as chemically resistant and fire resistant.
The capacity shall be at least 100% of the largest package, plus 25% of the aggregate capacity (up to 10 000 L), together with 10% of the capacity (10 000 L – 100 000 L) and 5% (above 100 000 L). This capacity shall be increased by volume equal to the output of auto or manual fire suppression systems over a 20-minute period. Drainage should be capable of carrying this output.
Any rainwater or fire water drainage that flows to outside of the compound shall be via a suitable interceptor or separator, or after sampling and testing of water.
If there is more than one storage connected to the common compound, drainage tank or pit, the capacity of the compound shall be equal to the largest compound for any one store, plus 20% of the capacity of the other stores.
Class 4 Flammable Solids: AS/NZS 5026
5.6 BUNDS AND COMPOUNDS
5.6.1 Spillage containment
Provision shall be made to contain any leakage or spillage within the premises, and to prevent them from contaminating surrounding soil or from entering any drainage system (other than any intended for their drainage and collection).
The Australian capacity for Class 4 dangerous goods that are liquid, contain liquid or are molten is at least 100% of PG 1 and PG II, and 25% of PG III - the capacity shall be at least the capacity of largest container. The fire water capacity over a 20-minute period must be factored into the design.
The spill compound shall comply with requirements including being sufficiently impervious to retain and recover spillage. The bund should withstand the hydrostatic head when full. It should not be higher than 1.5 m above interior grade unless means for safe and rapid entry and exit are provided.
Class 5.1 Oxidizing Agent AS 4326
7.5 BUNDS AND COMPOUNDS
7.5.1 General
Except for break tanks that have been provided with provision for spill containment, all tanks for liquid oxidizing agents shall be provided with a compound complying with the requirements of this Clause. Where it is not possible to provide a compound, the surface around and under the tank shall be graded to a catchment compound elsewhere within the premises. The requirements of this Clause shall also apply to any such remote compound.
The requirements in the standard include the capacity for oxidizing agents of PG 1 to be no less than 100% of the total storage capacity of all tanks within the compound; or PG II or III oxidizing agents to be no less than 100% of the largest tank within the compound.
Materials of construction shall be substantially resistant to chemical attack of the oxidizing agent they contain and must be sufficiently impervious to retain spillage. The bund must retain structural integrity in the event of a fire. Bunds should also be able to withstand the hydrostatic pressure expected to be exerted when bunds are full.
Class 5.2 Organic Peroxide AS 2714
Section 4 .7.4 Spillage control states that each indoor storage room/compartment shall hold at least 25% of the stored liquid or capacity of largest container, whichever is greater. Or, it must be provided with an enclosed drain that is fitted with a flame trap and lead to a bunded compound or impervious sump.
Class 6 Toxic Substances: AS/NZS 4452
4.4 GENERAL REQUIREMENTS FOR PACKAGE STORES
4.4.1 Requirements for stores other than indoor storage cabinets Package stores for toxic substances, other than indoor storage cabinets, shall comply with the following general requirements, as appropriate:
The standard lists extensive requirements including the store being located on a floor with immediate access for emergency personnel; a minimum of two means of access to stores with floor area over 25m2.
The stores must be designed, constructed and operated in a way that allows for housekeeping requirements to be effectively carried out including washing down of the floor.
The stores' walls, roof sheeting and main structural members must be constructed from non-combustible materials which are resistant to attack by the toxic substances stored. Capacity of compound must be 100% of aggregate volume of liquids kept for PG 1 liquids; 25% of aggregate volume of liquids kept for PG II and III.
Class 8 Corrosives AS 3780
The section 4.4 GENERAL REQUIREMENTS FOR PACKAGE STORES offers an extensive list of requirements that includes: materials must be corrosion resistant to the type of store and the materials to be kept, or they must be lined with corrosion-resistant materials. Areas used for decanting require sealed floors which are drained to a suitable compound. Packages must be kept in a way where they can't fall and cause spillage outside the compound.
The net capacity of the compound must be not less than (whichever is the greater) of 25% of aggregate volume of liquids or capacity of largest container — but must not exceed 5000 L where only packages are kept.
Racks or shelves must be designed and constructed to prevent the accumulation or pooling of liquid, except where they're designed as spill trays or compounds.
A corrosive resistant polyethylene bund to contain corrosive substances.
Class 9 Miscellaneous Dangerous Goods AS/NZS 4681
The standard outlines in section 3.3 DESIGN AND CONSTRUCTION REQUIREMENTS FOR PACKAGE STORES:
3.3.4 Spillage containment for package stores Where liquids are to be stored, spillage containment shall be provided. This may be achieved by using a bund or by having a means of diverting a spill into a compound within the premises, e.g. by installing spoon drains or sloping floors.
The spillage containment construction requirements include the provision for materials that are resistant to attack by the materials being stored. The compound shall also be impervious to the stored materials.
The capacity of the compound shall be at least 100% of the volume of the largest package, plus 10% of the total storage capacity (up to 5000 L). Capacity shall be increased to include fire water from sprinklers over a 20-minute period.
Common Safety Issues with Chemical Bunding
While adhering to the WHS Regulations and the requirements of the relevant Australian Standard is importance for safety and compliance, there are also some other key considerations when implementing bunding into your workplace.
To assist with your spill containment strategy, we’ve compiled some common safety concerns that affect many workplaces carrying liquid chemicals. By avoiding these safety issues, you can better select, use and maintain a chemical bund that is suitable for your specific chemicals and operational needs.
Issue #1: Chemical Incompatibility
When you’re working with hazardous substances such as corrosives, flammables, toxic substances or organic peroxides, your spill containment and management system will be determined by the class of dangerous goods that you are carrying.
This is because each class of dangerous goods has its own set of physical and chemical properties —and these may react with certain substances, chemicals or materials. Because of chemical compatibility issues, the dangerous goods class of your chemicals will determine the materials that your bunding — and other risk control measures — are constructed from.
For example, we recommend the use of steel bunds with flammable and combustible liquids, while corrosives and other chemicals can be used with poly bunds.
Issue #2: Unprotected Work Areas
According to the Model Work Health and Safety Regulations, wherever there is a risk from a leak or spill of a hazardous chemical, an organisation must provide a spill containment system.
This means that spill containment issues need to address in each part of the workplace where the hazardous chemical is:
- Used
- Handled
- Generated
- Stored
For example, you may have bunded storage and floor bunding installed in your workshop, but if you’re working with hazardous chemicals and moving them between other work areas – then you must also consider the spill bunding requirements of those workspaces.
Chemical bunding can be used in all indoor and outdoor areas of the workplace where hazardous chemicals are present.
These may include:
- Loading docks or delivery/receiving areas
- All areas where chemical decanting occurs
- Storage areas for hazardous chemicals
- Manufacturing premises
- Waste management areas
- Any work area where chemicals are transferred to, from or through
Conducting a detailed risk assessment of your workplace will help you identify all the areas where you are required to provide bunding and spill containment.
REMEMBER: If you’re using, handling, generating or storing hazardous chemicals, WHS Regulations states that you have a legal obligation to provide a compliant spill containment system.
Issue #3: Incorrect Bund Capacity
Are you confident that your chemical bunding complies with the capacities set out in the Australian Standards? It’s not just as simple as allowing for 110% capacity of your largest container (although you’ll often read that online).
To properly determine the bunding capacity for your workplace, we recommend an onsite risk assessment. However, the Australian Standard that relates to the chemicals that you’re carrying does detail the exact capacity requirements that you need to adhere to.
If bunding is inadequate for the chemicals that you're storing, overflow and hazardous spillage can occur.
Issue #4: Inadequate Maintenance of Bunds
Spill containment systems are designed to provide a short-term solution to chemical spills and leaks. But what they’re not designed to do is hold spilt substances for longer periods of time. One of the most important things to remember after you’ve implemented spill bunding at your workplace is that you must regularly inspect, clean and maintain it.
If you have bunded storage with a spill sump, you must make sure than any chemicals in the sump are immediately cleared and discarded in a safe way. Spilt chemicals pose an array of risks due to the hazardous vapours that they emit. If they aren’t dealt with promptly by your team, the chemicals could cause serious hazards such as human harm, fire or explosion.
The effectiveness of the sump will also be compromised, as the sump is specifically designed to hold a certain capacity of spilt chemicals. This sump capacity does not include the volume of spilt chemicals that are already sitting in the sump.
It’s important to maintain a regular schedule of inspections, maintenance and housekeeping to ensure your spill containment measures stay compliant. Make sure that any chemical leaks and spills are cleaned up straight away, so your bunding can continue to provide a safe and compliant spill containment solution.
Chemical Bunding Requirements
As we’ve outlined in this blog, chemical bunding is a key component of your spill containment strategy. To reach full compliance at your workplace, it is recommended that you study the Australian Standard that applies to the spillage containment requirements for the specific class of dangerous goods that you have onsite. To assist with your bunding selection, we’ve created an eBook about spill protection. This eBook will guide you through the relevant regulations, so you can contain your dangerous goods and hazardous chemicals in suitable chemical bunding.
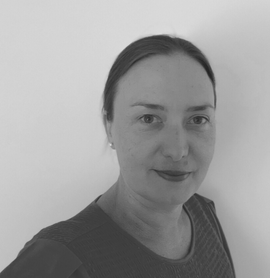
Living life by the 4 C’s of marketing – communication, coffee, compliance… and more coffee – Leisa Andersen is Storemasta’s Content Marketing Manager. When she’s not writing, you’ll find her enjoying all the good things in life, including shopping, travel and gluten free donuts.