Achieving Chemical Compliance in Your Workplace
Storage Compliance
Conduct Risk Assessments for Chemical Safety
Schedule WHS Compliance Audits
Implement a Maintenance Schedule
Free Chemical Compliance Guide
You’ve been through the whole risk management process and your hazardous chemical storage areas are all clean and in order. But before you breathe a sigh of relief, don’t forget that you’ll need to periodically review the whole system to sustain compliance. Risk management is not a set-and-forget approach to chemical safety and this blog post is all about the follow-up. Making sure you have a clear review process that includes scheduled compliance audits, regular maintenance and follow-up risk assessments is how you can sustain compliance with hazardous chemical storage regulations.
Achieving Chemical Compliance in Your Workplace
First let’s quickly look at the steps required in getting your worksite compliant with chemical safety and storage regulations.
The Storemasta methodology for chemical risk management consists of 4 clear steps to compliance:
- STEP 1: Identify all the chemical hazards
- STEP 2: Assess the dangers associated with each chemical hazard. Work out which ones have the greatest risk to health and safety — and are most likely to occur.
- STEP 3: Control the risks by either eliminating the chemical hazard completely or redesigning the workplace/operating procedures to reduce the level of harm.
- STEP 4: Sustain compliance and chemical safety by scheduling WHS audits, regular maintenance, and follow-up risk assessments.
Each step in the process is essential — and dependent on the other three.
For example, you can’t control a chemical hazard (step 3) if you don’t identify the chemical correctly (step 1), at the same time conducting a risk assessment (step 2) without introducing any control measures (step 3) is a waste of time. Once you’ve achieved compliance, step 4 is essential to sustain a safe workplace. And that’s what we are going to talk about now.
Storage Compliance
Storage compliance depends on the chemicals at your site, as well as their quantities, storage facilities, work tasks and other unique factors.
To adhere to WHS Regulations and the Australian Standards, we recommend developing inspection checklists to ensure your stores have been selected, installed, stacked, used, cleaned and maintained correctly. By regularly inspecting your chemical storage facilities, you can actively reduce the likelihood and impact of chemical hazards.
While there are many specific factors that will apply to your chemical stores, some common examples of storage compliance include ensuring that:
- Chemical leaks and spills are properly contained
- Any spillage is identified and cleaned up promptly
- Only the correct dangerous goods are stored in the appropriate safety cabinet or outdoor chemical store
- Hazards such as ignition sources or incompatible substances are separated from stores
- The chemical storage equipment is in good condition and fit-for-purpose
- Ventilation, if required, is operating effectively
- There are current safety data sheets near to the store for staff and emergency reference
- Signage is correct, visible and in tact
- Chemical containers are wiped clean after use and stacked or loaded safely within the store
- Staff have been trained to safely use the chemicals, as well as the chemical storage equipment
- Access controls (ie lockable safety cabinets or secure outdoor areas) are working to provide necessary security, if applicable
Your chemical safety cabinet or outdoor store must be used and maintained correctly to sustain compliance.
Conduct Risk Assessments for Chemical Safety
Now that you’ve been through the full risk management process you need to regularly review each of your control measures to make sure they’re working.
Following this Storemasta method, make sure you conduct a follow up risk assessment to identify:
- Any new chemicals hazards introduced by the control measures
- Any hazards that were overlooked in the initial risk assessment
- If there has been an increase or decrease in chemical safety incidents
- Whether staff are following safety procedures and using personal protective equipment correctly
Additionally, each time significant changes are introduced to the workplace you’ll need to conduct a risk assessment. Changes might include heavy staff turnover, new management, emerging technologies that introduce new work methods, chemicals that become obsolete or illegal, or suppliers that go out of business.
Schedule WHS Compliance Audits
A WHS compliance audit is an analysis of the workplace to assesses each chemical storage area for compliance to current WHS legislation, as well as relevant Codes of Practice and Australian Standards. A WHS compliance audit should be conducted regularly.
A WHS compliance audit covers:
- Staff knowledge and training (toolbox talks, staff meetings, formal training)
- Physical equipment (personal protective equipment, emergency equipment, plant and machinery)
- Work areas (signage, chemical storage areas, ventilation systems)
- Administrative controls (work methods, emergency procedures)]
- Documentation (hazardous chemical register, hazardous chemicals manifest, policies, safety manuals)
- Workplace accidents, incidents and near misses
- Licences, permits and certifications
WHS compliance audits are best conducted by external consultants who offer objective insights into the workplace. After physically conducting the audit, they will prepare a detailed report including the corrective actions that need to be taken to ensure compliance.
Implement a Maintenance Schedule
Finally, you should ensure that operational plant and safety equipment is scheduled for regular inspection and maintenance.
This includes:
- Cleaning, testing, and replacing personal protective equipment
- Servicing firefighting equipment
- Testing and calibrating alarms
- Inspecting chemical storage containers and safety cabinets
- Routine maintenance and cleaning of operational plant and machinery
- Testing air quality and toxicity levels to adhere to the workplace exposure standards
- Inspecting and activating emergency decontamination equipment
- Renewing first aid kits
Scheduled maintenance contributes to a safer workplace, minimises production downtime, and decreases breakdowns and emergencies. And in your chemical storage areas you’ll have the opportunity to investigate any leakages or spills, damage to containers and security breaches.
Free Chemical Compliance Guide
To achieve and sustain regulatory compliance, you’ll need a solid Chemical Management Program (CMP) that includes a system for identifying and controlling chemical hazards. To get started, we recommend accessing a copy of the eBook How to manage the risk of Hazardous Chemicals in the workplace. This free resource details the 4 essential steps of chemical compliance, with practical tools and templates to help you along. Download your copy now to learn how to sustain compliance with your hazardous chemical stores.
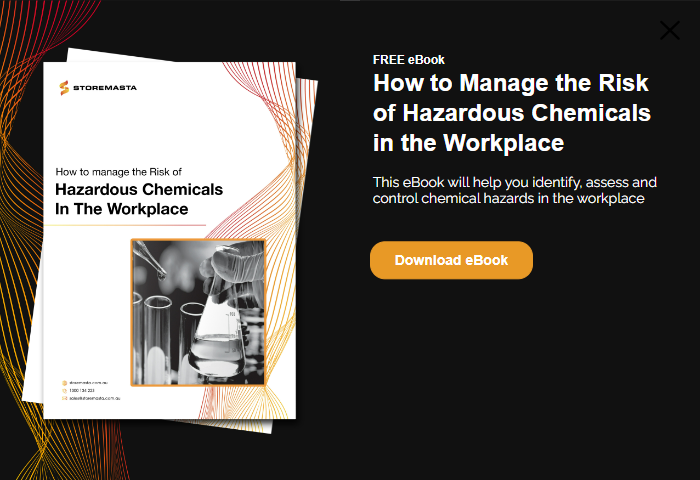
Joining the team as a Dangerous Goods Storage Consultant, Melissa Hampton became Storemasta's Marketing Manager in late 2021. With extensive knowledge and experience in chemical compliance, Melissa is responsible for leading the Marketing team and helping shape their marketing strategy. In her spare time, you can find Melissa hiking, swimming and enjoying the great outdoors in beautiful north-west Tasmania.