What are Class 2 Gases?
How are Gases Used?
What is Chemical Segregation?
What are the Segregation Rules for Gases?
Rules of Gas Segregation
Dedicated Gas Storage
Isolate from Ignition Sources
Empty Cylinders
Gas Storage and Safety
When handling and storing dangerous goods, the rules of chemical segregation must always apply. This is the process of identifying incompatible goods, and those that react dangerously, and separating these from goods to ensure health and safety onsite.
While gases – such as LPG, acetylene, chlorine, helium and nitrogen, are all recognised as Class 2 Gases, they fall into divisions which present specific hazards – and require strict segregation to maintain safety.
This post offers information to help you store and segregation your dangerous gases by practicing compliant storage.
What are Class 2 Gases?
Gases are a range of dangerous goods that are recognised as Class 2 Gases by the Australian Dangerous Goods Code.
Each division of gases is outlined below:
Class 2.1 - Flammable Gases
These gases can ignite and burn easily.
Examples of flammable gases include LPG, propane, butane, and acetylene.
LPG is a commonly found flammable gas that is used in many inudstries for heating, cooking, fuel and other applications.
Class 2.2 - Non-Flammable, Non-Toxic Gases
Non-flammable, non-toxic gases do not support combustion. They also do not pose threat with toxic poisoning. However, this does not mean they do not have their own specific hazards such as asphyxiation from oxygen displacement, cold burns and reactivity with other substances.
Some Class 2.2 are considered Oxidising Gases and are assigned the division Clas 2.2/5.1.
Examples of non-flammable, non-toxic gases include nitrogen, oxygen and carbon dioxide.
Oxygen is a type of non-flammable, non-toxic gas that's often used for healthcare purposes.
Class 2.3 - Toxic Gases
Toxic gases, as the name suggests, are poisonous dangerous goods. These gases can cause serious health effects or death if inhaled.
Examples of toxic gases include chlorine, ammonia and hydrogen sulphide.
Toxic gases have the potential to cause human harm through inhalation and the routes of exposure.
How are Gases Used?
Gases are used for a varied range of applications, such as:
- Heating
- Cooking
- Medical Use
- Industrial Processes
- Manufacturing
- Water Treatment
- Refrigeration
- Chemical Production
Due to the various properties of these gases — the very properties that make them useful for diverse applications such as heating or refrigeration — the gases require dedicated storage and segregation so no other hazards can be created with gases mixing.
We’ll look at the segregation requirements for gases in the next section of this post.
What is Chemical Segregation?
The process of segregating dangerous goods from other substances and materials which may react and create a hazard is a very significant consideration when managing risk in organisations. Chemical segregation is the identification of incompatibilities — or substances that may react dangerously with each other — and ensuring that these substances do not meet in the workplace.
How you segregate chemicals is by placing physical distances and barriers between the goods, so that gases and substances don’t mix, spill or otherwise encounter each other.
Segregation for dangerous goods is a vital consideration when planning on how to handle and store your substances.
Segregation is generally ensured through providing:
- Dedicated storage for each division or class of dangerous goods
- Adequate ventilation, natural or mechanical, so vapours and gases can’t react
- Measuring physical distances between handling or storage areas, so incompatible goods are separated from each other
- Separate spill bunds so substances don’t meet (if dangerous goods are in liquid form)
- Correct PPE for each chemical, so there is no cross-contamination
- Staff training to ensure controls are maintained and segregation is enforced
Segregation requires the separation of incompatible gases and dangerous goods, as well as suitable ventilation methods.
What are the Segregation Rules for Gases?
Best practice for the handling and storage of dangerous goods falls within the Australian Standard specific to that class or division. For gases, the Australian Standards states that gases must be segregated from other gas divisions by a distance of at least 3 metres.
It’s important to note that the segregation must apply to the primary risk of the gas, as well as the subsidiary risk.
In addition to this, if gases within a subclass/division are incompatible, these must also be segregated.
You must be mindful that your gases may be incompatible with a range of dangerous goods and other materials, so check your safety data sheet for each gas product to determine what other segregation rules apply.
Rules of Gas Segregation
You must segregate gases to ensure health and safety in the workplace. Segregation will dictate how and where you store your gases, specifically – where you install your gas stores.
The segregation rules for gas include:
- Class 2.1 must be segregated from Class 2.3 or Class 2.2/5.1 by at least 3 metres
- Class 2.3 must be segregated from Class 2.1 or Class 2.2/5.1 by at least 3 metres
Important: See the standard for details on how to measure distances.
In addition to the segregation of gases, you must also be aware of the segregation rules that apply to your other dangerous goods.
Segregation is required for many other DG classes including:
- Flammable Liquids
- Flammable Solids
- Spontaneously Combustible Substances
- Dangerous When Wet Substances
- Oxidising Agents
- Organic Peroxides
- Toxic Substances
- Corrosive Substances
Refer to your own onsite risk assessment, as well as each current safety data sheet, to determine sufficient segregation for gases and dangerous goods at your worksite.
Dedicated Gas Storage
Segregation of gas divisions is made simpler when choosing dedicated gas cages. Each store can be located in a suitable, protection position at least 3 metres away from other gases onsite.
Equip your gas cages with the appropriate dangerous goods diamonds, such as either:
- Class 2.1 Flammable Gas
- Class 2.2 Non-flammable, Non-toxic Gas
- Class 2.2/5.1 Oxidising Gas
- Class 2.3 Toxic Gas
Isolate from Ignition Sources
Gas stores must also be kept away from all sources of heat and ignition. This includes ignition sources that are fixed in place, such as a power point or hot surface, or those that are portable and may be accidentally brought into the work area, such as a lighter or welding torch.
Gases should never be around heat or direct sunlight as this can result in a fire or explosion. In addition to that risk, exploding cylinders can also create severe damage due to the metal pieces becoming dangerous projectiles.
The signage to exclude ignition sources from a gas storage or handling area is below:
Empty Cylinders
Due to the hazards associated with empty cylinders, which can still hold the residue of gases which may be flammable, corrosive, toxic or oxidising – and otherwise dangerous – you should treat ‘empty cylinders’ with the same care as any other full gas cylinder.
This means that your empty cylinders should be stored and segregated to avoid incidents and hazards. We recommend storing empty cylinders in dedicated stores prior to their recycling or disposal, that are segregated from incompatible gases, goods and materials.
Gas Storage and Safety
While there are many considerations for the segregation of gases in the workplace, the handling and storage of your Class 2 dangerous goods can be made simpler by using a risk management methodology. The Storemasta methodology is a 4-step process that will IDENTIFY – ASSESS – CONTROL risks, then SUSTAIN compliance through regular inspections and maintenance. Access your copy of our free eBook Gas Cylinder Storage: Compliance and Safety Requirements to learn more abour managing gas risk in your organisation. Download yours today.
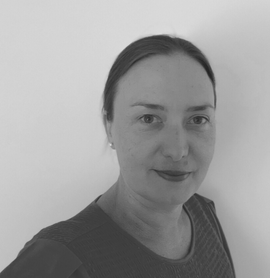
Living life by the 4 C’s of marketing – communication, coffee, compliance… and more coffee – Leisa Andersen is Storemasta’s Content Marketing Manager. When she’s not writing, you’ll find her enjoying all the good things in life, including shopping, travel and gluten free donuts.