If your workplace carries hazardous chemicals (or generates them during work processes) you’ll need to carefully assess your work procedures and chemical storage areas — looking at ways to reduce the likelihood of your workers suffering chemical burns to the eyes or other injuries.
You’ll also need to consider the first aid and emergency equipment required under the law. This blog focuses on eyewash stations, which are a mandatory requirement if you carry flammable liquids, corrosive and toxic substances, as well as certain quantities of other Dangerous Goods.
REMEMBER: Don’t mistake an emergency shower for an eyewash station — they are not interchangeable. Emergency showers are designed to deliver high volumes of water under pressure to soak the whole body and are not suitable for use as an eyewash station.
Eye injuries at work
Chemical burns to the eyes can happen when a hazardous liquid, powder, or dust contacts the eye. These injuries mostly occur after liquid chemicals accidentally splash over the face, but some chemical burns are caused by workers rubbing or scratching their eyes after handling chemicals. The severity of the burn will mainly depend on:
-
The type of chemical (acid, alkali, lachrymatory agent, toxin)
-
How much of the chemical contacted the eye (one drop vs a burst pipe sprayed directly into the face)
-
How concentrated it was (100% concentration vs 20% concentration)
-
How long the chemical was in the eye before being flushed with water (10 seconds vs 5 minutes)
Many liquid soaps and cleaning agents will irritate and redden the eyes, but symptoms begin to disappear as the chemicals are flushed out with water. Acids and alkalis, are far more dangerous because they can quickly kill eye tissue causing permanent eye damage and blindness. At the same time, some chemicals also cause rapid poisoning as toxins are absorbed into the bloodstream — and much faster than if the chemicals were absorbed through the skin.
If chemicals are splashed into the eyes, it essential your worker’s eyes are irrigated as quickly as possible. The American International Medical University advise that “patients with immediate copious irrigation have less severe injuries, as compared to eyes which are not irrigated”. A compliant eyewash station must be in reach and capable of delivering a consistent stream of water for at least 15 minutes, but many alkalis require 30-60 minutes of irrigation.
IMPORTANT: Eyewash stations must be easily accessible and should take an injured worker no more than 10 seconds to reach. A risk assessment on the chemical hazards and workplace layout is the best way of determining the best location.
Installing eyewash stations
The location of your eyewash station will be critical to the health of your workers. Under Australian Safety Standards an eyewash station is usually placed with 10 metres (but not closer than 2 metres) to chemical stores, but for some chemicals (eg, strong acids and strong caustics) it should be placed immediately adjacent to the hazard.
Compliant eyewash stations are:
-
Able to deliver a continuous flow of water to both eyes (simultaneously) at a pressure that will not cause injury.
-
Installed in an area that is well illuminated.
-
Easily recognisable with a sign that is visible to the whole area served by the eyewash station. We recommend eyewash stations that have a high-vis powder-coat finish.
-
Located on the same level as the chemicals with a clear path from the hazard to the eyewash station. It is essential that this path is always free of obstacles and obstructions eg, don’t leave a stack of pallets between the HAZCHEM store and the eyewash station.
-
Fitted with caps (or similar) to protect the nozzles from airborne contaminants (eg, dust, metal grindings) and the unit should also have filters to protect the eyes from debris or other particles in the water.
REMEMBER: Eyewash stations should be plumbed in by a competent professional then inspected, tested and tagged annually to ensure compliance with AS 4775—2007 Emergency eyewash and shower equipment.
Staff training workers in eye emergencies
To be effective, all hazard control measures (including eyewash stations) require the acceptance and understanding of your staff and workers. It is essential under AS 4775—2007 Emergency eyewash and shower equipment that you provide sufficient training to your workers. They’ll need to know where the eyewash stations are located and how to use them correctly.
Features of the training should include:
-
Locating the eyewash station in an emergency situation — workers should know how to treat themselves or another worker.
-
Activating the eyewash station using a single foot or hand action.
-
The length of time to keep flushing the eyes.
-
Safely removing contaminated PPE and clothing.
-
Specific chemical properties of the substances they use and how they could affect their eyes.
-
Things not to do during treatment: don’t rub the eyes, stop the flow of water, use additional soaps or chemicals.
IMPORTANT: It’s also important to train staff in general maintenance and care of the eyewash station. It’s the equipment that could save their eyesight — or even their life — so treat the units with respect and care.
Next steps
An eyewash station is a mandatory requirement under Australian Safety Standards if your workers are exposed to certain hazardous chemicals and Dangerous Goods. To learn more about how to assess and control chemical hazards that require eyewash stations or similar control measures, download our free eBook How to manage the risk of Hazardous Chemicals in the workplace. It’s easy to read and contains the necessary tools and resources to assess the chemical hazards at your job site. Download and read it today by clicking on the image below:
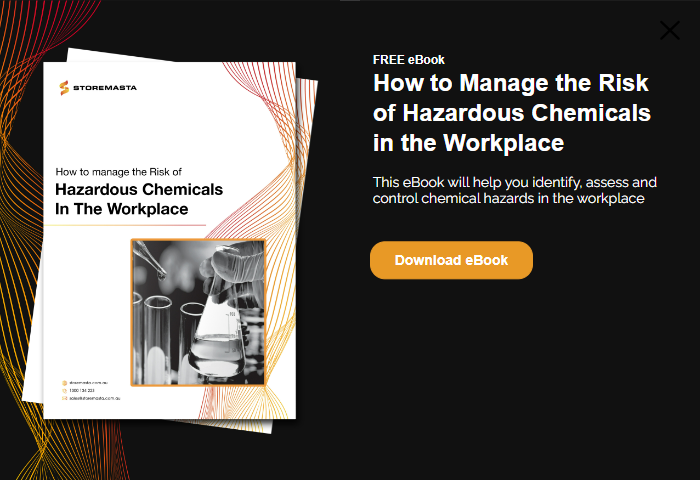
Joining the team as a Dangerous Goods Storage Consultant, Melissa Hampton became Storemasta's Marketing Manager in late 2021. With extensive knowledge and experience in chemical compliance, Melissa is responsible for leading the Marketing team and helping shape their marketing strategy. In her spare time, you can find Melissa hiking, swimming and enjoying the great outdoors in beautiful north-west Tasmania.