If you’re searching for the best chemical storage for your business, there are a few key factors to consider before you start purchasing equipment. In this post, we’ll be looking at key storage considerations for some common classes of dangerous goods and offering some tips on best practices for workplace chemical storage.
Where is a Safe Place to Store Chemicals?
In a nutshell, the best chemical storage is one that provides optimum safety for your workplace, environment and community.
A safe place to store chemicals in the workplace involves a wide range of factors, including but not limited to:
- A compliant chemical cabinet or outdoor chemical store that meets Australian Standards
- Located in a position that considers the safety of operations, as well as the community, including provision for evacuation, chemical segregation, isolation from ignition sources and other hazards, and separation from boundary lines or protected places (for outdoor storage)
- Suitable ventilation for the type and quantity of chemical held
- Correctly placarded with the right dangerous goods diamond/s and hazard signage
- A location, either indoors or outdoors, that meets regulatory requirements for aggregate quantities of chemicals stored
- Well-lit area to ensure operator safety when using the chemicals or putting them away
- Chemical storage operations that are used and maintained by staff who are trained in the chemical that they’re using, as well as the equipment itself
REMEMBER: To learn more about the specific conditions for storage, see the relevant Australian Standard to determine if you have minor quantities, package store quantities or bulk quantities of chemicals. This will also help you decide if an indoor or outdoor dangerous goods store is the right fit for your operations.
Best Practices for Chemical Storage
You can install the best dangerous goods storage equipment – but if it’s not used, cleaned, inspected and maintained as it should be, you’re decreasing chemical safety at your site. So, what are some of the best practices for proper chemical storage in the workplace?
- Load / stack your cabinet or store to ensure stability of containers
- Check your containers to ensure they are suitable for your chemicals
- Make sure staff are wiping down chemical containers after use, and securing them properly
- Inspect containers to ensure the labels are still accurate and in good condition
- Note any cracks or damage to containers, and replace immediately
- Keep a spill kit, suitable for your chemical and your chemical capacity, in close reach of every dangerous goods store
- Don’t replace componentry or shelving in your cabinet without consulting the manufacturer
- Identify and remove any expired chemicals
- Monitor store conditions for potential hazards including leaks, spills, extreme temperatures or damage to containers or store
- Keep hazardous chemicals and dangerous goods secured to avoid theft, misuse and vandalism
- Maintain store dangerous goods diamonds and relevant hazard signage
The correct selection and maintenance of equipment can provide a best practice solution for chemical storage.
Segregation
If you’re a regular reader of our posts, you’ll know that dangerous goods segregation is one of the most crucial factors to consider when setting up your safety cabinet or outdoor chemical store.
However, if you haven’t checked the segregation guidelines in sometime, you may be unaware of some changing segregation rules for your store.
Segregation involves the physical separation — by stores, physical barriers, walls, separate bunding systems etc. — from incompatible substances. An incompatible substance is one that can affect the safety of your chemicals, potentially causing a range of hazards or violent chemical reactions. Dangerous goods segregation is important, but it doesn’t have to be a complicated and confusing task.
We recommend choosing compliant dangerous goods cabinets or outdoor chemical stores (view the full Storemasta range) for each class of chemicals at your site.
Then, refer to the latest guidelines — via the Australian Standard for mixed classes of dangerous goods — on chemical segregation. This will ensure you’re installing your equipment at a suitable distance to prevent substances and their vapours mixing. Alternatively, speak to our Dangerous Goods Storage Consultants who can assist with your indoor and outdoor chemical storage queries.
What are Some Key Hazards with Commonly Used Chemicals?
We’ll now have a quick look at some important considerations when storing your workplace chemicals. These hazards, which are detailed in your safety data sheet for each product — as well as explained in the relevant Australian Standard — are those factors that need to be controlled so that you can provide the best chemical storage for your operations.
In addition to identifying your chemicals correctly and implementing compliant storage, it’s also vital that a risk assessment is done onsite in case any additional hazards are present – or will be created with the introduction of chemical storage. When in doubt, get in touch with a qualified Dangerous Goods Consultant who can guide you through the dangerous goods risk assessment process with authority and accuracy. Afterall, chemical safety is a complex subject which requires the knowledge of regulations, requirements and the unique risks at your site.
Class 2 Gas Safety Issues
Class 2 gases encompass a range of dangerous gases including compressed gases, liquefied gases, refrigerated liquefied gases and dissolved gases – to name just a few.
These gases pose specific hazards that must be carefully managed to ensure safety. Here are key hazards associated with Class 2 gases:
- Pressure Hazards: Compressed gases are stored under high pressure, and improper handling or storage can lead to ruptures or explosions. Release of compressed gas can cause physical injuries and damage to equipment. A compliant gas cylinder storage cage can mitigate the risks associated with pressurised gases.
- Cryogenic Hazards: Some Class 2 Gases are cryogenic, meaning they are stored at extremely low temperatures. Contact with cryogenic gases or their containers can cause frostbite or cold burns, leading to tissue damage.
- Flammability: Certain compressed gases are flammable, posing a risk of fires or explosions. Flammable gases can ignite in the presence of an ignition source, such as open flames or sparks.
- Toxicity or Corrosive Properties: Some Class 2 Gases are toxic or corrosive, which can result in chemical exposure and human harm. Proper precautions, including adequate ventilation and personal protective equipment, are necessary to prevent exposure.
- Incompatibility: Gases can react with other gases and substances, so the careful segregation of goods is vital for gas cylinder safety.
- Gas Leaks: Accidental leaks or releases of compressed gases can lead to rapid dispersion in the air. This may create hazardous atmospheres, especially if the gas is flammable, toxic, or displaces oxygen.
- Valve and Regulator Failures: Malfunctions or failures of valves and regulators can result in uncontrolled releases of gas. Regular inspection and maintenance of equipment are crucial to prevent such failures.
Gas stores offer natural ventilation, projectile protection and security for cylinders so they don't topple and fall, causing hazards in the workplace.
IMPORTANT: For more information on the hazards of dangerous goods, please see our popular blog: The 9 Classes of Dangerous Goods.
Flammable Liquid Storage Considerations
Flammable liquids, as the name suggests, pose several hazards that need to be carefully managed to prevent accidents and incidents, including fires and explosions.
Key considerations of flammable liquid storage include:
- Vapours: Flammable liquids release harmful, flammable vapours that can form explosive mixtures with air. These vapours are often heavier than air and can travel along surfaces to reach distant ignition sources, increasing the risk of fires or explosions. They also pose a risk to human health. Choosing indoor equipment that controls vapour emissions is essential for fire control; while outdoor stores must be equipped with suitable ventilation, such as natural ventilation via multiple walls of louvres.
- Flash Point: The flash point is the lowest temperature at which a liquid can produce enough vapor to ignite. Class 3 flammable liquids, such as petrol, kerosene or acetone, typically have low flash points. This makes the substances susceptible to ignition — even at relatively low temperatures. Therefore, flammable liquid storage must tightly control the risk of fire through non-combustible stores, control of vapours, isolation of ignition sources and containment and cleanup of leaks and spills.
- Static Electricity: The flow of flammable liquids can generate static electricity, which may lead to sparks. This static electricity works as an ignition source – resulting in fires or explosions. The control of static in the workplace, as well as the utilisation of grounding equipment and bonding techniques can help dissipate static charges.
- Leaks and Spills: Accidental leaks or spills of flammable liquids can create flammable vapor clouds, increasing the risk of fires. Proper containment measures, like secondary containment systems, are essential to minimize the impact of leaks.
- Ignition Sources: Open flames, hot surfaces, or other ignition sources should be prohibited, with staff trained to identify an ignition source correctly (including mobile phones or other objects accidentally brought into an area)
Key Hazards of Corrosive Substances
Corrosive substances present some unique hazards that require careful management to ensure the safety of individuals and the surrounding environment.
Consider the following when selecting storage for corrosive substances:
- Corrosion of Property: Corrosive substances can corrode and damage materials, including metals, concrete, and certain types of plastics. This can compromise the structural integrity of equipment, containers, and corrosive storage. Therefore, corrosive storage must be suitable for the corrosive substance stored.
- pH Level of Substance: The pH level of your corrosive substances will determine the type of storage facility you have. For example, a highly corrosive substance – such as an acid – may require storage in a heavy-duty polyethylene cabinet, that won’t corrode when vapours are released. A Class 8 substance that is not identified as highly corrosive, may be safely stored in a metal corrosive cabinet or store, with the applicable spill trays to prevent corrosion from spills.
- Chemical Burns: Corrosive liquids can cause chemical burns upon contact with the skin or mucous membranes. The severity of burns depends on factors such as concentration, duration of contact, and the specific properties of the corrosive substance. Correct storage and handling procedures, aided by adequate ventilation and suitable PPE, can greatly reduce the risk of exposure and harm.
- Respiratory Irritation: Inhalation of corrosive fumes or corrosive vapours can irritate the respiratory system, causing difficulty breathing, coughing, and other respiratory problems. Prolonged exposure may lead to chronic respiratory issues. Consideration may be given to mechanical ventilation of indoor stores.
Get the Best Dangerous Goods Storage to Suit Your Worksite
For assistance with dangerous goods storage selection, including the right indoor or outdoor store; suitable capacity; correct model and other queries – get in touch with our DG Storage Consultants who can help you with implement safe and compliant storage. To learn more about safe storage in the workplace, why not purchase our handy Ultimate DG Storage Guide for all the answers to your essential chemical storage questions.
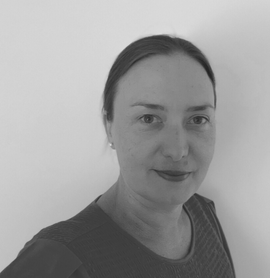
Living life by the 4 C’s of marketing – communication, coffee, compliance… and more coffee – Leisa Andersen is Storemasta’s Content Marketing Manager. When she’s not writing, you’ll find her enjoying all the good things in life, including shopping, travel and gluten free donuts.