What Hazards are Associated with Pool Chemicals?
Pool Chemical Classification
Examples of Commonly Used Pool and Spa Chemicals
What Australian Standards May Apply to Pool and Spa Chemicals?
Key Considerations for Retail Outlets with Pool Chemicals
Pool & Spa Chemical Safety
Pool chemicals are hazardous substances used to maintain health and safety of pools, spas and other aquatic areas. But in a retail setting – where you can have large amounts of these goods – what are the considerations you need to make to ensure these chemicals don’t harm staff, customers, property or the environment? In this post, we dive (sorry, but it had to be done!) into the requirements for retail outlets that stock pool chemicals.
What Hazards are Associated with Pool Chemicals?
As Australians, most of us are familiar with the pungent smell of chlorine in a spa or swimming pool — but what hazards are these chemicals actually posing to the people that are working with them?
Pool chemicals are strong substances that may have a range of properties. These are specific to the chemical product but may include corrosive, oxidising, water-reactive or combustible properties. This means that chemicals may corrode metal or living tissue (including human skin and eyes), react with other chemicals or increase a fire hazard.
Due to the hazardous nature of pool chemicals, these products must be stored and managed in a way that prevents harm, such as health issues, environmental damage or corrosion of property.
There are many hazardous substances required for pool maintenance, but these must be stored and handled in a way that reduces harm.
Pool Chemical Classification
The first steps in determining how to handle and store your pool chemicals is understanding what substances you’re storing.
Many pool and spa chemicals are deemed ‘hazardous’ in the Globally Harmonized System of Classification and Labelling of Chemicals (otherwise known as the GHS).
The GHS is an internationally recognised system that allows the accurate communication of information about hazardous chemicals through labelling and safety data sheets. Knowing the physical and health hazards of the pool chemical is vital for maintaining the health and safety of any workplace operations.
Safety data sheets of hazardous chemical products outline the physical and health hazards associated with that substance. There are many sections that offer vital information about the substance including:
- Section 2 Hazard(s) Identification
- Section 7 Handling & Storage
- Section 8 Exposure Controls & Personal Protection
- Section 9 Physical & Chemical Properties
- Section 10 Stability & Reactivity
- Section 11 Toxicology Information
Understanding this information will provide the foundation upon which your risk management process is built. Whether you're dealing with the dangers of pool chemicals (or other hazardous chemicals or dangerous goods) in your organisation, a risk management approach is crucial for health and safety.
REMEMBER: Learn more about safety data sheets, including how to read, store and maintain them, in our helpful blog post.
Examples of Commonly Used Pool and Spa Chemicals
In Australia, commonly used pool and spa chemicals include disinfectants, pH balancers, algaecides, and other specialised treatments. Here’s a rundown of some of the most widely used types:
Chlorine:
- Sodium Hypochlorite: Common for large pools as it’s easy to dose, but it has a shorter shelf life.
- Calcium Hypochlorite: Often used in residential pools. Needs to be dissolved before adding to prevent direct contact with pool surfaces.
- Stabilised Chlorine: Tablets or granular chlorine combined with cyanuric acid (a stabiliser) to protect chlorine from sunlight degradation.
- Bromine: Preferred in spas and hot tubs due to its stability in high temperatures and its ability to sanitize effectively, though it’s slower-acting than chlorine.
pH Balancers:
- Sodium Carbonate: Raises pH levels of the pool.
- Muriatic Acid or Sodium Bisulfate: Used to lower pH when levels are too high.
- Algaecides: Copper-based and quaternary ammonium compounds are commonly used to prevent algae growth.
What Australian Standards May Apply to Pool and Spa Chemicals?
The Australian Standards are highly detailed documents which are considered best practice for dangerous goods and hazardous substances.
There are various Australian Standards that may apply to pool chemicals, including:
- AS 2780 - The storage and handling of corrosive substances
- AS 4326 - The storage and handling of oxidising agents
and, when using mixed classes of chemicals, such as those with corrosive properties and oxidising properties:
- AS/NZS 3833 - The storage and handling of mixed classes of dangerous goods in packages and intermediate bulk containers
You can use these Standards in your workplace for guidance on how to handle and store your substances, with relation to ventilation, handling practices, storage equipment, spill control, first aid and emergency procedures.
REMEMBER: While the Standards are best practice, retailers must always abide by the Work Health and Safety laws or Dangerous Goods laws that apply to their region. Learn more in the blog Storing Dangerous Goods in a Retail Setting.
Key Considerations for Retail Outlets with Pool Chemicals
Just like any type of hazardous substance or dangerous goods, there are basic steps required to control risks. While an onsite risk assessment is important for understanding the complete picture in regard to chemical safety, there are some key considerations to make when selling pool chemicals.
Segregation of Pool Chemicals
Many substances should not be mixed or stored near each other due to the potential for harm. A liquid pool compatibility chart is an important resource that can prohibit incompatible substances from being mixed in the spa or pool.
Segregation of goods is also vital for the safety of the retail outlet and surrounding community, as incompatible substances can become unstable or react. For example hydrochloric acid is not compatible with hypochlorite solutions.
The Australian Standard for mixed goods AS 3833 explains that pool chemicals must be segregated from incompatible substances and those that might react dangerously. Segregation includes:
- Incompatible substances: Kept at least 3 metres apart, with separate bunded areas.
- Substances that might react dangerously: Kept at least 3 metres apart, not kept within the same bunded area.
Always remember that some chemicals can still be incompatible or react dangerously within their own class, so always determine the incompatibilities or reactions of your individual pool products.
IMPORTANT: Read more about segregation in a retail business in the blog Retail Stores: Segregation Requirements When Carrying Mixed Classes of Dangerous Goods.
Hazardous Chemical Register and Manifest
When storing hazardous chemicals, a register is a must. This register is a list of all hazardous chemicals at your store, which must be always kept up to date. Unlike the manifest, which is only for businesses with chemicals above manifest quantities, the hazardous chemical register is required when carrying any volume of hazardous chemicals.
Check with your local regulator to determine if you also require a hazardous chemical manifest for your business. The manifest will be required if the type and quantity of chemical exceeds a certain amount. The manifest must be prepared in accordance with regulations and may have to be submitted to your local fire service.
The manifest is for emergency services who may attend your site and must be stored in an Emergency Information Box at a specific location on your property. You may liase with fire services when determining the best location.
Spill Clean Up
While every precaution should be made to ensure that there are no spills of pool chemicals, accidents can happen. However, it’s your duty to make sure that these minor chemical spills don’t become a major problem.
Spill containment and clean up should be conducted by trained personnel who are wearing the appropriate PPE (see your safety data sheet) for the spilled substance. Areas should be cordoned off so that no customers come into contact with the spill, and care should be taken to ensure that adequate ventilation is considered during the clean-up process. Use the appropriate spill kit that is both compatible with your substance and suitable for the quantity spilled.
The proper waste disposal procedures must also followed to ensure that no hazardous chemicals are thrown out with the regular rubbish – potentially harming people or the environment.
Access to Safety Data Sheets
Staff should have easy access to safety data sheets at all times, so they can better handle and store these pool chemicals in the safest possible manner. If there is an incident, such as a fire or large spill, emergency services will also need access to these safety data sheets so they can accurately assess the situation and provide a suitable emergency solution. We recommend storing safety data sheets in an SDS folder and document holder that’s located close to the chemicals that you’re storing. The safety data sheet folder will keep the SDS safe and accessible, with a waterproof SDS holder being able to be attached to walls or storage.
Ventilation
When managing the risks of any type of hazardous chemical, airborne contaminants are a key concern. Chemical exposure doesn’t only happen if substances are spilled onto the skin, harm can occur when the vapours are breathed in by workers or customers.
Keeping your store clean, tidy, free of spills and well ventilated is part of maintaining a healthy, safe workplace.
Deliveries & Handling
Working in retail isn’t just about reducing the dangers within your store – it’s also about reducing risk in all aspects of your operations.
Spills and other hazardous incidents can occur when chemicals are being delivered or transported around a business. Care must be taken to develop procedures that reduce the likelihood of a pool chemical spilling or coming into contact with incompatible substances, ignition sources or other prohibited items.
Storage
Guided by your safety data sheet, retailers must adhere to the storage practices required for individual chemical products. Many substances may react or become unstable if they aren’t stored in the correct conditions.
Consider:
- Quantities – there are maximum quantities that apply to the storage of pool chemicals. However, these may vary across jurisdictions. Please liase with your local regulator to learn more about the quantities applicable for your situation.
- Temperature – many substances must be stored in controlled conditions to remain stable and also effective for use.
- Ignition sources – there are many classes of goods that must be separated from any type of heat or ignition source due to fire risk. The general separation distance is at least 3 metres. If your substance can ignite or heighten a fire risk, you must also show signage to prohibit smoking and ignition sources in the area where chemicals may be handled or stored.
- Moisture – some chemicals, such as calcium hypochlorite, must be separated from moisture or they can decompose, creating chlorine gas.
- Security of storage area – don’t allow untrained personnel access to hazardous chemicals and maintain visibility over areas in the store with hazardous chemicals to deter tampering.
- Containers – ensure all containers are clearly marked with labels, are not kept lying down, opened or otherwise in poor condition. Packages should be stacked in a safe way that prevents toppling and subsequent spillage.
- Shelving & racking – retailers must have the appropriate shelving for pool chemical storage so no harmful liquids can be absorbed. Metal shelving is suitable, while MDF, plywood or unprotected chipboard is not suitable. Shelving should be constructed in a way that allows for cleaning and maintenance, as well as emergency evacuations.
- Inspections – storage areas and containers should always be inspected to make sure that there are no chemical leaks, spills or other potential dangers.
Pool & Spa Chemical Safety
From spill containment and clean up to chemical segregation and storage, there are many practical ways that you can ensure safety and compliance when working with hazardous chemicals and dangerous goods, To learn more about the important process of risk management for any business carrying these types of substances, simply download our FREE pack.
This helpful template pack resource offers easy to follow templates that can help you identify and assess risk, while controlling them and sustaining ongoing compliance. It's an ideal tool when managing your chemical risks. Get your free template pack now.
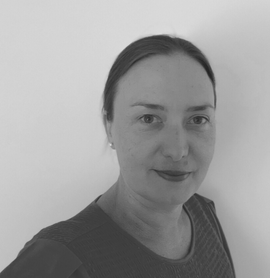
Living life by the 4 C’s of marketing – communication, coffee, compliance… and more coffee – Leisa Andersen is Storemasta’s Content Marketing Manager. When she’s not writing, you’ll find her enjoying all the good things in life, including shopping, travel and gluten free donuts.