If you store any type of compressed gases in cylinders at your workplace, you’ll need to carefully evaluate their potential to cause harm. After the risk has been properly assessed, you will then be able to implement suitable control measures to make sure gas cylinders remain safe.
This blog introduces our methodology for risk management and takes a deep dive into the risk assessment process and how hazards are prioritised. We’ll be using both real world and theoretical examples to give you an idea of how to apply the methodology to your own gas cylinder storage areas.
What are Risk Control Measures?
Risk control measures are systems or equipment that helps control risk. Gas cylinders present a number of different hazards, and it’s often difficult to determine how those hazards could interact with each other. Therefore, organisations should consider implementing a suitable risk management strategy to mitigate the chemical risks as well as the handling hazards and incompatibility hazards associated with the gases in cylinders. This is a process which results in the implementation of risk control measures to ensure that dangerous goods are kept safe onsite.
What is a Chemical Risk Management Methodology?
A risk management methodology is systemised way of identifying the hazards at your workplace, then determining the best way of reducing the chances of them causing a dangerous event, injury or death. Here at Storemasta, we’ve developed a methodology for assessing the risks associated with dangerous goods, such as compressed gases.
It consists of four essential steps which we outline below:
- STEP 1 IDENTIFY the cylinder hazards at the workplace.
- STEP 2 ASSESS each of the gas cylinder hazards, taking into consideration how likely they are to cause a dangerous event and what would be the consequences if they did. Create a priority list following your risk assessment.
- STEP 3 CONTROL you must eliminate risks or control each of the hazards associated with the gas cylinders with risk control measures. Use the priority list created in step 3 then implement changes to the workplace to reduce the likelihood of (or prevent completely) a dangerous event involving gas cylinders.
- STEP 4 SUSTAIN safety compliance. Review each of your control measures by conducting a follow up risk assessment of your gas cylinder stores, handling areas and procedures. Schedule regular reviews and maintenance.
The methodology operates in a circular form, where each of the 4 steps is dependent on the previous one. Once you’re at step 4, you return to step 1 as you undertake follow risk assessments and reviews.
Conducting A Risk Assessment
Gas cylinders have the potential to cause many different types of incidents or workplace accidents. Handling a cylinder incorrectly could cause a back strain injury, but if he or she drops that heavy cylinder it could create an explosion or expose a worker to toxic gas.
Therefore, your gas bottle risk assessment needs to look at:
- Ways in which your compressed gases could cause dangerous events, deaths or injuries.
- How likely these events are to occur (likelihood).
- What would be the outcome if the dangerous event occurred (severity).
Assigning Risk Scores To Hazards
In the Storemasta methodology we assign an overall risk score to each of those dangerous events (hazards), then create a priority list and action plan based on those scores. The hazards with the highest risk scores will be dealt with first.
A risk score is given to hazards, which factors in the likelihood and severity of an incident.
Let’s imagine your workplace uses LPG cylinders to fuel your forklifts. LPG is a class 2.1 Flammable Gas and capable of igniting or causing an explosion, an asphyxiant that is denser than air, and capable of causing thermal injuries and damage to electronics or equipment if rapidly released from the cylinders. At the same time employees could be injured when trying to manoeuvre the heavy cylinders.
In your risk assessment you would list all those hazards, but in our example, we’ll use the thermal hazard presented by LPG if rapidly released from the cylinder.
A documented accident did occur in the USA where a worker was changing forklift cylinders and hadn’t closed the cylinder valve properly on one of the cylinders. Wearing only cotton gloves he received severe burns and was hospitalised when he tried to shut down the valve.
If the cylinders are being changed every day, staff often forget to wear their PPE. If staff training hasn’t been conducted in more than a year, it’s almost certain this incident will occur.
The frostbite injuries are unlikely to kill a worker, but serious injuries are very possible. If there is only one worker in the area and there are no risk of injuries extended to another worker.
Likelihood of a Gas Cylinder Incident
To determine the likelihood of the frostbite injuries you need to consider how often the forklift cylinders are changed, if anyone has received a frostbite injury at the worksite in the past, whether there are clear operating review procedures that detail the correct way to change the cylinders, and whether the staff have been trained. If you noted that new staff members had not been properly trained, or a staff member who has been on long service leave returns to work without refresher training that might increase the likelihood. Now assign a score out of 5 for likelihood.
Severity of a Gas Cylinder Incident
To determine the severity, you would look at the worst possible outcome. A minor incident would be one that is quickly contained — and does not cause any injuries. A major incident might involve a fire and injuries. A catastrophic incident leads to fatalities and significant property damage.
A catastrophic external incident would be something that cannot be contained onsite and causes damage to the environment or adjacent properties. Again, give the severity a score out of 5.
Now continue through for all the cylinder hazards at the worksite. We’ve created another dummy example below: an explosion.
Let’s add to the list from above that staff carry personal electronics and there are no real controls to reduce static electricity or ignition sources in the area.
An explosion could lead to fatalities and major property damage. Perhaps it could be contained on the site and not affect the external environment.
Control Measure: Creating A Priority List
Adding the likelihood score and the severity score together will give you an overall total out of 10. Once you have assigned a risk score to each hazard, you can now create your priority list. All organisations have limited time and budgets and it’s unlikely you could address every hazard at the same time.
Storemasta's Gas Bottle Storage - Premium Range offers compliant storage that can be adjusted with the changing needs of your workplace. These stores can hold either aerosols, bottles or gas cylinders, but the rules of segregation still apply.
Your priority list helps you create an action plan based on the events that are most likely to occur and cause the most damage. Using two examples above you now have a priority list, but both hazards have the same score. In this instance you might have to dig a little deeper into the explosion hazard as the severity is much greater.
IMPORTANT: These examples are used to merely demonstrate how the risk score process works, always conduct your own risk assessment based on the cylinders and practices at your own workplace.
Gas Cylinder Risk Control Measures
For a more detailed look at the Storemasta risk management methodology, download our free eBook Gas Cylinder Storage: Compliance and safety requirements. The eBook is a tool for WHS Manager and supervisors responsible for managing gas cylinder storage and compliance. Download it today to learn more about implementing risk control measures for your gas bottles and compressed gas cylinders.
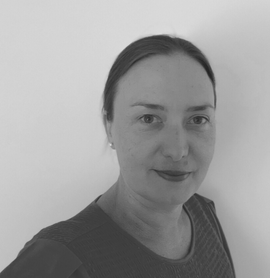
Living life by the 4 C’s of marketing – communication, coffee, compliance… and more coffee – Leisa Andersen is Storemasta’s Content Marketing Manager. When she’s not writing, you’ll find her enjoying all the good things in life, including shopping, travel and gluten free donuts.