If we had a dollar for every customer that said, “There’s not enough in this year’s budget, but I’ll try to get it into next year’s...” But when it comes to purchasing dangerous goods storage and handling equipment, not allocating funds for new or replacement items can impact the safety of your workplace. In this post, we’ll be looking at some practical ways that you can plan for dangerous goods storage purchases, so no one is put at risk with old, damaged or unsuitable equipment. We’ll also offer some tips on when to retire your old equipment and how to save money when selecting new items.
Preparing an Annual Budget
When you’re running a business, setting a budget is a necessary, yet challenging, task. Without a comprehensive and accurate budget, your workplace can’t operate to an optimal level.
And without that ability to properly forecast costs, you won’t be able to provide the goods and services necessary for your business to run smoothly and achieve further growth.
Creating a budget for your business allows you to identify:
- How much money is coming in
- How much money you've previously spent
- How much money you'll need to spend
If you don’t have enough money in your budget for new equipment or maintenance, then you may risk putting your workplace at risk of non-compliance.
Capital Costs
Chemical storage equipment and handling solutions are generally classed as ‘capital costs’. Capital costs are tangible and fixed. That is, they are property or pieces of equipment that are required to run your business. Other types of capital costs may include construction costs for new premises or the purchasing of manufacturing equipment for a factory.
IMPORTANT: Chemical storage equipment should be viewed in the same way that you see your tools, equipment, vehicles and devices. That is, this is an investment that will benefit your business. Your equipment should be regularly inspected, assessed and maintained to ensure its longevity and efficacy.
Planning for Chemical Storage Costs
Many larger companies may start planning for next year’s budget up to six months prior to the start of the new financial year. Many of these companies will also regularly analyse and review their budget to ensure that it still complies with the objectives of the business. However, smaller businesses may choose to budget for the next financial year just a few months prior.
Budgets may be annual or quarterly, with factors including revenue, variable and fixed costs, non-cash expenses, non-operating expenses and capital costs.
Whatever strategy you have for budgeting, don’t forget to include essential equipment and solutions that are necessary for meeting compliance obligations. By understanding your anticipated revenues and expenditures, you’ll be better equipped to operate your business in a methodical and effective manner.
IMPORTANT: Are you new to the world of chemical storage? Find out more about indoor and outdoor chemical storage solutions by reading our blog.
How to Determine Future Costs for DG Storage
New dangerous goods storage equipment is generally required when the existing equipment is:
- Showing signs of age
- Damaged, beyond reasonable repair
- Non-compliant
- Too small for the quantities of goods
- Not constructed to meet the requirements of the DG class
- Unsuitable for the job task
REMEMBER: A maintenance schedule can increase the safety at your site, as well as ensure the performance of your chemical storage equipment. Find out more by reading our post on maintaining compliant chemical cabinets.
To better prepare your business for the costs of dangerous goods storage and handling equipment for the new financial year, it’s a good idea to consider these questions:
- Are you storing any new substances onsite?
- Will we increase chemical inventory in any areas?
- Are there any new hazards that need to be controlled?
- Is the equipment nearing a time when it will have to be decommissioned?
- Do you need to increase efficiency with any systems or processes related to onsite chemicals?
If you are going to start working with a new substance, such as a corrosive liquid, you’ll need to look at your existing storage to see if it is suitable for the substance and the quantity you’ll be keeping.
You will also have to consider the many other pieces of equipment and materials that are purchased alongside chemical storage cabinets and outdoor containers.
These additional chemical safety items may include:
- Chemical bunding
- Spill kits
- Emergency showers and eyewash stations
- SDS folders and SDS document holders
- Hazmat boxes
- Accessories or spare parts (such as extra shelving for cabinets, dispensing trays for IBC bunds or ramps for low profile bund)
- Dangerous goods signage or hazard signage
Ensuring There’s Money for Essential DG Storage Items
As we’ve highlighted in the previous section of our post, there are many risk control items and safety measures that will help you create a compliant workplace. However, if there’s not enough money in the budget to allow for this, it may impact your business’ ability to grow – or negatively affect the safety at your site.
To make sure that you’re properly preparing your budget for such costs, develop (if you haven’t already) a system of inspecting, assessing and maintaining your equipment, so you have plenty of time to order new equipment, spare parts or even repairs.
You should also look at the business goals for the next financial year, as well as anticipated growth in areas that rely on dangerous goods and hazardous chemicals, to see if your existing equipment is sufficient.
Remember, the price of storage equipment (which may be several thousand dollars for a large capacity chemical cabinet), is a minor cost when comparing it to the clean-up of a large hazardous chemical spill – as well as any lost hours of production, damage to people or property, and fines for non-compliance.
Chemical spills and human harm are just some of the incidents that can occur if chemicals aren't stored or managed in a safe way.
Not only can dangerous goods put your people at risk of health hazards, but these chemicals can also impact local businesses and neighbourhoods, as well as polluting the natural environment through fumes or accidental releases.
REMEMBER: There are many financial costs associated with chemical incidents in the workplace. Find out more by reading our post ‘What is the Financial Cost of a Chemical Spill?’
Dangerous Goods Storage For Your Workplace
If you’d like to find out more about dangerous goods handling and storage equipment, and how you can meet your compliance obligations, we have an eBook that can help. The Ultimate DG Storage Handbook features all the important topics including dangerous goods classes, spill management, emergency decontamination and more. Grab your copy for just $6.99 + GST today.
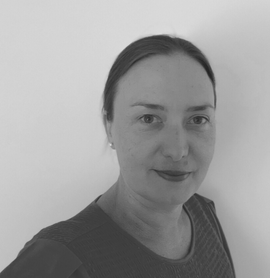
Living life by the 4 C’s of marketing – communication, coffee, compliance… and more coffee – Leisa Andersen is Storemasta’s Content Marketing Manager. When she’s not writing, you’ll find her enjoying all the good things in life, including shopping, travel and gluten free donuts.