David Irvine, Director and Principal Consultant at Dangerous Goods Network and DG Trainer, joins us on the Chemical Safety at Work podcast to discuss navigating the complex and ever-changing regulations and requirements around dangerous goods. We also chat about the importance of training for those working with dangerous goods, as well as the future of DG compliance including AI automation and digital transformation, how insurers shape dangerous goods storage, the DG skills shortage and much more.
DID YOU KNOW… Storemasta has partnered with Dangerous Goods Network and DG Trainer to offer a range of safety, compliance and training services? Whatever stage your business is at, our ecosystem of partners can provide the right risk management service or staff training solution.
Firstly, let’s talk about the trends you’re seeing in regard to safety and compliance with dangerous goods?
I think the trends are regulatory. Some of the areas that are really changing are around lithium batteries.
We're seeing that there's a push there to make some changes. While those changes haven't pushed all the way through, there's a desire there — especially from the emergency response departments of every state. In particular, New South Wales is pushing hard for that.
The other thing that we saw over the last several years is that most of the states have aligned under the model WHS laws — which has been good for consistency, for storage and handling that is in each of the states. Victoria is sort of the last holdout, but I'm sure that will change at some point in the future.
You've also got the Australian Standards continuing to update. There's been some recent updates, like AS 3833, which is the Standard for mixed classes of dangerous goods. I know that there's some work getting done on a lithium battery standard specifically as well, because that has historically been under Class 9. I think that we'll see some changes coming there, too.
How have you found implementing that standards update regarding mixed classes of DG into your work?
I think overall it's been fine. It depends on the nature of the business that we're working with; the complexity that they have, and the maturity that they have when it comes to compliance.
It's really a case-by-case basis and I think that, similar to other guests that you've had on the podcast, we see a whole spectrum of organisations from those who have no awareness at all and only twig after WorkSafe or the regulator rocks up, to others that are pretty mature and they just need a bit of fine tuning. We understand it quite well, so it's just working with the customers to implement the right solution for them.
What are the biggest challenges that companies face trying to maintain compliance?
There are quite a few things. I think one of the things that most of the companies struggle with is understanding and managing their storage threshold.
So, in every state your obligations are based on the amount and the type of dangerous goods that you're storing, so placarding is important. When we go out and work with a client, we'll ask them: what dangerous goods do you have on site? And they'll typically know what they have and how much they have. But then how does that relate to the regulations? I think that's where they struggle.
Another thing we see is around training and understanding what sort of training needs to be done. From a regulations perspective, whether it's under the OHS or the WHS regulations, in every state there is an overriding obligation that the employer needs to train and make the staff aware of the risks that they're exposed to and educate them on those.
So, obviously, if you have dangerous goods in your warehouse or in your place of business, then you should train people on that. I think that training requirement is often not well understood. Sometimes the training that gets done is not the right type of training, because it's not in context for what they're doing.
There's a heap of other things, but I think the other key one that I see a lot of is understanding how to manage the risks. So, knowing how to go about and perform a risk assessment:
"Identify the right types of hazards and then understanding how the relevant Australian Standards can be used as best practice risk controls — and you use those to help manage the risk."
That's another area businesses can struggle with and where we typically get involved. Those would be my three key areas, although I could probably rattle off a list of 20 other things.
What role do you see insurance companies playing in regard to dangerous goods storage and handling?
That's an interesting one that's always been there, but it's where we're seeing it that is changing and insurers are becoming more prescriptive about what they need.
Especially when you have a storage facility or a warehouse where they have a lot of dangerous goods, the insurer is insuring tens of millions, potentially hundreds of million dollars' worth of stock. So, they're typically putting a range of obligations on the business that's storing those dangerous goods, over and above what the regulations in any state require."
Typically, what we see is there's the FM global standards, which is really based around loss prevention. Typically, the FM global standards are — I don't know, I'm going to say stricter — or, you know, have higher levels of control than the regulations in any state do.
Often businesses are having to spend quite a lot on infrastructure. If their facility is not already designed to store dangerous goods and so they're trying to retrofit something, then that capital expenditure can be quite high, and I think it's also getting the businesses to understand that.
The insurers are worried about loss prevention of property. The regulations are more focused around protecting humans and the environment. Often they overlap, and often they don't as well. So, it's about understanding the driving forces.
"We're seeing insurers are playing a bigger role in dangerous goods compliance. Often when we consult a customer, that's the first thing we'll ask them:' Does your insurer know that you're storing dangerous goods at this property? Do they understand how much you have?' Because that's something you need to check."
What about lithium-ion batteries?
I think that we can all see, in the media and the news, the amount of incidents and fires that involve lithium-ion batteries is increasing.
Interestingly, the FM standards actually came out with their own standard about storing and handling those types of batteries, ahead of any regulations or standards. They're definitely at the forefront of it. It's risky because when a lithium-ion battery fire starts, then you've got thermal runaway.
It propagates to the other batteries and once those fires start, using conventional methods to extinguish them just literally doesn't work. And you kind of need to let the fire burn out. Obviously, the fire departments are focused on making sure everyone's out of the building, making sure the fire doesn't spread to surrounding properties.
But I think that the insurers have seen that that's probably their number one risk. If you're storing those batteries — and we're seeing more and more products out in the world today have that type of tech in them — and the batteries are getting bigger as well. So, I think that they can see the risk there, so they're trying to control that as much as they can.
With industrial manslaughter laws and higher penalties in place, how do you see liability changing for businesses handling dangerous goods?
The attitude there is changing for sure, and I think that most business owners, directors and senior managers that we go out and talk to are super aware that those laws are in place.
We’ve definitely seen a change in attitude. When we first go out and talk to people, they're sort of joining the dots on their obligations when it comes to dangerous goods. And then, as they quickly see that picture form in their mind, then they go, “Oh yeah, we definitely need to do something, because it’s the right thing to do.”
Not only because of the industrial manslaughter laws, but pretty much in every state in Australia, the fines and the penalties are going up. We're seeing that the regulators are being more proactive and going out more, and so that's having a flow-on effect as well.
Do you think there's a shortage of dangerous good professionals?
Yes, there is, and that's a bad thing overall. People might say, well, hey, you run a dangerous goods consulting business, so that's good for you. We do get a lot of calls, it's quite busy, but I think fundamentally overall for the industry it's not a good thing and I think that the challenges there are.
I think part of the challenge is that the nature of work now is that people don't work at places for 20 or 30 years anymore and you've got this built up experience and knowledge inside of an organisation.
People will tend to move jobs every two or three, maybe five years. Five years is considered a long time these days — and so you don't have that organisational knowledge.
One of the other drivers is with tertiary education. There's no unit in an engineering degree or course that covers dangerous goods compliance or regulation, so there's no formal way for people to learn that. People are learning on the job, so to speak.
While there are training organisations — like we do training —I think it's a different type of training to have that level of expertise. Organisations like the Australian Institute of Dangerous Goods Consultants (AIDGC) do a great job.
I think that there's a gap there. Thinking of strategies about how to address that gap and get more people up to speed is a good thing. It's also worth considering how you can use technology to bridge some of those gaps.
"The other thing, ultimately, is well-trained employees can help you manage the overall risk of the business."
Once we train people and let them know about the risks, we basically enlighten them that they're your first line of defence in ensuring that nothing ever escalates. That things don't escalate to the point where there is an explosion or a fire because people are aware of all those things I was talking about. Your staff are your first line of defence in helping prevent incidents in the first place.
It's important to consider the profile of your workforce and their level of skill and knowledge as it comes to dangerous goods. In some scenarios, going out and doing things face to face is going to be better if it's a high-risk activity. Or, if the staff don't really know anything about dangerous goods, and you need to do some hands-on things — doing that face-to-face is better.
In some scenarios, we're training remote over Zoom or some other tech. We'll often do that, and you'll have people dialling in from different places, so that will work as well.
What resources would you recommend if businesses don’t really know where to go or what to do first?
A good place to start is WorkSafe or the regulator in every state. And in every state, there's a code of practice for storing and handling dangerous goods, and so for those people that don't know, the code of practice is basically the regulations, but written in a more consumable and more easily understandable format. I wouldn't say it's the world's most exciting read, but it's one that you can understand. I think if people were unsure of their obligations, that's where I would start. Go and look at the regulator website. Go and have a look at the code of practice and get a general understanding of what your obligations are.
Contacting people like us at DG Network is a good thing to do, but I think there's some self-education that you can do first before you come to people like us and we're obviously happy to help.
What about the future of the industry? Where do you see growth?
I think the area where we're really going to see the growth is around AI. It's getting to the point where it's smart enough to overlay the regulations, the standards and all of those kind of nuances that we were talking about before. I think, in the next five years, AI is going to revolutionise a lot of things that we do.
If you could give businesses storing and handling dangerous goods one bit of advice for the future, what would that be?
Understand what dangerous goods, in what quantities, you have at your site. That is the key thing, because that is the foundation to manage the risk and your compliance.
They should have that at their fingertips. That's the key , and then everything cascades off that. It's pretty basic, but you would be surprised that a lot of companies can't answer that question easily.
It was really awesome to hear your perspective on all of that. What's next for you?
We're involved in three main companies that we run around dangerous goods. We've got Dangerous Goods Network, which is the consulting stuff that we've been talking to you about today, where we help companies with their storage and handling, going out, doing site assessments, writing up reports and providing advice. We also run a range of training courses through DG Trainer. We do them in person, we'll do them over Zoom with experienced instructors, and then we also have self-paced e-learning options, and we do partner with Storemasta and deliver some of the training with you guys as well.
The other part which we've been working on over the last 12 months pretty much is that we also run another business called Dangerous Goods Technologies. We’ve got one piece of software at the moment which we have a few customers on called SDS Connect, which obviously helps customers manage their SDSs.
But we're about to release in may a new piece of software called DG Expert, which is really around AI compliance. You'll be able to store your safety data sheets in there, and then we're focusing on the storage and handling regulations for each of the states in Australia —and then the Australian Standards that also apply. We’ll help businesses do those risk assessments that historically they've struggled with.
"Through the power of AI and the knowledge that we've got, we're going to help them do that. So, I think that's sort of our next big thing is to do that push into the technology and software space."
There's always going to be a need for consulting. There's always going to be a need for training. We see this as the next area that's going to evolve in the industry, and so we want to be part of that and help shape the future of what that's going to look like. There's always going to be these super complex, multiple things that we're going to need experts to do, but we have the belief that, like most stuff that we're doing on a storage and handling perspective, we think that tech can do that better.
To stream the full Chemical Safety at Work™ episode, visit your favourite podcast platform or watch the complete video on Youtube.
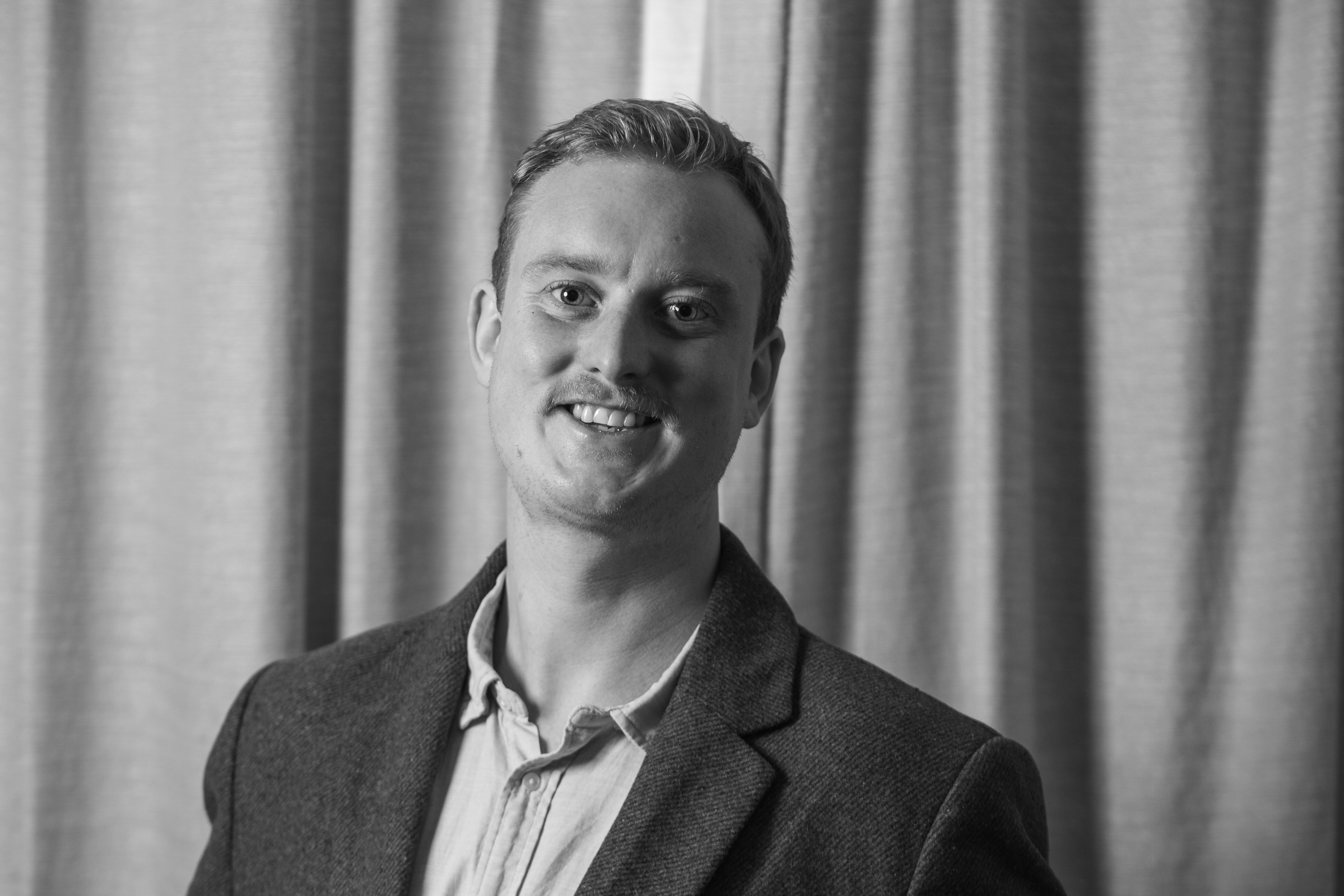
Patrick Gee is Storemasta’s Content Creator and Marketer. With background in journalism, Patrick is passionate about using his communication and photography skills to help organisations find safe solutions for dangerous goods storage. His Instagram is filled with pictures of his dog Milo, along with his travels throughout Australia and overseas.