1. Chemical Transfer Equipment
#2. Compliant Chemical Storage
#3. Emergency Decontamination Equipment
#4. PPE Cupboard
#5. HAZCHEM Documents Box
#6. Spill Kits
Safe Handling and Storage of Laboratory Chemicals
When you’re handling and storing laboratory chemicals, you need to maintain the highest levels of safety. Afterall, there are a range of risks associated with lab work including incompatible substances, hazardous spills and harmful vapours. Whether you’re running a small medical lab or a large commercial laboratory, it’s important that you maintain safety and compliance by adhering to the requirements of the Australian Standards.
AS/NZS 2243. 10:2004 – Safety in laboratories, Part 10: Storage of chemicals, details the controls your lab will need to implement to ensure your chemicals are being stored in the correct manner. This includes specifications regarding segregation in storage, the display of hazard identification information, management of movement of goods, and the storage procedures for laboratory chemicals.
Regardless of the size of your laboratory or your specific operations, there are some key chemical handling and storage products that your workplace will require to ensure the successful transfer, storage and segregation of your hazardous chemicals and dangerous goods. Read on to find out our top 6 chemical storage and handling products that every laboratory needs.
1. Chemical Transfer Equipment
Chemical spills can occur at any time. However, there is a particular risk of spillage when transferring chemical packages from delivery to storage areas and throughout your laboratory.
The decanting of chemicals is also is key spill risk for laboratories.
Chemical spillage isn’t just a waste of valuable stock — it can result in a range of issues for laboratory staff, including:
- Slippery floors which can result in falls and accidents
- The emission of harmful vapours, such as toxic vapours
- Risk of fire or explosion if flammable vapours meet ignition sources
- Potential damage to property and equipment if chemicals are corrosive
- Human harm caused by leaks and spillage, including eye damage, skin burns or asphyxiation
- Possibility for chemicals to react with other incompatible substances or materials
In addition to the risk of spillage, the transfer of chemicals throughout the laboratory can also put strain on the body. Carrying large packages or transferring heavy containers can increase the chance of back and neck strain, as well as accidents and injuries.
Chemicals can spill when they're being decanted or transferred.
To help create a safer working environment, it’s important that bunded handling and transfer equipment is utilized in a laboratory setting.
Such equipment may include gas bottle Rota trollies for the safe transport of cylinders or bunded trolleys for moving larger chemical containers throughout the laboratory.
#2. Compliant Chemical Storage
Whether you’re storing small bottles of toxic chemicals or cylinders of compressed gases, ticking the box for compliant chemical storage is essential when you’re working in a laboratory setting.
Each chemical that you have onsite must be stored in such a way as to meet the specific requirements of the product’s dangerous goods class.
If your chemicals have a further sub-class (such as a flammable liquid with a corrosive sub-class), then you must store your chemical to meet the Class 3 Flammable Liquids requirements, as well as ensuring that the requirements of the sub-class are also met.
Compliant storage is constructed in full conformance with the requirements of Australian Standards.
Compliant storage offers the highest levels of protection, as the design and construction of the storage equipment conforms with the Australian Standard. Storage provides a range of controls to minimise the harm posed by the chemicals, such as:
- Leak and spill containment
- Vapour containment or dispersion
- Security for kept chemicals
- Protection from impact damage
- Heat or fire barrier for flammable substances
-
Chemical segregation for that particular DG class
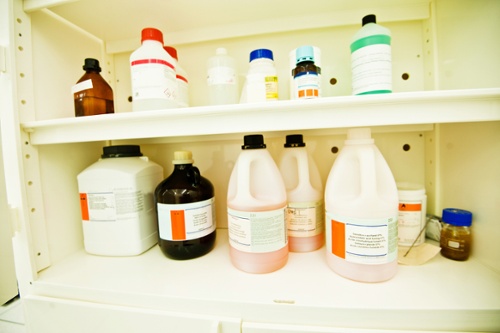
Compliant storage provides a wide range of control measures for hazardous chemicals.
In a laboratory setting, there are many types of storage that may be required, such as:
- Under fumehood and free-standing chemical cabinets – for the storage of each particular dangerous goods class
- Mechanically ventilated indoor gas cylinder storage – for the safe storage of laboratory gases
- Temperature-controlled storage – for chemicals which require specific temperature ranges for storage
- Bunded shelving – to prevent chemicals from spilling out into the workplace
- Drip trays – to catch leaks and spills from chemical containers
When selecting your storage equipment for laboratory chemicals, ensure that you carefully read the Safety Data Sheet of each chemical product to check the hazards and class of that substance. You should also conduct a risk assessment of your premises (with trained inhouse staff or through the consultation of a Dangerous Goods Consultant) to make sure that the equipment that you’re choosing sufficiently controls the risks that are present.
#3. Emergency Decontamination Equipment
Protecting your laboratory staff from harm is an integral part of your WHS obligations. Therefore, the installation of emergency decontamination equipment is one of the most significant factors for staff health and safety. There are many ways that lab staff can be harmed during their work day, including cuts from broken test tubes or beakers, chemical burns from harsh substances and eye damage caused by the accidental release of chemicals.
Safety showers and emergency eyewash facilities are key pieces of decontamination equipment. They must be positioned close to any potential chemical hazards, so that lab staff can quickly reach the facilities within a 10 second window.
To determine your need for eyewash or shower facilities in your laboratory, you must refer to the Standards and conduct an onsite risk assessment.
We highly recommend installing compliant facilities, such as a combination eyewash and shower, within 2-10 metres of any potential chemical hazards.
Emergency decontamination facilities are an essential item to reduce the risk of human harm.
In a laboratory setting, you may require one or more emergency decontamination stations to sufficiently protect your people from the chemical hazards that are present.
And just remember, it’s your duty under WHS Regulations to regularly test and maintain your emergency decontamination facilities to ensure they’re working as they should.
Need to know more about emergency decontamination equipment?
Access your free guide.
#4. PPE Cupboard
Laboratory work requires personal protective equipment for staff to be protected from exposure to hazardous substances. Through inhalation or contact with the skin or eyes, harmful chemicals can cause serious health problems if the correct PPE isn’t worn by workers.
However, not only is it important to choose the correct PPE, but you must also ensure that your staff know exactly how to use each item. This includes understanding how to properly put on the item of PPE – as well as take it off without risking chemical exposure.
In addition to this consideration, you must also maintain your PPE so it’s effective for the next time it’s used. This can be achieved through:
- Regular PPE inspections
- Swift repairs or replacements of damaged PPE
- Installing a dedicated PPE cupboard
A cupboard encourages diligent work practices, with staff able to quickly identify and retrieve their PPE, as well as having a safe place for the PPE to stay while it’s not in use. PPE cupboards are an important product to install in a laboratory setting, as it assists with maintaining the PPE — and ensuring its effectiveness and safety.
#5. HAZCHEM Documents Box
To properly handle and store chemicals in a laboratory setting, knowledge of the onsite materials is key. Lab staff must possess a good understanding of the chemical properties of each product.
Therefore, to assist with hazard identification and the minimisation of risk, the Safety Data Sheets of each chemical must be available to all lab staff.
Safety Data Sheets offer essential information about:
- Dangerous goods class
- Health hazards
- Physical hazards
- Chemical incompatibilities
- PPE requirements
- Environmental hazards
- General guidelines for safe handling and storage
- Emergency procedures
- First aid
Furthermore, adequate training and supervision should be implemented to make sure that all staff fully understand the information that’s listed on the Safety Data Sheets.
All laboratory staff must have easy access to every chemical's SDS.
As lab staff (and emergency services, in the event of a major spill, fire or other emergency) require fast, easy access to this chemical data, we suggest installing a hazmat box. The hazmat box is designed to contain a range of emergency documents including:
- Safety Data Sheets
- Emergency Plans
- Hazardous Chemicals Register
- Manifest of Hazardous Chemicals (if applicable to your laboratory)
Install your hazmat box in a prominent position, preferably at the entrance to your laboratory.
#6. Spill Kits
When working with hazardous chemicals, there is always the possibility of leaks and spills. Laboratories must be properly equipped to clean up and contain a chemical spill when it occurs.
Most spills in a laboratory will require a chemical spill kit, which is designed for use with most hazardous substances. Otherwise known as a HAZCHEM spill kit, these kits can be used to clean up and contain a range of substances from acids to caustic chemicals and toxic substances.
Safe Handling and Storage of Laboratory Chemicals
Keeping your laboratory safe from chemical hazards is an ongoing process of controlling and re-evaluating risks. These 6 essential items, including compliant chemical storage and emergency decontamination equipment, are vital for both safety and compliance. However, if you introduce new work practices to your lab or your chemical inventory changes in any way, it’s important to reassess your chemical hazards to ensure that your handling and storage equipment remains effective.
Like to learn more about chemical safety? Then why not access our free eBook? Our easy-to-read guide will introduce you to our 4-step risk control methodology, which can be applied to your laboratory today. Get your copy of our guide by clicking on the image below.
Joining the team as a Dangerous Goods Storage Consultant, Melissa Hampton became Storemasta's Marketing Manager in late 2021. With extensive knowledge and experience in chemical compliance, Melissa is responsible for leading the Marketing team and helping shape their marketing strategy. In her spare time, you can find Melissa hiking, swimming and enjoying the great outdoors in beautiful north-west Tasmania.