Does your business use flammable liquids on a regular basis? Then you understand how important it is to control potential risks by storing these dangerous goods in flammable storage cabinets. Afterall, it’s not just the flammable liquid that can cause serious hazards — flammable vapours are highly volatile and can quickly spread throughout a workplace and escape into the natural environment. A key risk control measure for flammable vapours is to install a ventilation system. That allows any hazardous vapours within your cabinet to be safely extracted and dispersed. In this blog, we’ll take a look at the flammable storage cabinet requirements for ventilation systems and also recommend some features of a compliant ventilation system.
But first, let’s take a closer look at flammable vapours.
What Are Flammable Vapours?
Flammable vapours pose a wide range of hazards for businesses, including human harm, fire, explosion and environmental damage. But what makes flammable liquids and their flammable vapours so dangerous in a workplace situation?
We’ll look at the definition of Class 3 Flammable Liquids as provided by the Australian Dangerous Goods code:
‘Flammable liquids are liquids, or mixtures of liquids, or liquids containing solids in solution or suspension (for example, paints, varnishes, lacquers, etc., but not including substances otherwise classified on account of their dangerous characteristics) which give off a flammable vapour at temperatures of not more than 60 °C, closed-cup test, or not more than 65.6 °C, open-cup test, normally referred to as the flash point.’
One of the most dangerous properties of a flammable liquid is the low flash point of the substance. As described above in the ADG code, flammable liquids emit flammable vapours at temperatures below 60°C. Due to the volatility of flammable vapours, it’s crucial that the vapours are controlled in a way that effectively minimises the risks.
Flammable liquids will give off hazardous vapours at temperatures below 60°C.
While your flammable cabinet is designed and constructed to provide a risk control measure for your workplace, there are some instances when the cabinet will require a ventilation system.
To determine if your organisation is vulnerable to the hazards posed by flammable vapours, you’ll have to familiarise yourself with the relevant cabinet ventilation requirements and apply them to your own workplace situation.
Flammable Cabinet Ventilation Requirements
There are two main resources that you can refer to when determining your flammable cabinet ventilation requirements. These are the Australian Standard AS 1940:2017 – The storage and handling of flammable and combustible liquids and workplace exposure standards. We’ll take a closer look at the Australian Standard before reviewing the requirements stated in the workplace exposure standards.
Australian Standards
AS1940-2017 - The storage and handling of flammable and combustible liquids is the standard that sets out the ventilation requirements for flammable storage cabinets.
Section 4.9.5 explains:
Where ventilation is installed, it shall be designed so that vapours are prevented from escaping into any room. Any ventilation exhaust shall be to the outside atmosphere and in a location which allows the safe dispersal of vapours and is away from any ignition sources (see Clause 4.5).
As this standard doesn’t state that a ventilation system “shall” be installed, it means that ventilation of flammable liquid storage cabinets is not a mandatory requirement. However, you should provide a ventilation system if it’s part of a risk control measure.
A flammable storage cabinet ventilation system can be an effective risk control measure.
An instance where ventilation would be required is if the flammable vapours inside the cabinet exceed the workplace exposure standards. We’ll explain those standards in detail now.
Workplace Exposure Standards
If workers are exposed to hazardous vapours, it can result in significant health risks.
Some of these risks include:
- Asphyxiation
- Nausea
- Headaches
- Vomiting
- Irritation to the eyes, ears and throat
- Dizziness
Flammable vapours can cause serious health risks for workers if they exceed the legal airborne concentration limits.
To combat these health risks, Safework Australia developed the workplace exposure standards. These standards identify approximately 700 hazardous substances and their legal airborne concentration limits.
If the flammable liquids stored inside your cabinet are listed in the workplace exposure standards — and the concentration of the vapours exceeds the legal limit — the flammable storage cabinet must be ventilated.
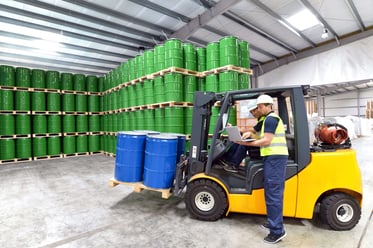
The ventilation system is designed and installed to reduce the concentration of the flammable vapours, so your workplace is safe for staff to work in.
Features Of A Compliant Ventilation System
So, you’ve carried out a dangerous goods risk assessment and determined that your flammable storage cabinets require a ventilation system? That’s a great first step towards chemical compliance.
Now it’s time to consider purchasing a ventilation system that will minimise the risks associated with storing your flammable liquids. However, when considering your ventilation options you should always keep in mind that the ventilation system must be designed and installed in a way that doesn’t create any further risks for your organisation.
If your cabinet requires a ventilation system as a risk control measure, the design, construction and installation must follow specific requirements
In short, you don’t want to make a compliant flammable cabinet non-compliant due to an inappropriate ventilation system.
A safe flammable cabinet ventilation system must follow the requirements outlined below:
- A mechanical ventilation system should be designed so that it prevents any vapours from escaping into the room.
- The ventilation system shall be vented to the outside atmosphere in a location that is safe to disperse vapours. A safe location will be away from ignition sources and places where people congregate.
- The air inlet shall be attached to the vent port at the top of the cabinet and the vapours shall be extracted from the bottom vent port using an exhaust fan. This configuration is most effective as most dangerous vapours are heavier than air and reside in the bottom of the cabinet.
- Any ventilation system that is used to extract flammable vapours will need to have an intrinsically safe exhaust fan.
- A ventilation system cannot be linked to multiple cabinets as this can cause incompatible vapours to mix, resulting in violent reactions.
- When a mechanical ventilation system is not attached to a cabinet, the vent bungs must be tightly screwed into the vent ports. This stops any dangerous vapours from escaping into the workplace.
- In all instances the ventilation system shall not compromise the structural integrity of the cabinet.
- In all cases the ventilation duct shall not be smaller than the size of the venting opening on the side of the cabinet.
- A ventilation system shall be designed by an appropriately qualified engineer and it shall comply with AS/NZS - 1668.2-2002 – The use of ventilation and airconditioning in buildings (part 2).
Understanding Your Flammable Cabinet Ventilation Requirements
Now that we’ve explained the volatility of flammable vapours and the hazards that they pose to workplaces, we hope you have a better understanding of your flammable cabinet ventilation requirements. It’s so important to choose a ventilation system that bolsters the compliance of your flammable cabinet — and does not create any further chemical risks for your organisation.
For a ventilation system to be safe, it must follow the best practices outlined above and comply with the requirements specified in the Australian Standard AS 1940:2017 – The storage and handling of flammable and combustible liquids.
If you’d like to learn more about the safe storage of flammable liquids, our team at STOREMASTA are here to help. We’ve been Dangerous Goods Storage Specialists for almost 30 years and can assist any business is achieving chemical compliance. If you’re interested in finding out more about the safe storage of flammable liquids, why not access our free eBook? Essential Considerations When Storing Flammable Liquids Indoors explains how to minimise the specific risks associated with storing flammables and offers our 4-Step risk control methodology, IDENTIFY - ASSESS – CONTROL - SUSTAIN, which you can apply to your own business. Get it free today by clicking the image below.
Joining the team as a Dangerous Goods Storage Consultant, Melissa Hampton became Storemasta's Marketing Manager in late 2021. With extensive knowledge and experience in chemical compliance, Melissa is responsible for leading the Marketing team and helping shape their marketing strategy. In her spare time, you can find Melissa hiking, swimming and enjoying the great outdoors in beautiful north-west Tasmania.