Renton Parker, Director of Riskcon Engineering, joins the podcast crew in this not-to-be-missed Chemical Safety at Work episode. From key issues with dangerous goods safety to the importance of knowledge and education, Renton discusses a broad range of topics relevant for any industry managing DG risk.
So, what led you to the dangerous goods industry?
I kind of fell into it, really. I studied chemical engineering at university, and through circumstances, I wanted to stay in Sydney. I ended up applying for an environmental engineering role, which turned out to be a chemical engineering role within an environmental team. I started working in the industry, found it really interesting and engaging, and I’ve been in it ever since.
What does a chemical engineering role in an environmental team look like?
It was a large consultancy that categorised teams by industry focus — environmental, mechanical, mining, and so on. My role was within the environmental team, so it was labelled as an environmental engineering position, but in practice, it was entirely chemical engineering.
How did you transition from there to founding Riskcon Engineering?
I’ve essentially been doing the same role for 12 years now. I worked for a few different companies along the way and realised early on that, because the field was quite niche, there was an opportunity to start my own company. I teamed up with my mentor in 2018 to establish Riskcon Engineering. We've been operating for six years now, continuously growing and helping our clients.
What industries do you primarily focus on?
We cover a broad range of chemical processing industries, including mining, warehousing and logistics, oil and gas, food and beverage, and pharmaceuticals — essentially anywhere chemicals are stored or where risk management is required.
What behaviours and attitudes towards safety have you observed in your experience?
As consultants, we primarily engage with businesses that already have some awareness of the risks they face, often due to regulatory involvement. Our experience is somewhat biased because we mostly interact with those already seeking solutions.
However, there’s a large portion of businesses and individuals who don’t fully understand their risks, and therefore, they aren’t managing them properly.
Chemical Engineer & Director of Riskcon
What is the biggest threat to Australian businesses regarding dangerous goods?
Knowledge. Many people are never formally taught about dangerous goods and their associated risks. As a result, hazards often go unrecognised and unmanaged.
Additionally, universities don’t emphasise chemical management and storage, so graduates entering the industry are often unaware of best practices.
Where should the push for better knowledge and education come from?
Each state's regulations require employers to educate their employees, but this doesn’t necessarily extend to the educators themselves. Universities focus on providing a broad education, meaning graduates often lack specialised knowledge in chemical safety. Businesses need to take responsibility for bridging this gap.
Do you have any real-world examples of incidents you've encountered?
A recurring issue involves static electricity. While fixed electrical installations in hazardous areas are well-regulated, static discharge is often overlooked. One incident involved a client who cleaned a mixing vessel with a solvent and then covered it with plastic to contain flammable gas. The procedure required the vessel to be earthed before removing the cover, but the employee forgot. When they removed the plastic, the static discharge ignited the vapour. Fortunately, they weren’t seriously injured, but it could have been a major incident.
What improvements could be made at a national level to reduce incidents and accidents?
Regulators are already doing a great job providing guidance and support. Organisations like the Australasian Institute of Dangerous Goods Consultants (AIDGC) also offer resources and lists of consultants. Businesses just need to recognise what they don’t know and seek expert advice.
Are you seeing new technology or innovations improving dangerous goods safety?
Absolutely. Battery safety, for example, has become critical, and solutions like Storemasta’s storage cabinets are addressing these risks. Electrical safety is also well understood, with international standards constantly evolving. While existing safety measures remain relevant, new industries — such as hydrogen energy — drive the need for innovative safety procedures and equipment.
What about software and AI? Are digital solutions helping businesses manage risks?
Software tools are great for documenting and tracking risks, but the first step is always identifying hazards, which doesn’t necessarily require advanced technology. Once risks are understood, software can help manage them through schedules, maintenance tracking, and procedural documentation.
What’s in store for Riskcon in 2025?
We’ve been involved in a lot of distillery and renewable energy projects lately. That seems to be where the industry is growing. However, trends shift every few years, so we’ll see where the future takes us.
To stream the full Chemical Safety at Work™ episode, visit your favourite podcast platform or watch the complete video on Youtube.
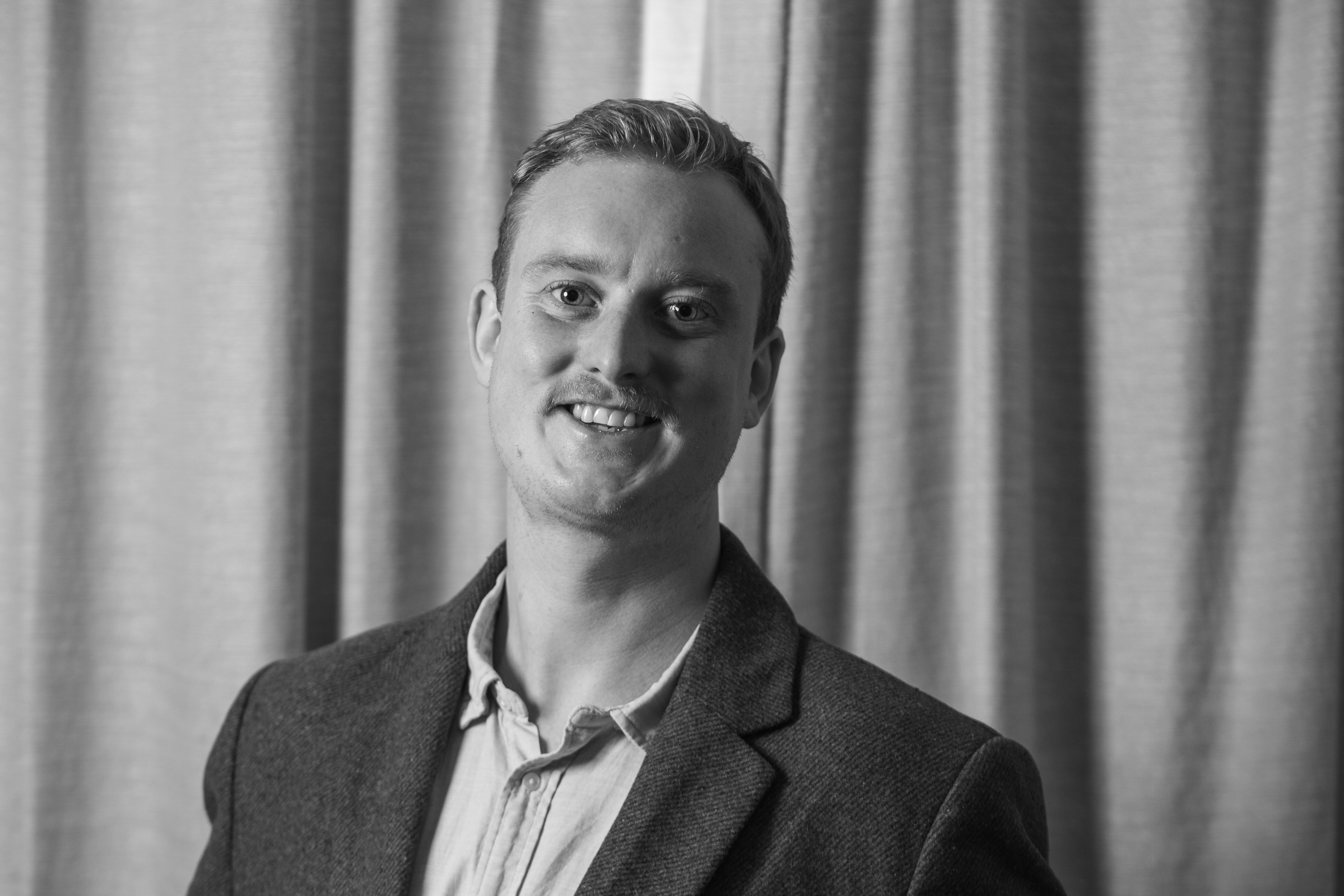
Patrick Gee is Storemasta’s Content Creator and Marketer. With background in journalism, Patrick is passionate about using his communication and photography skills to help organisations find safe solutions for dangerous goods storage. His Instagram is filled with pictures of his dog Milo, along with his travels throughout Australia and overseas.