Gas Cylinders in the Workplace
Gas Cylinder Handling
Gas Bottle Handling Risks and Hazards
Requirements for Handling Gas Cylinders
Handling Compressed Gas Cylinders?
Compressed gases in cylinders are classed as dangerous goods, and therefore, should only be handled by staff and contractors trained in correct handling techniques. This post looks at gas cylinders and highlights how they’re used in the workplace, as well as the risks that they pose to health and safety. We’ll also explain how you can control these risks by understanding how to safely handle gas cylinders in the workplace.
Gas Cylinders in the Workplace
Compressed gases are used in homes and workplaces all over the world. The unique chemical properties of gases and other hazardous chemicals make our comfortable 21st century lives possible.
Some examples of industrial applications of compressed gases include:
- Fuels gas cylinders such as liquidfied petroleum gas (LPG) powered forklifts, gas heaters in restaurants and welding torches in workshops;
- Toxic gases like chlorine purify water treatment plants and swimming pools
- Pure oxygen gas is used for yeast activation and preservation in wineries, industrial welding, and medical treatment
- Oxidising gases like nitrogen dioxide is used to bleach flour and it’s also an ingredient in rocket fuel
- Reactive gases like acetylene are used for welding and industrial cutting
- Corrosive gases like ammonia is used to refrigerate cold storage plants, and manufacture plastics
- Industrial gases like helium, hydrogen, argon and nitrogen are used to maintain laboratory instruments
NOTE: Compressed gas bottles are never completely empty, so make sure that your staff understand that your ‘empty cylinders’ still pose a risk. Even if the cylinder gauge reads 0, residual gas will always remain in the cylinder. Segregate and store your empty cylinders, treating them with the same caution as your full gas cylinders.
Gas Cylinder Handling
Cylinders that contain compressed gases are pressurised vessels which must be handled and stored in a way that reduces risk. Gas cylinders must always be kept in the upright position and restrained to avoid instability and damage.
The cylinder themselves are heavy and awkwardly shaped, so handlers are vulnerable to manual handling injuries like sprains, strains, falls, bruises, or broken bones. It’s a much safer and simpler option to use a gas cylinder trolley when transporting compressed gas cylinders through your work site.
If cylinders are dropped, impacted or knocked over, they create additional hazards if the gases are accidentally released.
Moving gas cylinders around a job site can create additional risks to people and property, so it’s a safe option to use a gas bottle trolley.
Gas Bottle Handling Risks and Hazards
Catastrophic hazards are all very possible if gases leak from damaged cylinders. Some examples of hazards caused by dropped or damaged cylinders may include:
- Fires
- Explosions
- Chemical burns
- Cold burns
- Fatal exposure to toxic and corrosive gases
- Impact from cylinders in ‘torpedo-like’ momentum
- Asphyxiation from oxygen displacement
- Handling gas cylinders safely
Requirements for Handling Gas Cylinders
To keep your workplace safe and 100% compliant with Australian safety legislation, follow the guidelines of AS 4332:2004 - The storage and handling of gases in cylinders. We’ll detail some of the minimum requirements for handling compressed gas cylinders in the next section of our post.
Gas cylinders can cause harm to people and property if they're not restrained and positioned upright.
1. Mechanical Lifting Devices are Used When Transporting Cylinders
A worker suffered multiple fractures and was hospitalised after a cylinder he was moving tipped over and crushed his leg. This accident might have been prevented if the worker had used a forklift to move the cylinder.
The Standard requires that cylinders must only be lifted and transported with a mechanical lifting device (like a forklift), and care should always be taken to ensure that cylinder valves are always protected from damage.
Cylinders must never be dropped or rolled over the side of trucks.
2. Gas Cylinder Valves are Protected
A worker was on a ladder while soldering pipe. He placed the torch cylinder on a wooden beam in between welds, which subsequently fell to the ground. The cylinder neck cracked open, and the cylinder was engulfed in flames. The worker suffered 3rd degree burns as he tried to jump from the ladder.
To avoid incidents such as this, the Standard requires a purpose-built gas bottle trolley or cage that has individual restraints. These restraints will protect the gas cylinder valve and regulator from damage.
Need to learn more about safe DG storage?
3. Cylinders are Securely Restrained
A worker checking cylinders for leaks was killed after being struck by a loose cylinder that was propelled into the air as gas began dispensing rapidly.
This workplace accident is tragic example of why the Standard requires cylinders to be kept upright — and securely restrained at all times. You should store gas cylinders in a compliant manner, with ample natural ventilation, secure restraints and a durable cage to prohibit impact damage.
4. Appropriate PPE is Provided for Employees
Using substandard personal protective equipment can result in injuries and accidents. This occurred when an employee received 2nd degree burns to his hands while wearing cotton when changing an LPG cylinder.
Always consult the Safety Data Sheets (SDSs) for each of the gases handled and stored at your worksite and make sure the personal protective equipment is well maintained and easy to find.
5. Staff are Given Clear Instructions and Adequately Trained
Two workers were killed, with another seriously injured, when they were carrying LPG cylinders down some stairs. One worker dropped a cylinder, which impacted another worker — before causing an explosion.
It’s essential that staff understand the chemical properties of the gases they use and handle, as well as the hazards associated with the cylinders. They must be given clear and specific manual handling procedures as well as ongoing re-training.
Remember, the handling operation can always be improved, so make sure that you’re ensuring your staff always receive up-to-date training on gas cylinder handling.
Other gas cylinder handling best practices:
- Transport gas cylinders with the value closed, and the cap in place
- Never use a gas cylinder valve or cap to lift or move the bottle
- Do not accept a cylinder, such as liquefied petroleum gas or other compressed gases, from a gas bottle supplier that has no labels or identification. Never rely on the colour alone to identify the gas inside the cylinder
- Visually inspect your gas cylinder and don’t accept anything that appears damaged, corroded or out of test date
- Don’t try to catch a falling cylinder, get clear
- Have your cylinders regularly tested and serviced by qualified technicians
- Never drag or slide a cylinder, even for short distances
- Don’t tamper or remove cylinder labels, markings or paintwork
Handling Compressed Gas Cylinders?
If you handle and store gas cylinders at your workplace, we strongly encourage you to download our eBook Gas Cylinder Storage: Compliance and Safety Requirements. In this free guide, we unpack AS 4332-2004 - The storage and handling of gases in cylinders and detail how you can better manage the risks and hazards associated with compressed gases through careful handling and storage practices. Find out more about gas cylinder safety and reduce risk at your site.
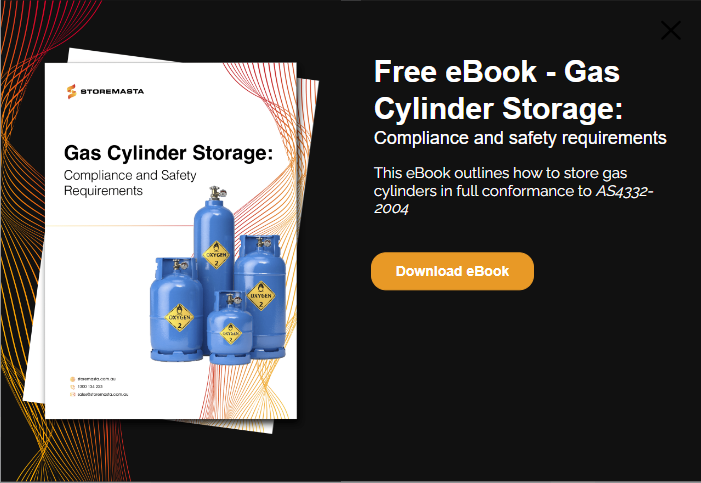
Joining the team as a Dangerous Goods Storage Consultant, Melissa Hampton became Storemasta's Marketing Manager in late 2021. With extensive knowledge and experience in chemical compliance, Melissa is responsible for leading the Marketing team and helping shape their marketing strategy. In her spare time, you can find Melissa hiking, swimming and enjoying the great outdoors in beautiful north-west Tasmania.