‘How long should I wait before reviewing flammable liquids control measures?’ It’s a question our team often get asked by customers who have implemented a hazard control measure for their business. Many people forget that equipment such as flammable liquids cabinets, chemical decanting equipment, and specific items of PPE aren’t simply off-the-shelf purchases. Instead, they are pieces of high-tech, specialised equipment that should only be purchased and installed to address specific hazards (that have been identified in a risk assessment).
In this blog, we’ll be explaining your legal requirements in relation to periodically reviewing your flammable liquids cabinets. This also applies to other engineering control measures, such as outdoor chemical stores, spill bunding and decanting systems.
Let’s get started by unpacking what the law says about your obligations — and illustrating what that looks like on a standard job site.
REMEMBER: Reviewing hazard control measures is an essential requirement under Australian WHS Regulations in every state and territory.
What The Law Says About Reviewing Hazard Control Measures
Any business holder who has introduced a hazard control measure to minimise health and safety risks has responsibilities in three different sections of the Model WHS Regulations.
Every Australian business has a responsibility to minimise health and safety risk.
These responsibilities are as follows:
- Section 37: to ensure hazard control measures are maintained so they remain safe, effective, fit for purpose, installed and working correctly.
- Section 38: to carry out a review if there are indications that a hazard control measure isn’t working, or if new hazards have emerged.
- Section 352: to review chemical hazard control measures at least once every 5 years — or if:
- Chemical’s Safety Data Sheet (SDS) is updated
- Register of Hazardous Chemicals is updated
- There are indications that workers may have developed adverse health conditions.

We’ll now go into more detail about each of these responsibilities in detail below — and use examples that may be applied to your own workplace.
How You Can Carry Out Hazard Control Reviews
To comply with work health and safety legislation, Australian businesses must review their flammable liquids storage and decanting equipment at least once every 5 years WHS Regulations Section 352 (d).
But in daily practice, it’s unlikely that you would wait this long. We’ve detailed 3 checks that we suggest you carry out to ensure you’re minimising chemical risk in your workplace.1. Post Installation Checks
A flammable liquids cabinet or decanting system should be reviewed within a few days of installation.
Our Dangerous Goods Specialists always recommend post installation checks that include:
- Installation and setup — is the cabinet on a level surface and not blocking an emergency access point? Are the self-closing doors working? Are warning signs clearly visible? Is there enough lighting in the area? Are there ignition sources or power points within 3 metres of the cabinet?
- Correct usage — has the cabinet been loaded past the capacity rating? Are there chemicals being stored in the spill compound? Are incompatible substances also inside the cabinet?
- Fit-for-purpose — is the cabinet big enough for the chemical quantities? Is an indoor cabinet being used outside?
We suggest that you perform regular checks on your flammable cabinet and outdoor stores including checks on the installation and setup of the cabinet.
2. Review Triggers
Section 38 and 357 of the Regulations outline a range of incidents that must trigger a review of your flammable liquids gear.
There are many incidents which may trigger a review of your flammable cabinet or other hazard control measures including chemical leaks or fumes being emitted from the cabinet.
Incidents which may trigger a review include:
Section 38 Model WHS Regulations
- Something isn’t working — is there any evidence that vapours or liquids are leaking from the cabinet? Eg, people working near the cabinets complain of headaches or they can smell fumes.
- Changes to the workplace — have chemical quantities increased since purchasing the flammable liquids cabinet? Eg, production schedules increase, and more chemicals are being ordered, there are times when chemicals are left outside overnight.
- New hazards — has a new (or previously unknown) hazard been identified? Eg, an electrical contractor installs a power point next to the flammable liquids cabinet.
- Consultation — has consulting with chemical handling staff made you aware of additional safety issues? Eg, workers are having trouble carrying out decanting processes while using their PPE.
- Request from HSE Representatives — has an appointed HSE Representative made a formal request for a review? Eg, workers are concerned the chemical decanting equipment has deteriorated and needs replacing.
You may have to consider if the chemical quantities that you are currently using are still applicable for the capacity of your flammable cabinet.
Section 352 Model WHS Regulations
- Safety Data Sheets (SDS) — has there been any changes to a Safety Data Sheet (SDS) or the Register of Hazardous Chemicals? Eg, a new chemical is introduced to the job site.
- Health Monitoring — is there any evidence that a worker may have contracted a disease, injury, or illness from chemical exposure? Eg, a worker develops chronic asthma and a doctor recommends health testing for chemical metabolites.
- 5 years — has it been more than 5 years since you carried out a review? Eg, you must carry out a risk assessment review.
If there has been a change with your Safety Data Sheet or the Register of Hazardous Chemicals, you’ll need to review your Dangerous Goods equipment.
3. Ongoing Compliance Checks
The best way to ensure you are always in full compliance with the WHS Regulations is to carry out regular inspections and safety audits.
Ongoing compliance checks can include:
- Housekeeping checks — chemicals put away, lids and caps in place, cabinet doors not propped open, decanting containers labelled properly.
- Integrity checks — cabinet doors working correctly, no dints or structural damage to cabinet walls and seams, lube stations pumping at correct capacity.
- Maintenance — replacing missing or damaged parts.
- Compliance checks — ensuring signage is in place, cabinets aren’t overloaded, ignition sources are not in decanting areas.
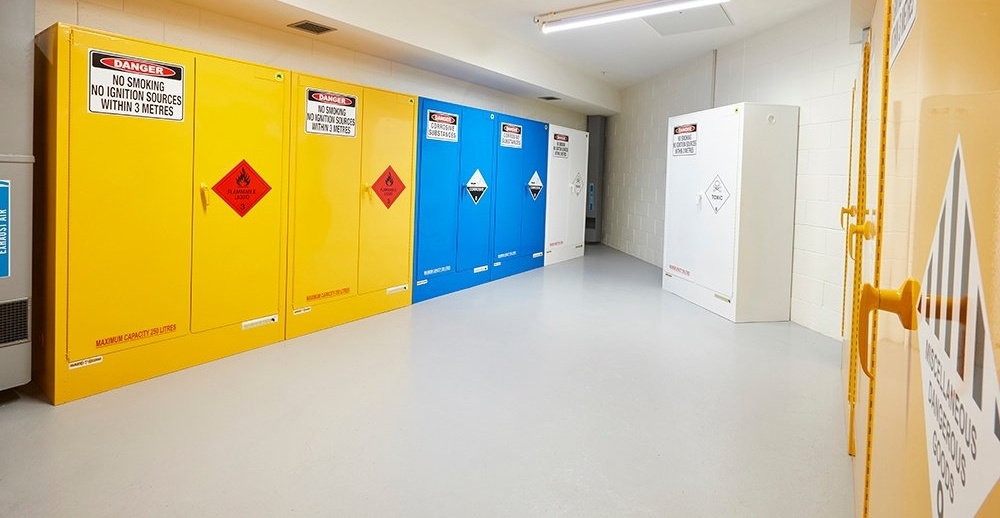
To comply with WHS Regulations, you must ensure that good housekeeping practices are maintained, including closing the flammable cabinet properly and labelling decanting containers correctly.
When Did You Last Review Your Flammable Liquids Control Measures?
Has it been a while since you’ve checked your flammable liquids storage and decanting equipment? Then we hope we’ve educated you about your obligations under WHS Regulations — and how you can easily review control measures in your own workplace. If you’re thinking about conducting a review of your Class 3 Flammable Liquids storage areas, we encourage you to first download our handy eBook. Essential Considerations When Storing Flammable Liquids Indoors can be used as the basis for a compliance review, site inspection or risk assessment. And best of all, it’s completely free. Grab your copy today.
Joining the team as a Dangerous Goods Storage Consultant, Melissa Hampton became Storemasta's Marketing Manager in late 2021. With extensive knowledge and experience in chemical compliance, Melissa is responsible for leading the Marketing team and helping shape their marketing strategy. In her spare time, you can find Melissa hiking, swimming and enjoying the great outdoors in beautiful north-west Tasmania.