Creating a safe chemical storage area isn’t just a simple one-step process, but it doesn’t have to be a complex issue, either. Once you’ve selected and installed your chemical storage cabinet, there are practices and procedures that you should put in place, so your team are all on the same page about chemical safety. While using a chemical cabinet may first appear like a simple task, you’d be surprised how often we hear of staff using or maintaining their equipment in an unsafe way. To find out what you should not be doing with your indoor DG storage equipment, keep reading to find out the 9 things you shouldn’t do with your chemical storage cabinet.
1. Store The Wrong Type Of Chemicals
To determine the type of cabinet required for your chemicals, you will need to refer to the Safety Data Sheet of your individual products to find the applicable dangerous goods class.
As many classes of dangerous goods are incompatible with other classes, it’s vital that you only store the correct chemicals in your cabinet. In some circumstances, chemicals within the same dangerous goods class may even be regarded as incompatible.
So, always check with the SDS of each chemical product that you’re considering storing in your cabinet to ensure that it’s the right match for the cabinet.
2. Overload Shelves
Overloading your cabinet can reduce the effectiveness of the control measures and increase the risk of spillage and hazardous vapour emissions. Shelving should always be adjusted to suit the requirements of your chemical packages. You should allow packages to sit comfortably on the shelf, so that they don’t inhibit the self-closing mechanisms of the doors or stop the tight-closing doors from shutting properly.
Make sure that cabinets aren’t overloaded past their maximum capacity, as this will put your organisation at risk of non-compliance. How you stack and load your cabinet is also important for reducing the risk of packages falling over and causing a hazardous chemical spill.
Don't overload the shelves in your cabinet as this can increase the risk of hazardous spillage and render your cabinet non-compliant.
3. Ignore Spillage
Whether a spill has occurred, whether it’s noticed by staff or not, it must be immediately cleaned up to reduce risks such as harmful vapours, chemical burns, fire or explosion. If a spill does occur when staff members are using the cabinet, the appropriate staff must be notified so they can clean out the spill containment sump.
IMPORTANT: Compliant cabinets are designed with a spill containment sump in the bottom of the cabinet. Any spill or leak which occurs in the cabinet will be directed into this sump. The sump can be cleaned up by soaking up the spill with a chemical pad. Alternatively, you may use a pump to collect larger spills within the sump.
Remember also to wipe over the interior of the cabinet, as well as any affected chemical packages, to clean away hazardous chemical residue within the cabinet.
Spills or leaks which are not noted by staff can be tended to through regular inspections and housekeeping of the cabinet. We recommend checking your cabinets daily (or conducting set weekly inspections if this is not possible) for any signs of spills or leaks. Without developing a set procedure for cabinet inspections and housekeeping, you won’t be able to adequately maintain your spill sump and reduce the risks associated with hazardous spillage.
4. Prop Open The Cabinet Doors
Chemical cabinets are designed with an automatic door closing system. This ensures that the doors close tightly every time the cabinet is not in use. However, there are some circumstances which may require the doors of the cabinet to be held open for some time by a staff member or a door opening device.
While loading new chemicals into the cabinet or cleaning out the cabinet may be a necessary task that requires the doors to remain open, it’s important that the doors are closed as soon as the cabinet is not in use.
Compliant cabinet doors are specifically designed to contain spillage and vapours. The doors also provide a barrier that will protect the contents of the cabinet in the event of a workplace fire. Self-closing, tight-fitting doors also provide a protected and secure storage space for your hazardous chemicals.
Sometimes staff may keep the doors open by placing a heavy item in front of the doors, or by wedging a piece of timber in the door frame. When unsafe practices like this occur, you’re not only negating the effectiveness of the cabinet — you’re increasing the risk of fire, spillage, chemical misuse, theft and harmful vapours.
Leaving the doors of the cabinet open also exposes your stored chemicals to possible impact damage. It also strips away any segregation barrier that the double-walled sheet steel cabinet would usually provide.
5. Forget To Label Containers
Are your stored chemicals kept in a suitable container that’s tightly secured with a lid? Are your containers properly labelled so that staff are aware of the chemicals stored — and their hazards?
One of the basic rules of chemical safety is making sure that staff are aware of the chemicals that they’re handling, as well as the associated hazards presented by the chemical. This not only allows for the safe handling and storage of chemical containers, but it is a requirement under WHS Legislation.
All types of chemical packages, whether they’re bags, containers or drums, should be clearly marked with the appropriate GHS labels. If you’re transferring chemicals to other containers, they must be labelled immediately to avoid staff unknowingly using the chemical in an unsafe manner. This includes any chemicals which may be placed in portable containers, such as jerry cans or spray bottles.
REMEMBER: Hazardous chemicals will leave a residue in any type of chemical package or container that they’re placed in. These containers still pose the same risks as the chemical itself. Don’t place chemicals in containers without ensuring that the previous chemical was compatible. Also ensure that any cracked, damaged or aged containers are disposed of in a safe and compliant manner. Consult your local government for further guidance on safe chemical container disposal.
6. Put Other Items In The Chemical Storage Cabinet
Your cabinet is a high-tech piece of dangerous goods storage equipment that is constructed to reduce risk for the class of chemical that you’re storing. So, why would you place anything other than the appropriate chemicals in your cabinet?
Whether it’s lack of space, lack of knowledge or just a lack of time, staff sometimes throw usual items into their safety cabinets. Items such as paperwork, SDS, cleaning rags, dustpan and brushes, tools and PPE can sometimes find their way into chemical cabinets. Not only is this creating further risk for your stored chemicals, it’s also a waste of valuable chemical storage space and an inefficient way to store your other workplace items.
We suggest having designated storage areas for each of your essential items, such as:
- Document storage box for your SDS
- PPE Cabinets for your personal protective equipment
- your various pieces of personal protection equipment
- Tool cabinets for your workplace tools
- Cleaning equipment cabinet for your rags, dustpan and brushes and other items
REMEMBER: Always remove the packaging before you place chemicals in your cabinet. Packaging, such as cardboard boxes, can increase the risk of fire or explosion in flammable safety cabinets.
7. Not Attach Your SDS
It’s a requirement of WHS Legislation and Australian Standards that SDS are readily available for staff and any emergency services which may attend your site. Therefore, attaching your SDS to a document holder attached to your cabinet is one of the simplest ways to make sure that the SDS is always accessible.
A document holder will provide a dedicated and protected space for your chemical SDS. Each cabinet should be fitted with its own document holder that features the SDS of each chemical product stored in the cabinet.
Keeping your SDS in a dedicated folder that's attached to a document holder on your cabinet is an easy way to maintain compliance.
8. Have Untrained Staff Use The Chemical Cabinet
It seems like common sense that a staff member using a forklift or a truck would require the appropriate training in order to drive the vehicle. However, there are some instances where staff members are using a hazardous chemical cabinet without adequate chemical safety training.
Just as a vehicle can cause damage to the staff member driving it — as well as the people, property and environment in the surrounding area — a chemical cabinet can be used in an unsafe way.
Implementing a training program for your staff is a key consideration when installing a chemical cabinet. Staff should be able to understand the features of the cabinet and how to use it correctly. They should also be trained in how to identify and reduce the risks associated with the chemicals that they’ll be handling and storing.
9. Not Consider Emergency Decontamination
Have you conducted a risk assessment to determine if your chemical storage cabinet requires emergency decontamination facilities nearby? Depending on the class and quantity of chemicals that you’re storing, you may be obliged to install equipment within 2 to 10 metres of your cabinet.
As we know, many chemicals pose serious health hazards to the staff that handle and store them. Whether it’s toxic poisening from Class 6 substances or eye damage caused by corrosive chemicals, it’s crucial that staff can access emergency decontamination equipment in the event of an accident.
The Australian Standards explain that eye wash units, emergency showers and first-aid equipment be located within a 10 second reach of your chemical store. We recommend conducting a thorough risk assessment of your storage area to determine if these facilities are required for your chemical cabinet.
How are You Using Your Chemical Cabinets?
Installing a compliant chemical storage cabinet is just the first step towards creating a workplace that is free from chemical hazards. As we’ve highlighted in our post, there are many practices that should never occur within or near your chemical store. Understanding how to install, use and maintain your cabinet will help you achieve higher standards of chemical safety in your organisation.
To find out more about using safety cabinets, you can download our guide, Essential Considerations When Storing Flammable Liquids Indoors. Our guide will help you look after your chemical cabinet, with specific tips for organisations that are carrying flammable substances. Grab your own copy of our guide today by clicking on the image below.
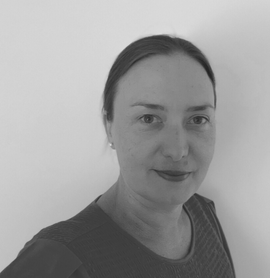
Living life by the 4 C’s of marketing – communication, coffee, compliance… and more coffee – Leisa Andersen is Storemasta’s Content Marketing Manager. When she’s not writing, you’ll find her enjoying all the good things in life, including shopping, travel and gluten free donuts.